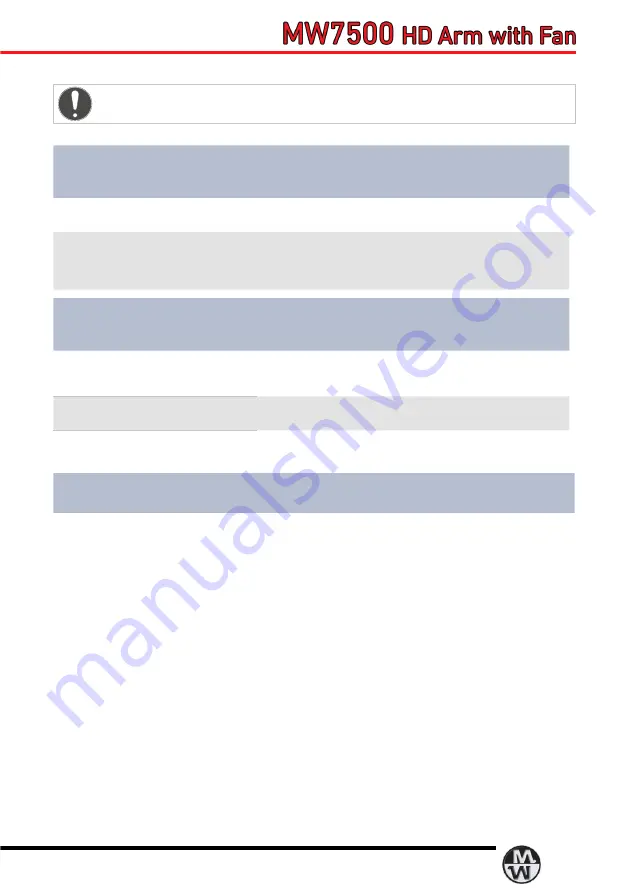
52
IT IS FORBIDDEN TO EVEN PARTIALLY REPRODUCE THE TEXT AND/OR ILLUSTRATIONS.
www.masterweld.co.uk
9.6. TABLE OF SCHEDULED MAINTENANCE
It is recommended to use a register to track the maintenance actions performed.
It is suggested to photocopy this page and keep the register updated.
250 HOURS
Operation
Date
∆p
prev.
∆p
after
Operator's signature
Check correct calibration of the filtering
arm.
Check the status of cleanliness and, if
necessary, clean the filter inlet piping,
including caps, pipes and any flexible
hoses.
500 HOURS
Operation
Date
∆p
prev.
∆p
after
Operator's signature
Check wear of suction hood joints and
hood clutches
Check wear of slewing bearing
Check conditions of internal adjustment
shutter
YEARLY
Operation
Date
Operator's signature
Replace
mandatory
the
flexible
channel sections with flexible hoses
providing the same physical features