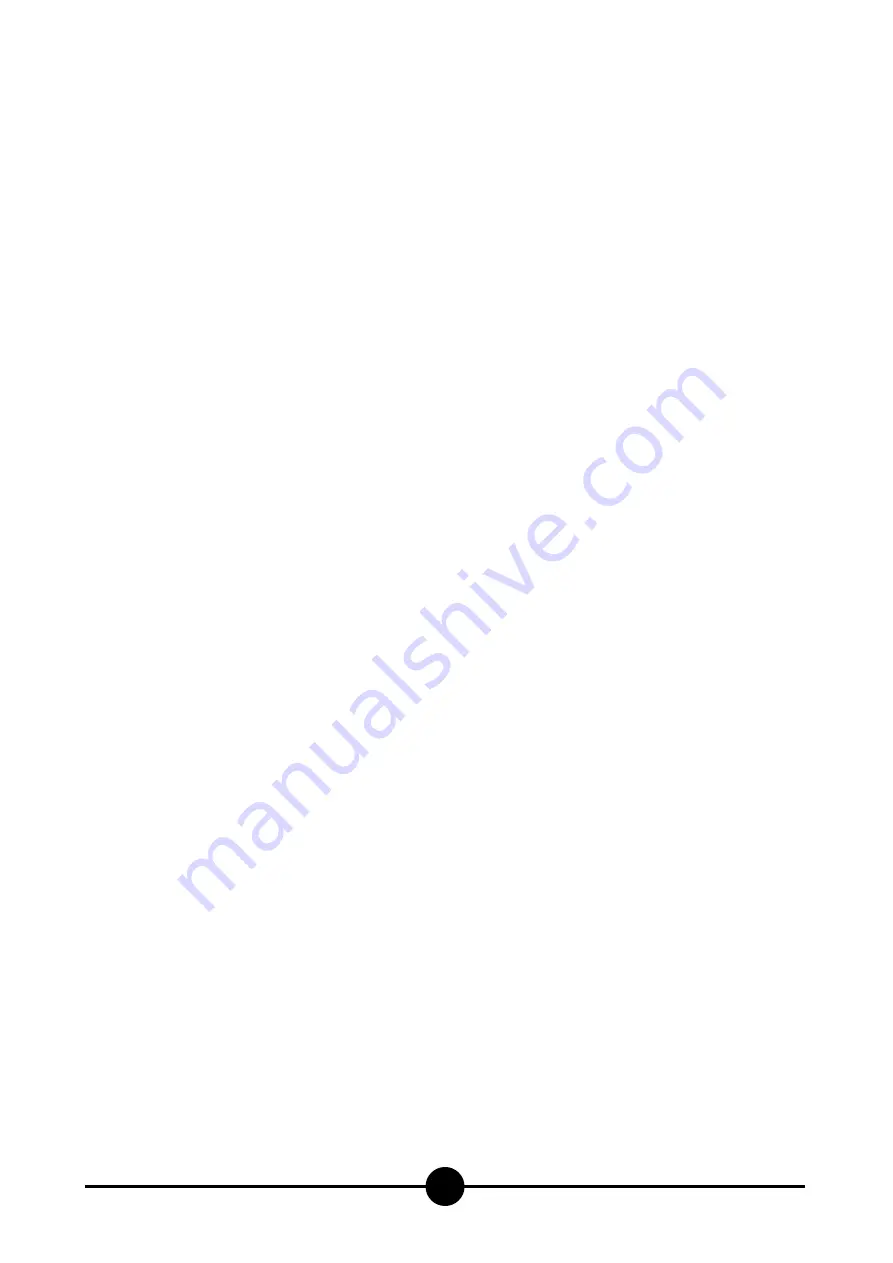
control panel fixing screws.
Remove the control panel, disconnect the ignition lead and
unscrew the nozzle from the nozzle holder with a spanner.
Replace with a new nozzle (see “TECHNICAL DATA” table);
if necessary, to facilitate this operation push the air adjust-
ment sleeve upwards loosening screw (G).
After fitting the nozzle, reset primary air distance “A” (see
“TECHNICAL DATA” table).
Adjusting the low flame (Fig. 2)
Referring to the “TECHNICAL DATA” table, set the low fla-
me screw (D) as follows:
- if the appliance is to run on LP gas, tighten the low flame
screw as far as it will go;
- if the appliance is to run on natural gas, turn the low fla-
me screw while simultaneously adjusting the primary air:
●
read off the setting in It/min which corresponds to the
heat value (calculated by the “Volumetric Method”) in
the Gas Flow Setting Table (2);
●
start the appliance up according to the instructions;
●
after allowing the appliance to run for 45 minutes, turn
the knob to low and set minimum by turning screw (20)
(to the right = gas flow decreases; to the left = gas flow
increases).
Adjust the gas flow.
MAINTENANCE
The following maintenance programme should be carried
out at least once a year:
- Check that all the safety and setting devices are working
properly;
- Check that the burners are working properly with regard
to:
●
ignition
●
combustion safety;
- Check the functions of the appliance as described in pa-
ragraph "Checking the functions".
If the main burner needs cleaning, proceed as follows:
a)
remove the pan support, the flame distributor, the
crown and the burner supports;
b)
clean the parts with water and detergent, rinse and dry;
c)
when reassembling the parts, make sure you replace
them in the right order.
REPLACING PARTS
All parts must be replaced by authorised technicians
only!
To replace the following parts first remove all the control
knobs and the control panel (after loosening the fixing
screws), then disconnect the ignition lead.
Ignition plug (Fig. 2)
Remove the pan support, the flame distributor, the crown
and the the burner crown support, pull out the spring using
a pointed tool, remove the ignition plug from the bottom, di-
sconnect the ignition lead and insert a new plug.
Gas tap (Fig. 2)
Loosen the gas piping and thermocouple fixing screws,
then loosen the screws fixing the gas supply to the gas
ramp and insert a new tap.
Thermocouple (Fig. 2)
Loosen the screws fixing the thermocouple to the gas tap
and the burner. Insert the new part. After replacing the
parts, fit the control panel back into place.
WARNING
Every time a replacement involving gas input parts is
made, recheck all functions and test for leakage.
Resistances electric oven 60
Disconnect the power supply!
Open the oven door; remove the protective shield covering
the back wall of the oven by loosening its fixing screws; the
resistance is held by 5 screws, two of which are on the flan-
ge. Once these screws have been loosened, you can pull
the resistance forward. Disconnect the leads and fit a new
resistance.
Resistances electric oven 90
Disconnect the appliance from the mains. The bottom resi-
stance is under the oven floor.
The top resistance is fixed to the roof of the cooking cham-
ber.
To remove the resistances, loosen the screws fixing them
to the relative flange, pull the resistances and relative leads
forwards.
Disconnect the leads using a screwdriver and fit a new re-
sistance following the above sequence in reverse order.
008-03 - Gas cooker
9