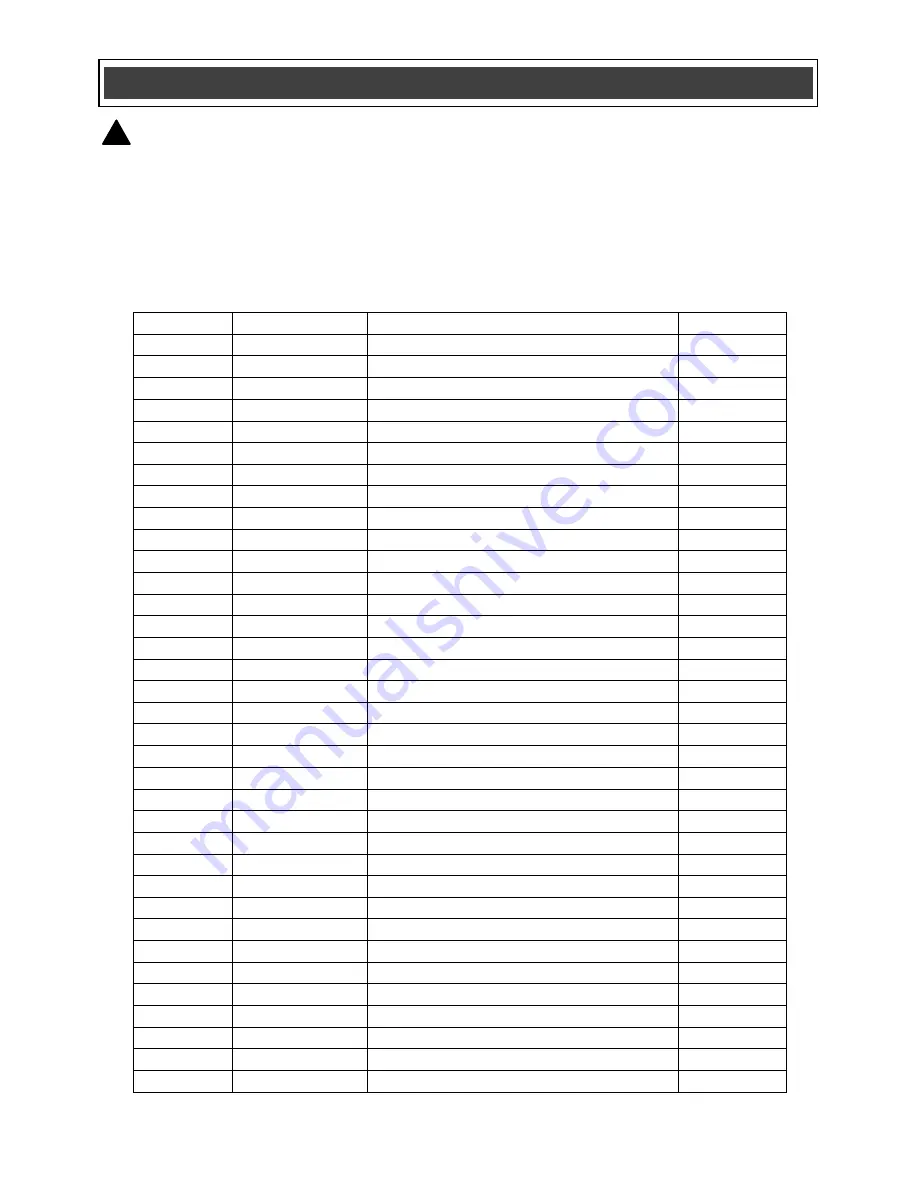
38
WARNING:
When servicing, use only Mastercraft® replacement parts. The use of
any other parts may create a safety hazard or cause damage to the rotary tool.
Any attempt to repair or replace electrical parts on this rotary tool may create a safety
hazard unless repairs are performed by a qualified technician. For more information, call
the Toll-Free Helpline, at 1-800-689-9928.
Always order by PART NUMBER, not by key number.
Key #
Part #
Part Name
Quantity
1
313300
Accessory collar
1
2
215100
Collet nut
1
3
216506
1/8" collet
1
4
213016
Output shaft
1
5
520008
Bearing 626RS
2
6
314009
Fan
1
7
134008
Armature
1
8
138008
Stator
1
9
321006
Bearing sleeve
1
10
500843
Screw M3 x 10
2
11
504000
Spring washer 3
2
12
503008
Small washer 3
2
13
215014
Locking pin
1
14
221286
Washer
1
15
240824
Locking pin spring
1
16
312934
Spindle lock button
1
17
300076
Housing (right)
1
18
234033
Aluminium cover (right)
1
19
500001
Tapping screw ST2.9 x 16
6
20
162853
Rectifying PCB
1
21
500409
Tapping screw ST2.2 x 16
3
22
162852
V.S. PCB
1
23
242553
Hanging loop
1
24
312098
Back cover
1
25
317013
"-" speed control button
1
26
317012
"+" speed control button
1
27
500006
Tapping screw ST2.9 x 12
2
28
224455
Cord clamp
1
29
322006
Cord guard
1
30
160205
Cord set
1
31
314527
Brush holder support
2
32
222827
Brush holder
2
33
342027
Carbon brush
2
34
300076
Housing (left)
1
35
234033
Aluminium cover (left)
1
!
PARTS LIST
Summary of Contents for 54-4790-6
Page 13: ...13 CONTENTS 0 A D B C E F G H I J K L M...
Page 37: ...37 EXPLODED VIEW...