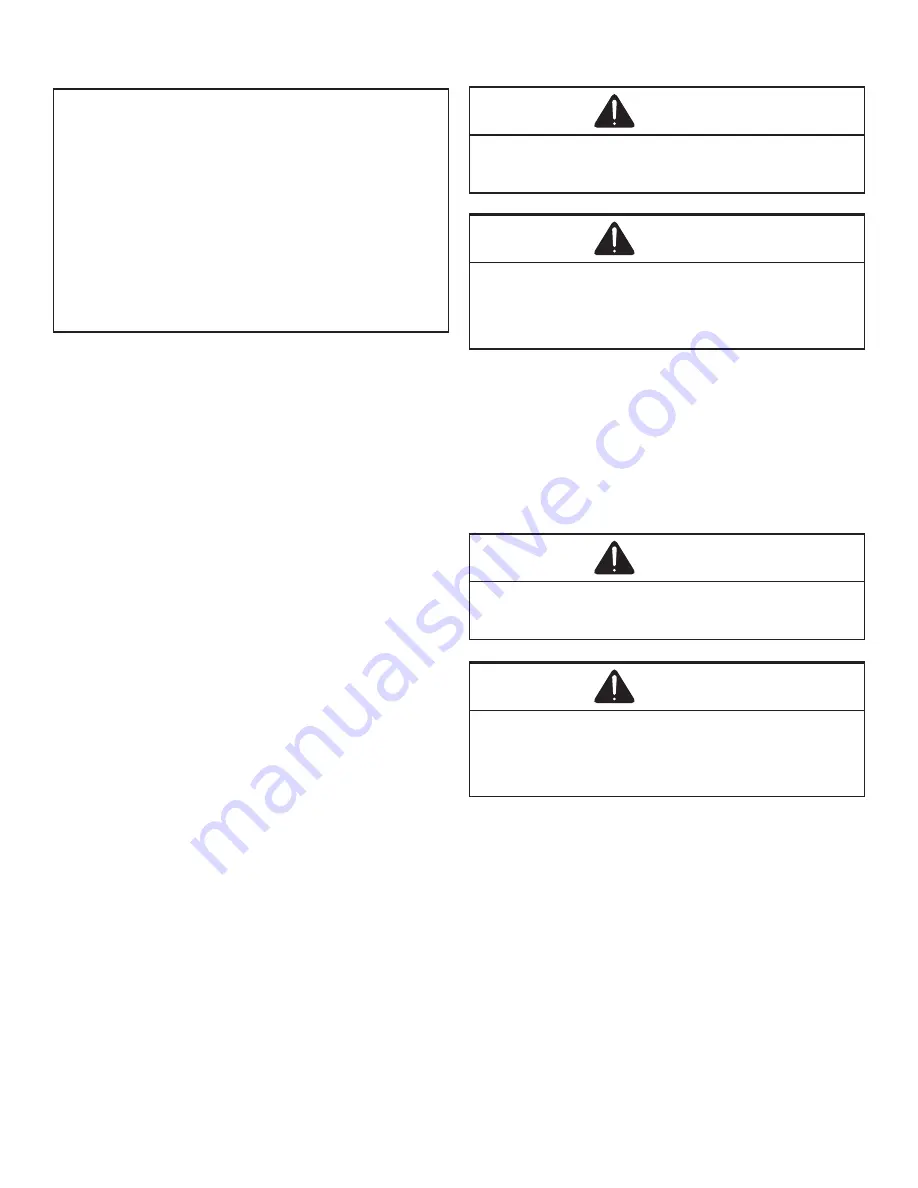
7
REFRIGERANT LINE CONNECTIONS
IMPORTANT
To avoid overheating the service valve, TXV, sensor or filter
drier while brazing, wrap the component with a wet rag,
or use a thermal heat trap compound. Be sure to follow
the manufacturer’s instruction when using the heat trap
compound. NOTE: Remove Schrader valves from service
valves before brazing tubes to the valves. Use a brazing
alloy of 2% minimum silver content. Do not use flux.
