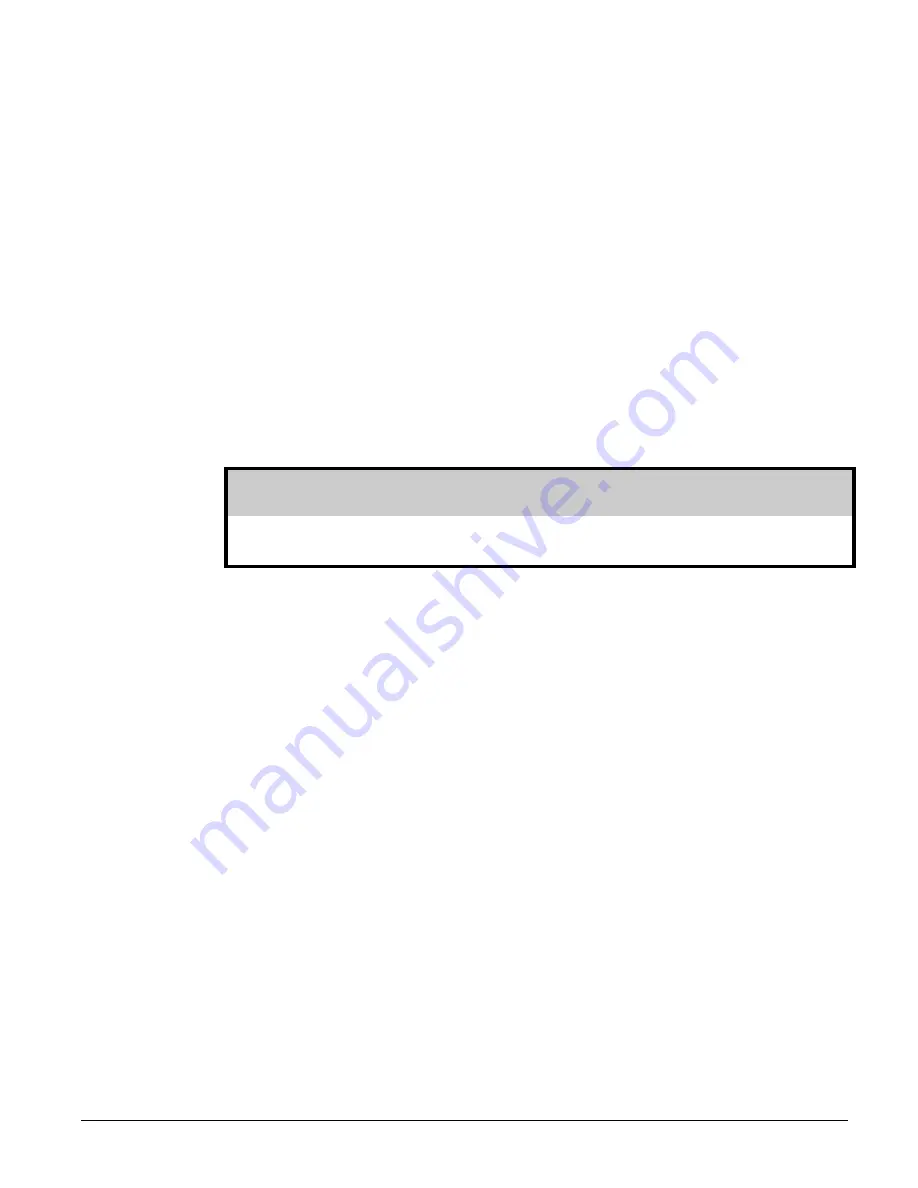
IM 676
7
Water Piping
Local authorities can supply the installer with the proper building and safety codes required for safe
and proper installation.
Install piping with minimum bends and changes in elevation to minimize pressure drop.
Consider the following when installing water piping:
1. Vibration eliminators to reduce vibration and noise transmission to the building.
2. Shutoff valves to isolate the unit from the piping system during unit servicing.
3. Manual or automatic air vent valves at the high points of the system. Install drains at the
lowest points in the system.
4. A means of maintaining adequate system water pressure (expansion tank or regulating valve).
5. Temperature and pressure indicators located at the unit to aid in unit servicing.
6. A strainer or other means of removing foreign matter from the water before it enters the pump.
Place the strainer far enough upstream to prevent cavitation at the pump inlet (consult pump
manufacturer for recommendations). The use of a strainer will prolong pump life and keep
system performance up.
7. Place a strainer in the water line just before the inlet of the evaporator. This will help prevent
foreign material from entering and decreasing the performance of the evaporator.
CAUTION
If separate disconnect is used for the 110V supply to the evaporator heating cable, mark
the disconnect clearly to ensure disconnect is not accidentally shut off during cold seasons.
8. The shell-and-tube evaporator has a thermostat and heating cable to prevent freeze-up down to -
20
°
F (-29
°
C). It is suggested that the heating cable be wired to a separate 110V supply circuit.
As shipped from the factory, the heating cable is wired to the control circuit. All water piping
to the unit must also be protected to prevent freezing.
9. If the unit is used as a replacement chiller on a previously existing piping system, flush the
system thoroughly before unit installation. Regular water analysis and chemical water
treatment on the evaporator is recommended immediately at equipment start-up.
10. The total water volume in the system should be sufficient to prevent frequent “on-off” cycling.
Turnover rate should not be less than 15 minutes for normal variable cooling loads. Turnover
rate for process cooling or a constant load,should not be less than 6 minutes.
11. When glycol is added to the water system for freeze protection, the refrigerant suction pressure
will be lower, cooling performance less, and water side pressure drop greater. If the percentage
of glycol is high, or if propylene is used instead of ethylene glycol, the added pressure drop and
loss of performance could be substantial. Reset the freezestat and low leaving water alarm
temperatures. The freezestat is factory set to default at 36
°
F (2.2
°
C). Reset the freezestat
setting to approximately 4 to 5 degress F (2.3 to 2.8 degress C) below the leaving chilled water
setpoint temperature. See the section titled “Glycol Solutions” for additional information
concerning glycol.
12. Perform a preliminary leak check before insulating the piping and filling the system.
13. Piping insulation should include a vapor barrier to prevent condensation and possible damage
to the building structure.