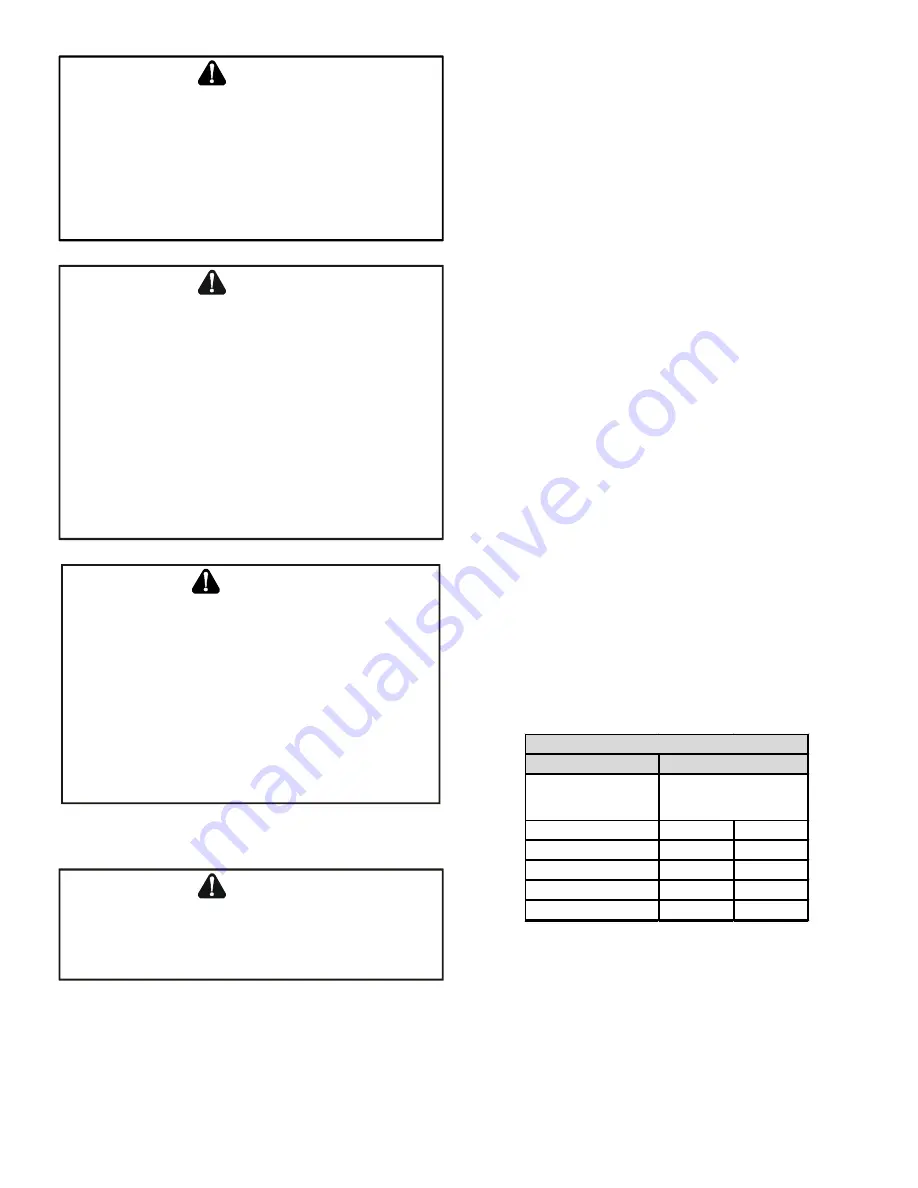
5
T
O
AVOID
POSSIBLE
EXPLOSION
,
USE
ONLY
RETURNABLE
(
NOT
DISPOSABLE
)
SERVICE
CYLINDERS
WHEN
REMOVING
REFRIGERANT
FROM
A
SYSTEM
.
• E
NSURE
THE
CYLINDER
IS
FREE
OF
DAMAGE
WHICH
COULD
LEAD
TO
A
LEAK
OR
EXPLOSION
.
• E
NSURE
THE
HYDROSTATIC
TEST
DATE
DOES
NOT
EXCEED
5
YEARS
.
• E
NSURE
THE
PRESSURE
RATING
MEETS
OR
EXCEEDS
400
PSIG
.
W
HEN
IN
DOUBT
,
DO
NOT
USE
CYLINDER
.
WARNING
R
EFRIGERANTS
ARE
HEAVIER
THAN
AIR
. T
HEY
CAN
“
PUSH
OUT
”
THE
OXYGEN
IN
YOUR
LUNGS
OR
IN
ANY
ENCLOSED
SPACE
. T
O
AVOID
POSSIBLE
DIFFICULTY
IN
BREATHING
OR
DEATH
:
• N
EVER
PURGE
REFRIGERANT
INTO
AN
ENCLOSED
ROOM
OR
SPACE
. B
Y
LAW
,
ALL
REFRIGERANTS
MUST
BE
RECLAIMED
.
• I
F
AN
INDOOR
LEAK
IS
SUSPECTED
,
THOROUGHLY
VENTILATE
THE
AREA
BEFORE
BEGINNING
WORK
.
