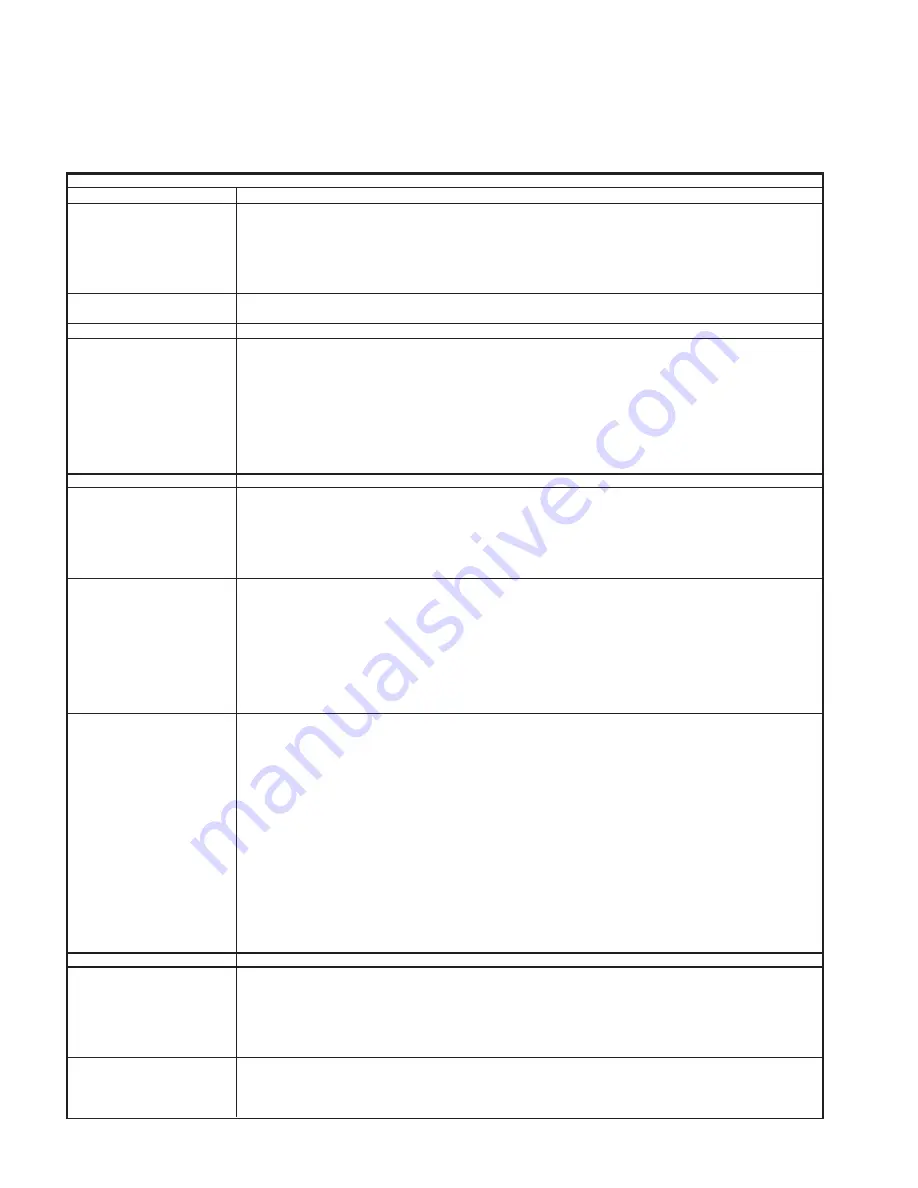
Page 26 / IM 685
Troubleshooting Guide
The RM7895A flame safeguard is equipped with five LEDs to aid in the diagnosis of burner operation and problems. In
addition, a Keyboard Display Module is available and is a valuable aid for indicating flame signal DC volts, fault messages,
sequence status, etc. See “Flame Safeguard (RM7895A)” for additional information on the Keyboard Display Module and for a
description of the function of the LEDs. Some of the steps listed in this troubleshooting chart will be unnecessary if a Keyboard
Display Module is used, as that module will pinpoint many problems.
BURNER MOTOR DOES NOT RUN (AFTER 10 SECOND “INITIATE” PERIOD AND WITH SWITCH AT AUTO):
1.1 Power LED is off.
a. Power is not getting to burner.
1.2 Entire unit seems to be off.
a. Burner power comes from the main control panel which has a main disconnect switch, a stepdown transformer with
primary winding fuses, a 120V secondary winding fuse, and an on-off service switch. If any of these were open, the
burner as well as the supply fan would be inoperative. The control system also has firestat type temperature sensors
which will shut down the entire unit if supply or return air temperatures exceed set points. On some control systems
the firestats only lock out the supply and return fans. Check main control schematic as these would not be burner
problems.
