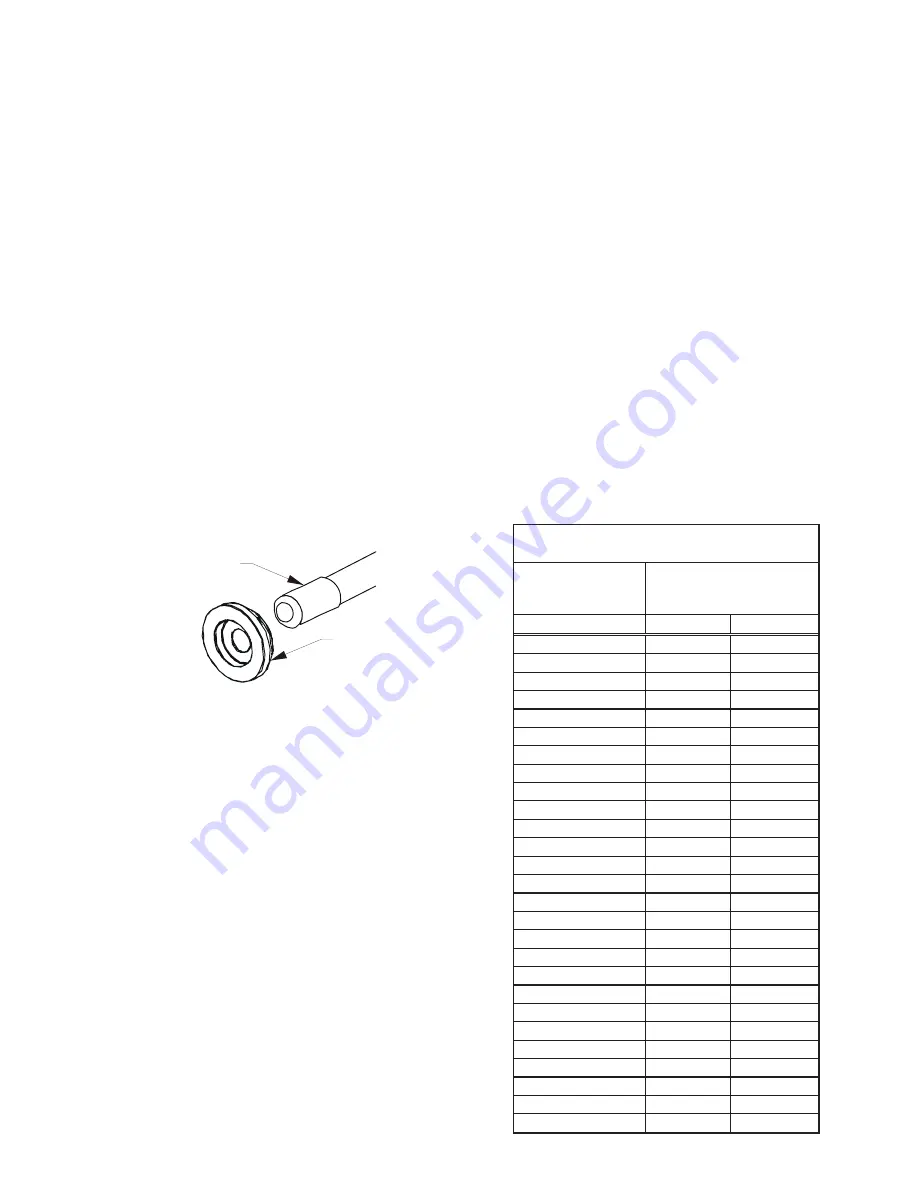
7
7.3 Tubing Connections for TXV Models
TXV models come with factory installed TXV with the bulb
pre-installed on the vapor tube.
1. Remove refrigerant tubing panel or coil (lower) access pan
-
el.
2. Remove access valve fitting cap and depress the valve stem
in access fitting to release pressure. No pressure indicates
possible leak.
3. Replace the refrigerant tubing panel.
4. Remove the spin closure on both the liquid and suction
tubes using a tubing cutter.
5. Insert liquid line set into liquid tube expansion and slide
grommet about 18” away from braze joint.
6. Insert suction line set into suction tube expansion and slide
insulation and grommet about 18” away from braze joint.
7. Braze joints. Quench all brazed joints with water or a wet
rag upon completion of brazing.
NOTE
: The sensing bulb must be permanently located. A heat
shield, heat trap, or wet rag must be used during brazing to prevent
damage to the TXV valve.
8. Replace access panels, suction line grommet, insulation and
all screws.
RUBBER
GROMMET
SUCTION LINE
WITH SPIN CLOSURE
Suction Line Grommet
Figure 10
7.4 Thermal Expansion Valve System Adjustment
Run the system at Cooling for 10 minutes until refrigerant
pressures stabilize. Use the following guidelines and meth
-
ods to check unit operation and ensure that the refrigerant
charge is within limits. Charge the unit on low stage.
1. Purge gauge lines. Connect service gauge manifold to base-
valve service ports.
2. Temporarily install a thermometer on the liquid line at the
liquid line service valve and 4-6’’ from the compressor on
the suction line. Ensure the thermometer makes adequate
contact and is insulated for best possible readings. Use
liquid line temperatice to determine subcooling and vapor
temperature to determine superheat.
3. Check subcooling and superheat. Systems with TXV applica
-
tion should have a subcooling of 7 to 9°F and superheat of
7 to 9°F
a. If subcooling and superheat are low, adjust TXV to 7 to
9°F, and then check subcooling.
NOTE
: To adjust superheat, turn the valve stem clockwise to in
-
crease and counter clockwise to decrease.
b. If subcooling is low and superheat is high,
add
charge to
raise subcooling to 7 to 9°F, and then check superheat.
c. If subcooling and superheat are high,
adjust
TXV valve to
7 to 9° superheat, then check subcooling.
d. If subcooling is high and superheat is low,
adjust
TXV valve
to 7 to 9° superheat and
remove
charge to lower the sub
-
cooling to 7 to 9°F.
NOTE
: Do NOT adjust the charge based on suction pressure unless
there is a gross undercharge.
4. Disconnect manifold set, and installation is complete.
NOTE
: Check the Schrader ports for leaks and tighten valve cores
if necessary. Install caps finger-tight.
SUBCOOL FORMULA=
SAT. LIQUID LINE TEMP - LIQUID LINE TEMP
SUPERHEAT FORMULA=
SUCT. LINE TEMP - SAT. SUCT. TEMP
SUCTION PRESSURE
PSIG
R-22
R-410A
50
26
1
52
28
3
54
29
4
56
31
6
58
32
7
60
34
8
62
35
10
64
37
11
66
38
13
68
40
14
70
41
15
72
42
16
74
44
17
76
45
19
78
46
20
80
48
21
85
50
24
90
53
26
95
56
29
100
59
31
110
64
36
120
69
41
130
73
45
140
78
49
150
83
53
160
86
56
170
90
60
SATURATED SUCTION PRESSURE
TEMPERATURE CHART
SATURATED SUCTION
TEMPERATURE ºF