• L
IQUID
REFRIGERANT
CAN
BE
VERY
COLD
. T
O
AVOID
POSSIBLE
FROSTBITE
OR
BLINDNESS
,
AVOID
CONTACT
AND
WEAR
GLOVES
AND
GOGGLES
. I
F
LIQUID
REFRIGERANT
DOES
CONTACT
YOUR
SKIN
OR
EYES
,
SEEK
MEDICAL
HELP
IMMEDIATELY
.
• A
LWAYS
FOLLOW
EPA
REGULATIONS
. N
EVER
BURN
REFRIGERANT
,
AS
P
OISONOUS
GAS
WILL
BE
PRODUCED
.
WARNING
T
O
AVOID
POSSIBLE
EXPLOSION
:
•N
EVER
APPLY
FLAME
OR
STEAM
TO
A
REFRIGERANT
CYLINDER
. I
F
YOU
MUST
HEAT
A
CYLINDER
FOR
FASTER
CHARGING
,
PARTIALLY
IMMERSE
IT
IN
WARM
WATER
.
•N
EVER
FILL
A
CYLINDER
MORE
THAN
80%
FULL
OF
LIQUID
REFRIGERANT
.
•N
EVER
ADD
ANYTHING
OTHER
THAN
R-410A
TO
A
RETURNABLE
R-410A
CYLINDER
. T
HE
SERVICE
EQUIPMENT
USED
MUST
BE
LISTED
OR
CERTIFIED
FOR
THE
TYPE
OF
REFRIGERANT
USE
.
•S
TORE
CYLINDERS
IN
A
COOL
,
DRY
PLACE
. N
EVER
USE
A
CYLINDER
AS
A
PLATFORM
OR
A
ROLLER
.
WARNING
REFRIGERANT LINES
T
HE
COMPRESSOR
PVE
OIL
FOR
R-410A
UNITS
IS
EXTREMELY
SUSCEPTIBLE
TO
MOISTURE
ABSORPTION
AND
COULD
CAUSE
COMPRESSOR
FAILURE
. D
O
NOT
LEAVE
SYSTEM
OPEN
TO
ATMOSPHERE
ANY
LONGER
THAN
NECESSARY
FOR
INSTALLATION
.
CAUTION
Use only refrigerant grade (dehydrated and sealed) copper
tubing to connect the heat pump unit with the indoor unit.
After cutting the tubing, install plugs to keep refrigerant
tubing clean and dry prior to and during installation. Tubing
should always be cut square keeping ends round and free
from burrs. Clean the tubing to prevent contamination.
The liquid line must be insulated if more than 50 ft. of liquid
line will pass through an area that may reach temperatures
of 30 °F or higher than ambient in cooling mode and/or if
the temperature inside the conditioned space may reach a
temperature lower than ambient in heating mode. Never
attach a liquid line to any uninsulated potion of the suction
line.
Do NOT let refrigerant lines come in direct contact with
plumbing, ductwork, floor joists, wall studs, floors, and
walls. When running refrigerant lines through a foundation
or wall, openings should allow for sound and vibration
absorbing material to be placed or installed between tubing
and foundation. Any gap between foundation or wall and
refrigerant lines should be filled with a pliable silicon-
based caulk, RTV or a vibration damping material. Avoid
suspending refrigerant tubing from joists and studs with
rigid wire or straps that would come in contact with the
tubing. Use an insulated or suspension type hanger. Keep
both lines separate and always insulate the suction line.
Insulation is necessary to prevent condensation from
forming and dropping from the suction line. Armflex or
satisfactory equivalent with 3/8” min. wall thickness is
recommended. In severe conditions (hot, high humidity
areas) 1/2” insulation may be required. Insulation must
be installed in a manner which protects tubing and
connections from damage and contamination.
Where possible, drain as much residual compressor oil
from existing systems, lines, and traps; pay close attention
to low areas where oil may collect. NOTE: If changing
refrigerant, the indoor coil and metering device must be
replaced. Only AVPEC air handlers or TXV-V** expansion
valves are compatible and have been manufacturer
approved for use with these models. See unit specifications
or AHRI for an approved system match.
Line Set Length
Heat Pump Unit
(Tons)
Suct
Liq
2
3/4
3/8
3
7/8
3/8
4
1 1/8
3/8
5
1 1/8
3/8
0-250' Equivalent
INTERCONNECTING TUBING
Line Type & Line
Diameter (In. OD)
Burying Refrigerant Lines
If burying refrigerant lines can not be avoided, use the
following checklist:
1. Insulate liquid and suction lines separately.
2. Enclose all underground portions of the refrigerant
lines in waterproof material (conduit or pipe) sealing
the ends where tubing enters/exits the enclosure.
3. If the lines must pass under or through a concrete
slab, ensure lines are adequately protected and
sealed.
Summary of Contents for Amana VZC20
Page 6: ...6...
Page 48: ...48 4 Select YES to continue 5 Select HEAT PUMP 6 Select SYS SETUP...
Page 55: ...55 NOTE BOOST MODE is applicable only for AVZC200 AB and GVZC20 AA or later revision...
Page 56: ...56 https partnerlinkmarketing goodmanmfg com goodman info finder plus...
Page 57: ...57 THIS PAGE IS INTENTIONALLY LEFT BLANK...
Page 58: ...58 THIS PAGE IS INTENTIONALLY LEFT BLANK...