Torch heat required to braze tubes of various sizes is
proportional to the size of the tube. Tubes of smaller size
require less heat to bring the tube to brazing temperature
before adding brazing alloy. Applying too much heat to
any tube can melt the tube. Service personnel must use the
appropriate heat level for the size of the tube being brazed.
NOTE: The use of a heat shield when brazing is
recommended to avoid burning the serial plate or
the finish on the unit.
1. The ends of the refrigerant lines must be cut square,
deburred, cleaned, and be round and free from nicks
or dents. Any other condition increases the chance of
a refrigerant leak.
2. Purge with nitrogen at 2 to 3 psig during brazing
to prevent the formation of copper-oxide inside
the refrigerant lines. The FVC oils used in R-410A
applications will clean any copper-oxide present
from the inside of the refrigerant lines and spread it
throughout the system. This may cause a blockage or
failure of the metering device.
3. After brazing, quench the joints with water or a wet
cloth to prevent overheating of the service valve.
4.
A bi-flow filter drier is shipped with the unit as a
separate component and must be brazed on by the
installer on-site. Ensure the bi-flow filter drier paint
finish is intact after brazing. If the paint of the steel
filter drier has been burned or chipped, repaint or treat
with a rust preventative.
The recommended location of the filter drier is before the
expansion device at the indoor unit.
NOTE: Be careful not to kink or dent refrigerant
lines. Kinked or dented lines will cause poor
performance or compressor damage.
Do NOT make final refrigerant line connection until plugs
are removed from refrigerant tubing.
Standing Pressure Test (Recommended before
System Evacuation)
WARNING
To avoid the risk of fire or explosion, never use oxygen,
high pressure air or flammable gases for leak testing of a
refrigeration system.
WARNING
To avoid possible explosion, the line from the nitrogen
cylinder must include a pressure regulator and a pressure
relief valve. The pressure relief valve must be set to open at
no more than 450 psig.
Using dry nitrogen, pressurize the system to 450 PSIG.
Allow the pressure to stabilize and hold for 15 minutes
(minimum). If the pressure does not drop below 450 PSIG
the system is considered leak free. Proceed to system
evacuation using the Deep Vacuum Method. If after 15
minutes the pressure drops below 450 PSIG follow the
procedure outlined below to identify system leaks. Repeat
the Standing Pressure Test.
Leak Testing (Nitrogen or Nitrogen-Traced)
WARNING
To avoid the risk of fire or explosion, never use oxygen,
high pressure air or flammable gases for leak testing of a
refrigeration system.
WARNING
To avoid possible explosion, the line from the nitrogen
cylinder must include a pressure regulator and a pressure
relief valve. The pressure relief valve must be set to open at
no more than 450 psig.
Leak test the system using dry nitrogen and soapy
water to identify leaks. If you prefer to use an electronic
leak detector, charge the system to 10 PSIG with the
appropriate system refrigerant (see Serial Data Plate
for refrigerant identification). Do not use an alternative
refrigerant. Using dry nitrogen finish charging the system
to 450 PSIG. Apply the leak detector to all suspect areas.
When leaks are discovered, repair the leaks, and repeat
the pressure test. If leaks have been eliminated proceed to
system evacuation.
System Evacuation
Condensing unit liquid and suction valves are closed to
contain the charge within the unit. The unit is shipped with
the valve stems closed and caps installed. Do not open
valves until the system is evacuated.
Summary of Contents for Amana VZC20
Page 6: ...6...
Page 48: ...48 4 Select YES to continue 5 Select HEAT PUMP 6 Select SYS SETUP...
Page 55: ...55 NOTE BOOST MODE is applicable only for AVZC200 AB and GVZC20 AA or later revision...
Page 56: ...56 https partnerlinkmarketing goodmanmfg com goodman info finder plus...
Page 57: ...57 THIS PAGE IS INTENTIONALLY LEFT BLANK...
Page 58: ...58 THIS PAGE IS INTENTIONALLY LEFT BLANK...