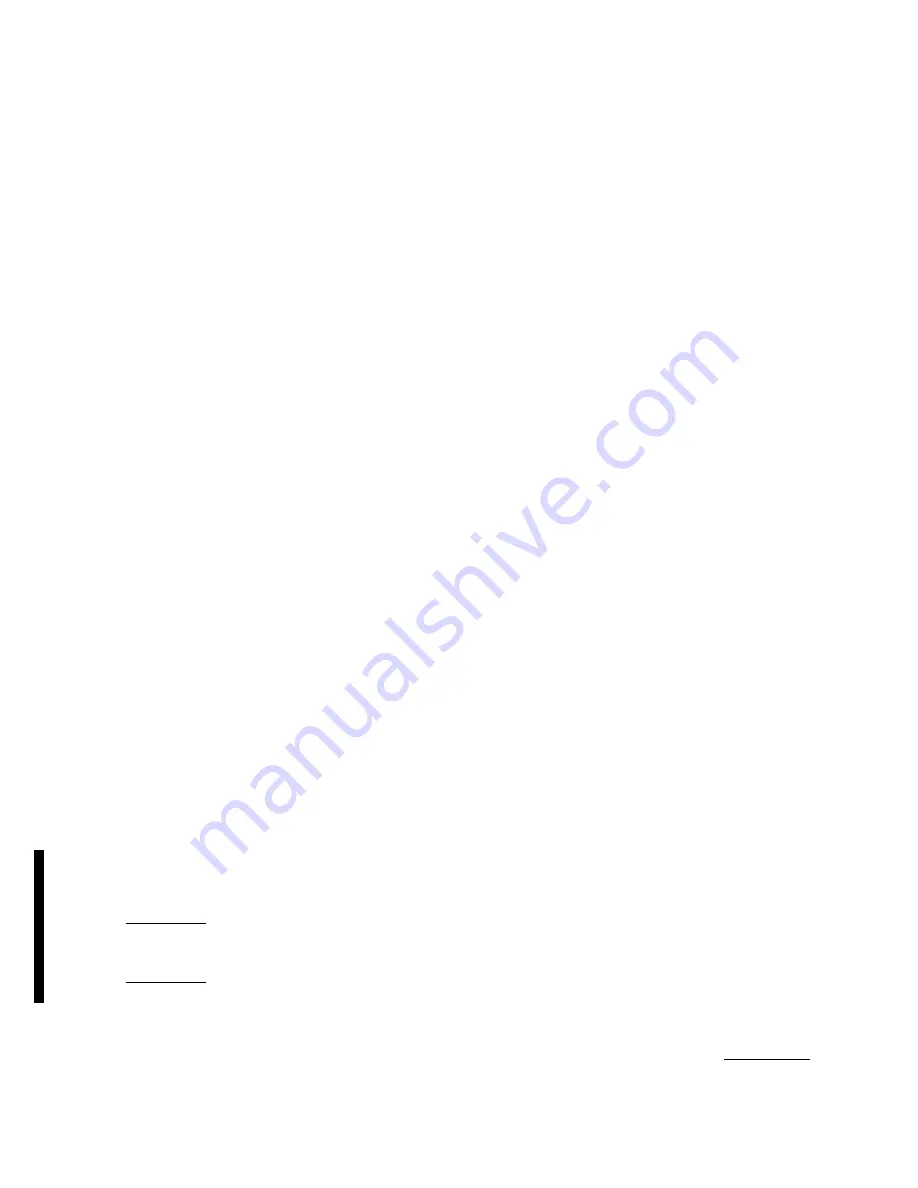
CSP−HMI−2
MD Helicopters, Inc
.
MAINTENANCE MANUAL
Page 606
Revision 39
67−10−00
6. Collective Control Interconnecting Torque
Tube Inspection
(1). Remove pilot’s seat cover, control access
door, and left side foot support fairing.
(2). Inspect collective interconnecting
torque tube for cracks, bends or
distortions.
(3). Inspect bungee bracket and bungee
fitting for security and condition.
Ensure cotter pin in over−center
adjustment bolt is not sheared.
(4). Inspect all accessible rivets for play.
inspect support bearings for security
and evidence of binding.
(5). Reinstall pilot’s seat cover, controls
access door and foot support fairing.
7. Collective Bungee Inspection
NOTE:
Replace any bungee parts in question-
able condition.
(1). Inspect bearings in male and female
bearing assemblies for evidence of
binding, corrosion and galling.
(2). Inspect female bearing assembly
threads for damage.
(3). Inspect spring for evidence of deforma-
tion. Free length of spring must be;
(a). Effectivity: 369D/E/FF−500N, 3.64
±
0.06 inches (92.456
±
1.524 mm)
(b). Effectivity: 600N, 4.50
±
0.025 inches
(114.30 +0.635 mm
)
(4). Inspect male bearing rod for cracks,
evidence of binding, corrosion and
deformation.
NOTE:
Bungee support bracket may be either
an aluminum or magnesium casting. (For
corrosion control and identification of mag-
nesium and aluminum alloys, Ref. Sec.
20−40−00.)
8. Inboard Collective Stick Socket Assembly
Inspection
(1). Inspect all bearings for binding or play.
(2). Inspect gears for cracks, and chipped or
broken teeth.
(3). Inspect all components for cracks,
corrosion and deformation.
NOTE:
Bellcrank and idler may be either an
aluminum or magnesium casting. (For cor-
rosion control and identification of magne-
sium and aluminum alloy parts, Ref. Sec.
20−40−00.)
9. Pilot’s Cyclic Control Stick Inspection
NOTE:
D
For this inspection, friction stop nut must
be loosened.
D
Socket may be either an aluminum or
magnesium casting. (For corrosion con-
trol and identification of magnesium and
aluminum alloys, Ref. Sec. 20−40−00.)
(1). Inspect stick tube attachment to socket
for evidence of loose rivets, distortion
and corrosion.
(2). Inspect parts of friction mechanism for
physical damage. Free length of friction
spring should be approximately 0.580
inch (14.732 mm).
(3). To check installation, loosen lateral and
longitudinal friction knobs, move cyclic
control stick and check for binding or
unusual noises. Check that rod end
bearings of pilot’s lateral control rod do
not jam when stick is full forward and
full aft.
NOTE:
Set minimum friction so that phenolic
washers can be slightly turned by hand. If
minimum friction is set too low, stick shake
will occur.