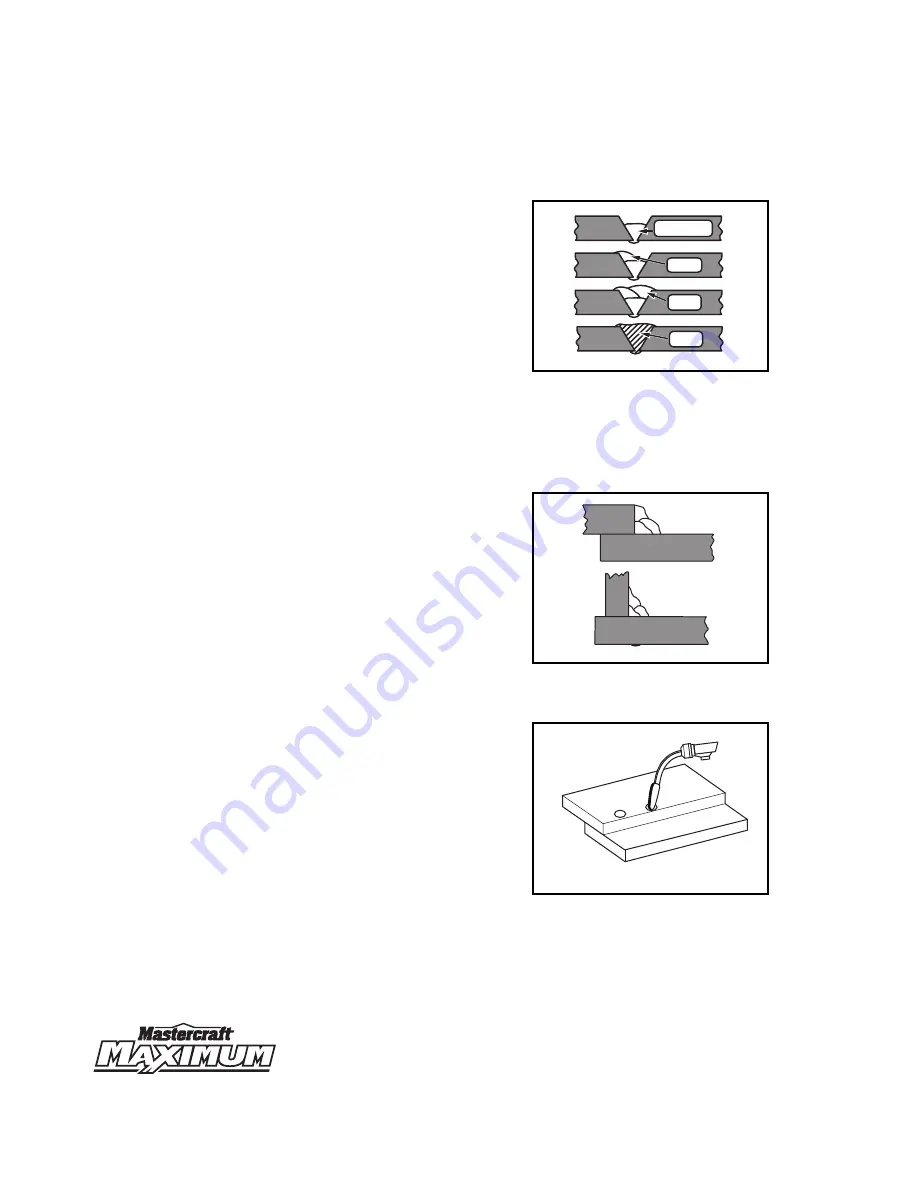
OPERA
TING INSTR
UCTIONS
41
MIG 140 INVERTER WELDER 058-9305-6
Multiple pass welding
1. Butt weld joint: When butt welding
thicker materials, prepare the edges of
the material to be joined by grinding a
bevel on the edges of the metal pieces
being joined. When this process is done,
a "V" is created between the two metal
pieces. In most cases, more than one
pass or bead will need to be laid into the
joint to close the "V"
(fig t)
.
Note: When using self
-shielding
flux core wire,
it is necessary to thoroughly chip and brush the
slag off each completed weld bead before
making another pass.
2. Fillet weld joint: Most fillet weld joints on
metals of moderate to heavy thickness
will require multiple pass welds to
produce strong joint. The multiple pass
beads can be laid in three passes into a
T fillet joint and a lap fillet joint as
shown
(fig u)
.
Spot welding
There are three methods of spot welding:
1. Burn
-
through method: In this method, two
overlapped metal pieces are welded
together by burning through the top piece
and into the bottom piece. It is better to
choose large diameter wire for this
method. Self
-
shielding, flux core wire of
0.035" is suitable for this method. Always
select the high heat setting for this method
and tune in the wire speed prior to making
a spot weld
(fig v)
.
Note: Do not use 0.030" self
-
shielding flux
core wires when using this method unless the
metal is very thin or excessive filler metal and
minimal penetration is acceptable.
fig t
1
2
1
1
2
3
First or
Root Pass
Second
Pass
Third
Pass
Finished
Weld
MC-589305-49
fig u
1
1 2
3
2
3
Lap Joint Welded
In Three Passes
T Joint in
Three Passes
MC-589305-50
fig v
MC-589305-51