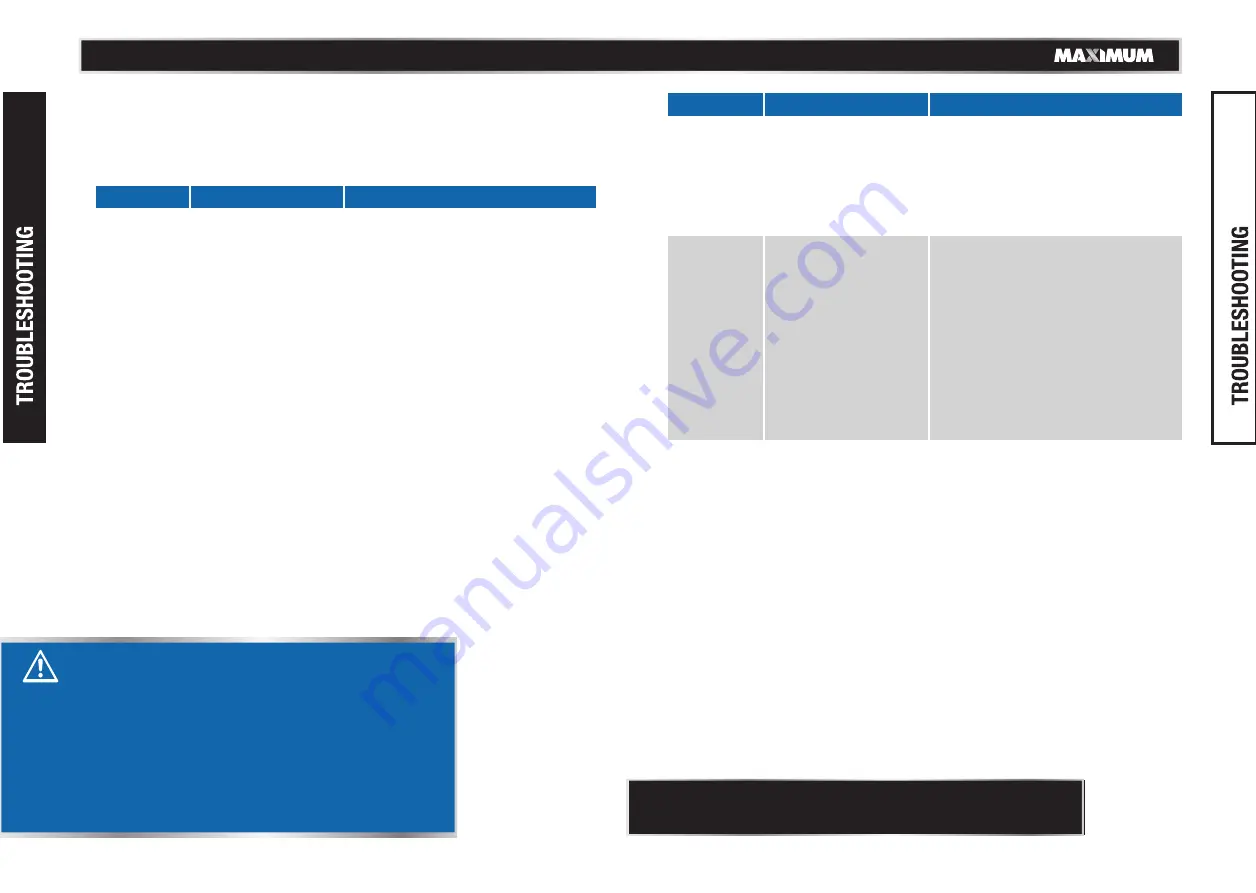
19
18
model no. 058-9365-2 | contact us 1-888-670-6682
Troubleshooting
The following chart lists common issues and solutions. Please read it
carefully and follow all instructions closely.
Tool runs at
normal speed
but loses
power under
load.
Motor parts are worn
or damaged.
Cam clutch is worn or
stuck due to lack of
lubricant.
PROBLEM
POSSIBLE CAUSES
SOLUTIONS
Grease lubrication: Heat is
generated due to
insufficient grease in the chamber.
Severe operating conditions may
require frequent lubrication.
If the problem persists,
please contact
1-888-670-6682.
NOTE:
For further repair information, please
call1-888-670-6682.
PROBLEM
POSSIBLE CAUSES
SOLUTIONS
Tool runs at
low speed.
Air flows
slightly from
exhaust.
Motor parts are
jammed with dirt.
Power regulator is in
closed position.
Air flow is blocked
by dirt.
1. Check if there is blockage in air inlet
and filter.
2. Pour pneumatic tool oil into air inlet
as per instructions.
3. Operate the tool by reversing rotation
back and forth in a short duration.
Repeat the above steps as needed.
Tool stops
working.
Air flows
freely from
exhaust.
One or more motor
vanes are stuck
due to material build up.
Pour pneumatic tool oil into the air
inlet.
2. Tap motor housing gently with
plastic mallet.
3. Operate the tool by reversing the
rotation back and forth in short
duration (wherever applicable).
4. Disconnect the power supply.
Operate the motor manually by
rotating the drive shank (wherever
applicable).
If the problem persists,
please contact 1-888-670-6682.
Tool does
not shutoff.
Throttle valve O-rings
(13, 17, 18, 19) are
dislodged from seat
inlet valve.
If the problem persists, please
contact 1-888-670-6682.
WARNING!
Potential hazard that could result in serious injury or
loss of life.
• If any of the following symptoms appear while the
tool is in use, turn it off and disconnect it from the
air supply immediately. Failure to heed this warning
could result in serious injury or loss of life.
• Disconnect the tool and the electrical plug from the
air supply before making any adjustments.
• Repairs must be performed by a qualified service
technician only.
Replace O-rings.
1.
2.
Lubricate clutch housing.
Check for excess clutch oil.
Clutch cases should only be half
filled, as overfilling can cause
drag on high-speed clutch parts.
A typical oiled/lubricated
wrench requires 1/2 oz (14 ml)
of oil.
1.
2.
1.
1.
2.
TM