1.3 Supply fan will operate.
a. Check the manual reset limit control located between the filters and the supply fan and reset if required.
b. Check that the control system has energized relay R20 located in the burner control box.
1.4 Power LED is on.
a. Push the reset button on the flame safeguard.
1.5 Resetting flame safeguard
a. Push the reset button on the burner motor. (Note: If motor is hot and probably tripped, it has to cool sufficiently
does not start motor after
before it can be reset.)
the 10 second “Initiate”
b. Test for line voltage across burner terminal 8 and NB. If powered, the problem is with the burner motor or its associated
period is completed.
controls. On Models 1100-2000, terminal 8 only controls a contactor and burner motor power comes from its own
circuit breaker. If terminal 8 is dead, check for power across terminals 1 and NB.
c. IF VOLTAGE IS ZERO: The power is being interrupted by the limit control, the manual reset high or auto reset low
gas pressure switches (if included), or relay contacts (R20). Consult the schematic and determine the interruption.
d. If voltage is satisfactory across terminals 1 and NB and terminal 8 does not become energized after 10 seconds, and
pressing the safety reset button has no effect, replace the RM7895A.
BURNER MOTOR RUNS, BUT . . .
2.1 Burner motor runs
a. Switch LS2 is not being actuated by the collar on the control rod when at the maximum rate position.
valve actuator travels to the
b. The air proving switch AS is not sensing burner fan pressure. Check the connecting tube, setpoint, and wiring.
maximum rate position and
If LS2 and AS are functioning, 120 volts can be measured across terminals 7 and L2 on the flame safeguard
stays there, the Keyboard
when the burner fan is running.
Display Module indicates
"Purge Hold".
2.2 Burner motor runs, valve
a. Timer TD10 is not 'making' after 20 seconds. Check that there is 120 volts on TD10 tab 1 when the actuator is at
actuator travels to the
the maximum rate position. TD10 tab 2 should become energized 20 seconds after tab 1 is powered.
maximum rate poistion and
b. Relay R21 is not being energized by TD10, check for power across C1 and C2 after TD10 has become energized
and replace R21 if indicated.
stays there, the Keyboard
Display Module goes
through the prepurge
ountdown. At approxi-
mately 20 seconds, Relay
(R21) does not energize.
2.3 Burner motor runs, pre-
a. Flame is not igniting or is not being detected by the flame safeguard. Check that the manual gas valves are open.
purge appears normal,
Check for manifold pressure at Tap (1), Figure 16, during the 10 seconds the LED marked Pilot is on:
LED marked PILOT comes
1. If zero, verify that there is pressure at Tap (2), Figure 16, during the same 10 second period. If so, check
on for 10 seconds, then
that LS1 is being actuated by the collar on the control rod when at the low fire position. Check that the manual
the flame safeguard locks
knob on GV1 is not closed and power is supplied to valve.
out on flame failure.
2. If manifold pressure is normal, check for disconnected or shorted flame rod or ignition lead wire. Watch the
ignition attempt through inspection window on burner and check that spark is in the appropriate location. If not,
this indicates a short. If flame is bserved but not detected by the flame safeguard, remove the burner gun
assembly and check the flame rod, lead wire, and connections.
3. Check the flame safeguard with a flame simulator:
a. Close main gas test cock.
b. Plug the flame simulator into the flame safeguard.
c. When the LED marked PILOT comes on, touch the simulator G post to ground. If the LED marked FLAME now
comes on, the flame safeguard is working, but it is not receiving an adequate flame signal. If the LED marked
FLAME did not come on, replace the R7847A amplifier and/or the RM7895A flame safeguard.
4. If there is spark but no flame, check for faults that would cause way too much air or too little gas.
BURNER MOTOR RUNS, FLAME IGNITES . . .
3.1 Burner motor starts, a
a. The flame is momentarily proving itself to the flame safeguard. It must be proven at the end of the 10 second trial for
normal prepurge cycle
ignition period.
occurs, the LED marked
b. On a new start-up, this could indicate the gas lines have not been sufficiently purged of air.
FLAME comes on
c. Improper flame rod position.
momentarily and then
d. Defective or improperly installed pressure regulator that passes enough gas during the off cycle to build up pressure
goes out.
for light off but when the valve opens quickly drops pressure.
3.2 Burner ignites, the flame
a. The temperature control system has contacts that turn the burner on and separate contacts that control firing rate.
safeguard does not lock
Verify that the contacts that control firing rate are calling for an increase rate.
out but the burner remains
b. Verify that Relay R23 is functioning properly.
at the minimum rate.