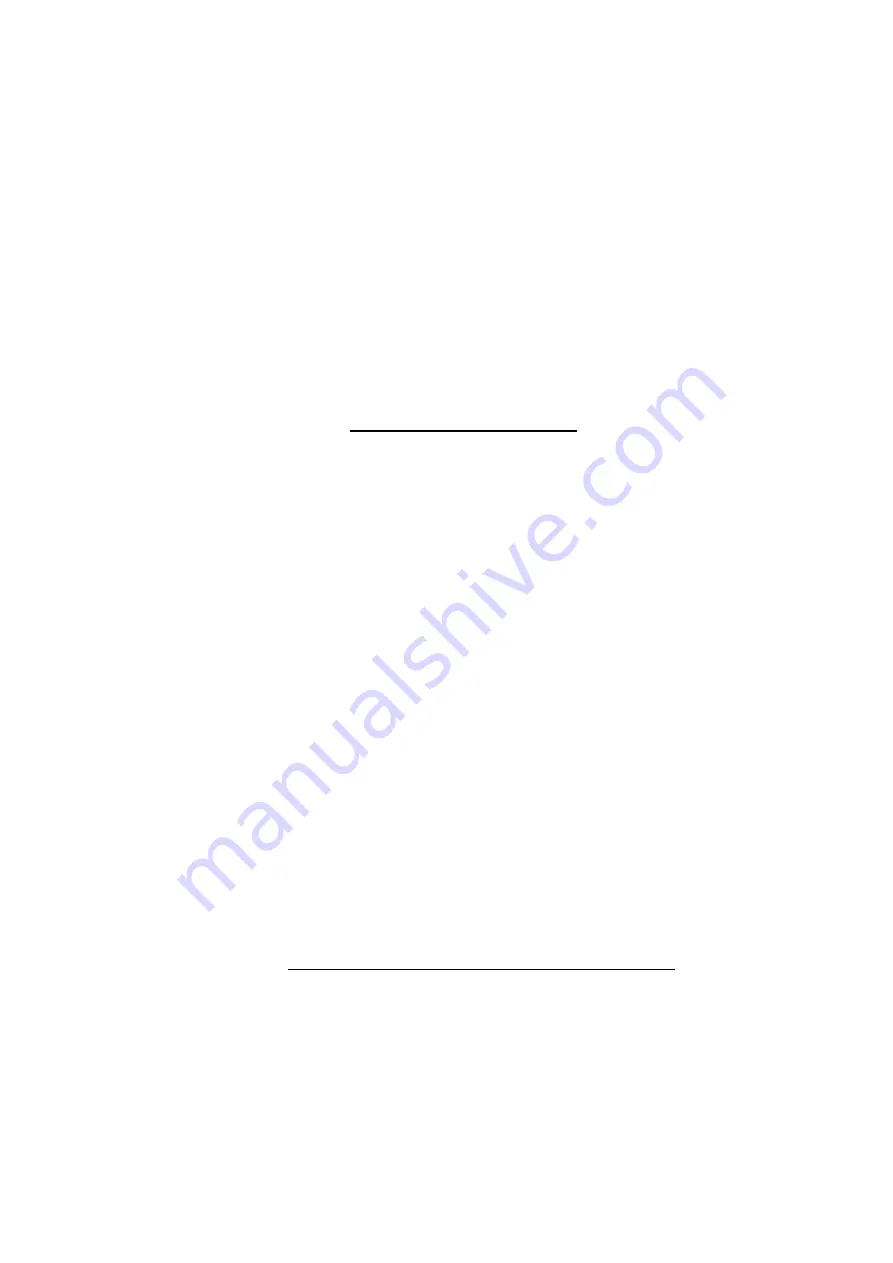
Page of 45
1812367-12
2
MATCO TOOLS
EFFECTIVE APRIL 1, 2015
LIMITED WARRANTY
This warranty applies to the original purchaser and is subject to the terms and conditions listed below. This Limited Warranty is for
new equipment sold after the above date, providing coverage for defects in material and workmanship at the time it is shipped from
the factory.
Limited to the warranty periods below, MATCO TOOLS will repair or replace the item under warranty that fails due to defects in
material and workmanship. MATCO TOOLS must be notified within 30 days of the failure, so as to provide instructions on how to
proceed with the repair of your welder and warranty claim processing. Warranty period begins at the time the welder is purchased
from an Authorized MATCO TOOLS distributor.
Keep your receipt as proof of purchase.
Warranty Periods
Limited Warranty is divided into these categories. No Warranty, 1 year, 2 year and 3 year.
No Warranty
Normal wear items, MIG gun parts (contact tips, nozzle, contact tip adapter, MIG gun liner), drive roll, electrode holder, ground
clamps, and plasma torch parts (nozzle, electrode, diffuser, cover) are considered consumable items and are not covered under
warranty.
1 Year Accessories Warranty
Parts and Labor on MIG gun parts (except those listed under normal wear items), cables, regulator, and plasma torch (except those
listed under normal wear items) are covered for 1 year. Any shipping related to warranty repair is the responsibility of the
customer.
3 Year Welder Warranty
The 3 year warranty covers Parts and Labor on items such as: transformer, reactor, rectifier, solenoid valve, PC board, switches,
controls, gas valve, drive motor, drive system other than drive roll and any other component that requires the removal of the sheet
metal to access. Any shipping related to warranty repair is the responsibility of the customer.
Voiding Warranty
Warranty does not apply to: shipping damage, misuse and abuse of the unit and alteration of the unit in any way.
Warranty Claim
This is a Parts and Labor warranty.
Contact the MATCO TOOLS distributor you purchased the unit from
. Retain your receipt in
the case a warranty claim is needed. No warranty will be provided without the original receipt from an authorized MATCO TOOLS
distributor. To make a warranty claim, contact your MATCO TOOLS distributor. That MATCO TOOLS distributor will contact the
customer service department for warranty instructions.