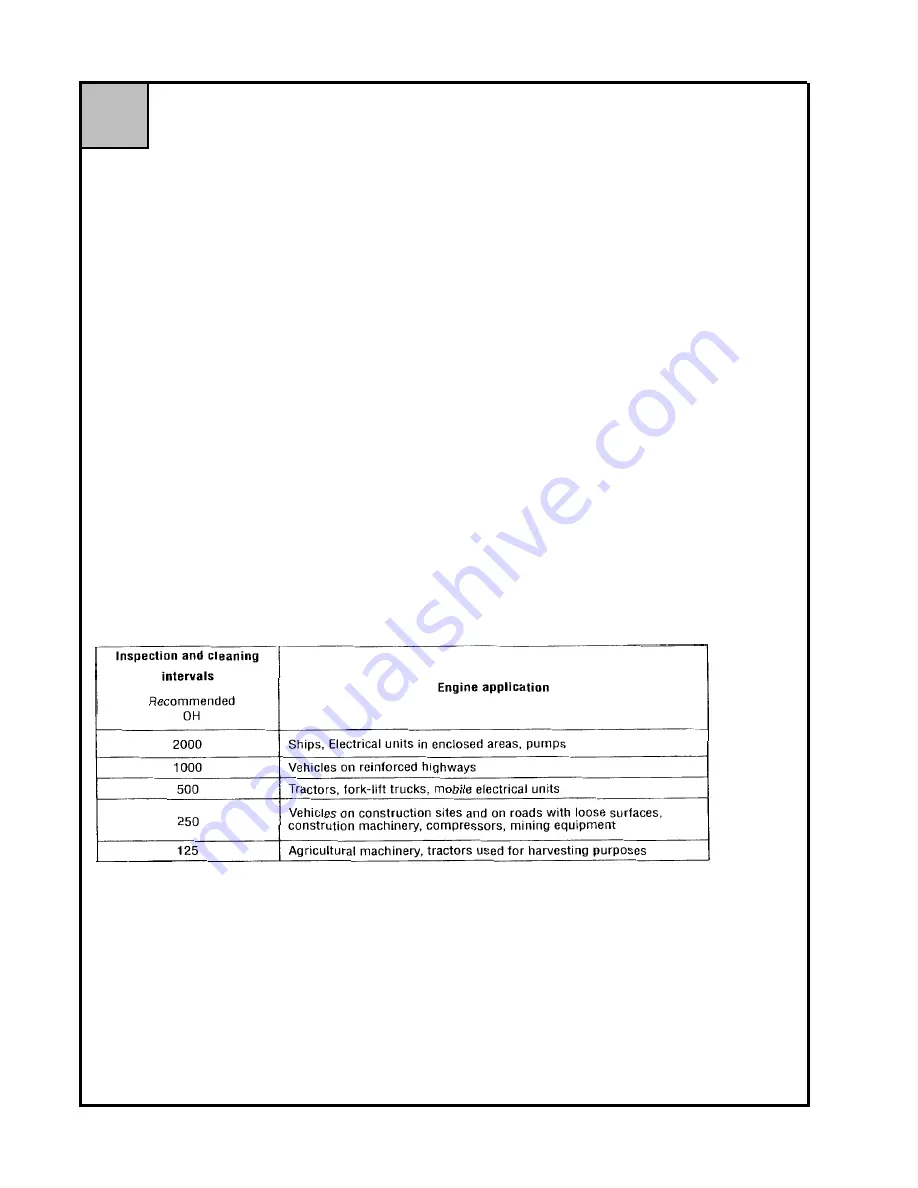
SERVICE AND MAINTENANCE
6.3 Cooling System
6.3.1 Cleaning Intervals
The amount of contamination in the
cooling system depends on the
engine application.
Spilled oil or fuel on the engine
increases the risk of contamination.
Be especially careful if the engine
is used in dusty environments.
Because applications vary, cleaning
intervals have to be determined from
case to case. The cleaning intervals
given in the table on the below can be
used as a guide.
Serious contamination can occur,
for example:
- on construction sites where there is
a high level or air borne dust.
- in harvesting applications where
here are high concentrations of chaff
and chopped straw in the vicinity of
the machine.
5.1.24
Clean the engine as described in 6.8.1.
Summary of Contents for MCL 36C
Page 10: ...CARRIAGE ASSEMBLY McL 36 42C 3 1 1...
Page 12: ...ROLL BAR ASSEMBLY McL 36 42C 3 2 1...
Page 14: ...McL 36 42C POWERTRAIN ASSEMBLY 3 3 1...
Page 16: ...DOG PLATE ASSEMBLY McL 36 42C 3 4 1...
Page 18: ...36 CASING PUSHER SPOIL EJECTOR 3 5 1 McL 36 42C...
Page 20: ...42 CASING PUSHER SPOIL EJECTOR McL 36 42C 3 5 3...
Page 22: ...MASTER TRACK ASSEMBLY McL 36 42C 3 6 1...
Page 29: ......
Page 30: ......
Page 31: ......
Page 32: ...HYDRAULIC SYSTEM McL 36 42C 4 1 1 HOSES AND FITTINGS...
Page 34: ...ELECTRICAL SYSTEM McL 36 42C WIRING DIAGRAM ENGINE DETAIL 4 2 1...
Page 35: ......
Page 53: ...ROUTINEMAINTENANCE 5 1MaintenanceSchedule 5 1 17...
Page 55: ...ROUTINEMAINTENANCE 5 3MaintenanceWorkCompleted 5 1 19...
Page 56: ...ROUTINEMAINTENANCE 5 3MaintenanceWorkCompleted 5 1 20...
Page 69: ...7 1DiagnosisChart FAULTS CAUSES AND REMEDIES 5 1 33...
Page 71: ...9 1EngineSpecificationsandSettings TECHNICAL SPECIFICATIONS 5 1 35...
Page 72: ...9 1EngineSpecificationsandSettings TECHNICAL SPECIFICATIONS 5 1 36...
Page 74: ......
Page 76: ...TRANSMISSION PARTS 5 2 1 McL 36 42C...
Page 78: ...GEARBOXPARTS McL 36 42C 5 3 1...