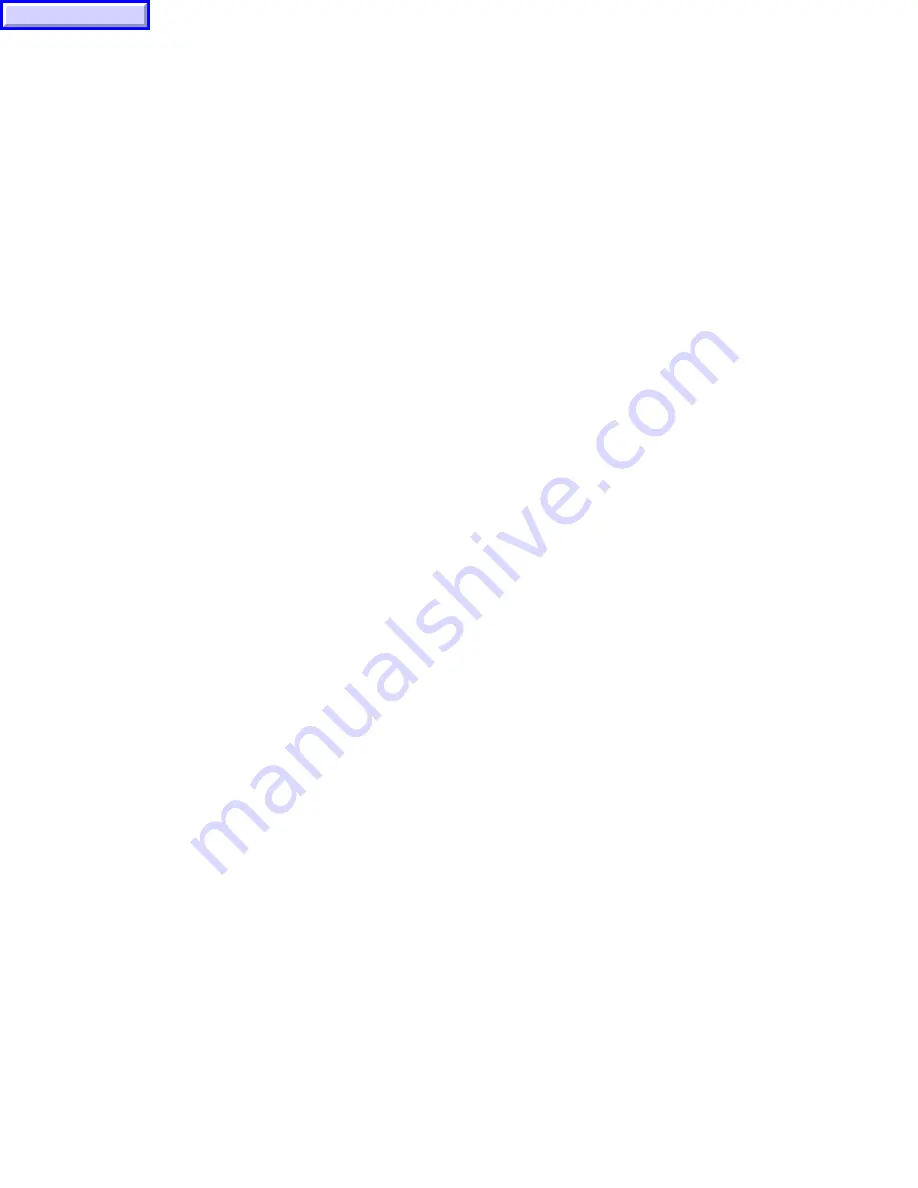
............................................................................................
5-3-2 Construction of the ATC Magazine
............................................................................
........................................................................................
5-4-2 Maintenance of the Hydraulic Unit
.............................................................................
5-4-3 Hydraulic Circuit Diagram
..........................................................................................
......................................................................................
5-5-2 Maintenance of the Air Unit
........................................................................................
5-5-3 Pneumatic Circuit Diagram
........................................................................................
5-6 Centralized Lubrication Unit
........................................................................
5-6-2 Maintenance of the Centralized Lubrication Unit
.......................................................
5-6-3 Spindle, Linear Guide and Ball Screw Lubrication
.....................................................
....................................................................................
5-7-2 Construction of the Spindle Cooling Unit
...................................................................
5-7-3 Spindle Cooling Circuit Diagram
................................................................................
...........................................................................................
5-8-2 Construction of the Coolant System
...........................................................................
5-9-3 Changing the Reed Switch
.........................................................................................
5-10 NC Unit and Electric Control Cabinet
........................................................
5-10-2 Resetting the thermal relay
......................................................................................
5-10-3 Changing the Proximity Sensor
................................................................................
................................................................................
6-1 Precautions on Installing the Machine
........................................................
Return to Library
Summary of Contents for VTC-160A
Page 2: ...Notes Return to Library...
Page 20: ...Notes Return to Library...
Page 54: ...4 20 MEMO Return to Library...
Page 61: ...5 7 5 4 3 Hydraulic Circuit Diagram Return to Library...
Page 74: ...5 20 MEMO Return to Library...
Page 82: ...6 8 Machine body Fig 6 1 Lifting the Machine Return to Library...
Page 96: ...7 4 MEMO Return to Library...