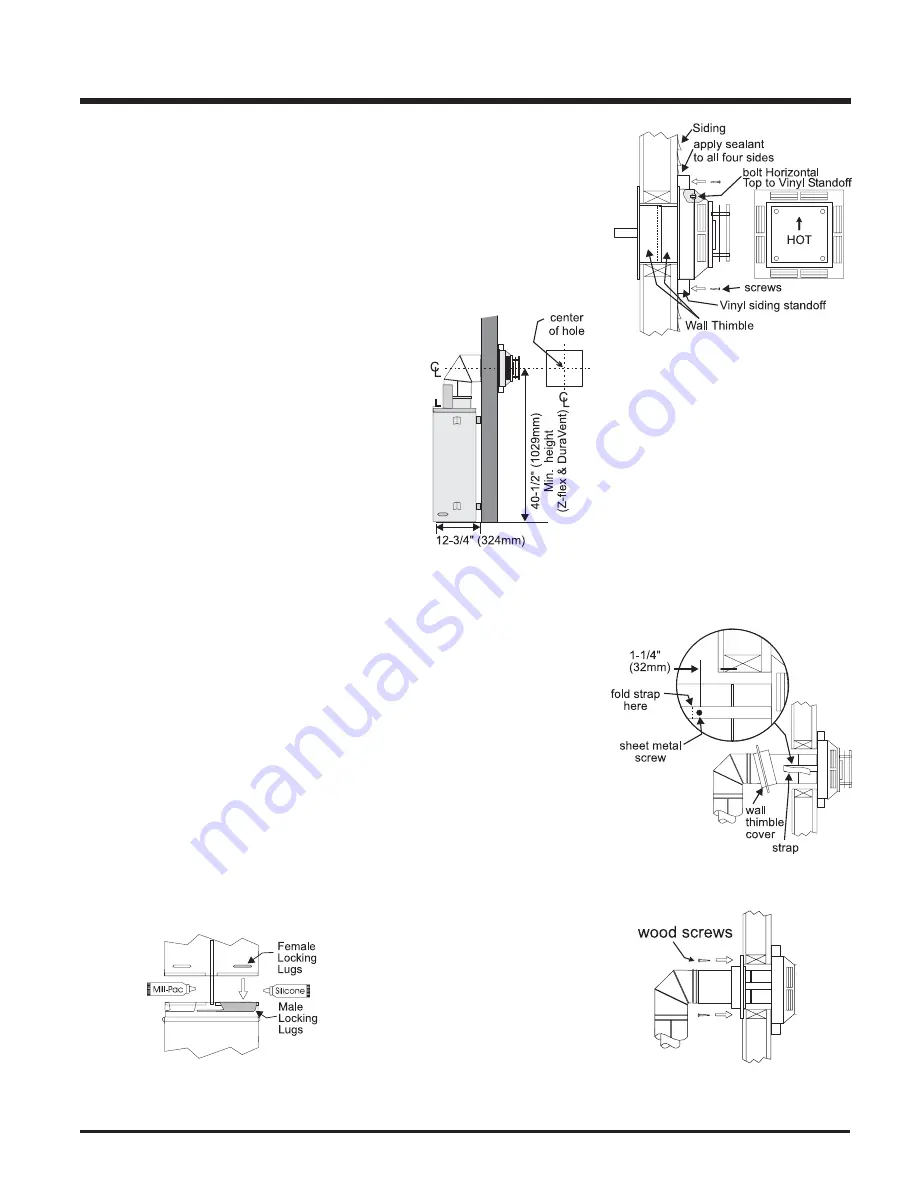
Masport PG36-3 Gas Inbuilt
17
INSTALLATION
Diagram 5
8) Slide the appliance and flue assembly to-
wards the wall carefully inserting the flue
pipe into the flue cap assembly. It is impor-
tant that the flue pipe extends into the flue
cap sufficient distance so as to result in a
minimum pipe overlap of 1-1/4 inches
(32mm). Secure the connection between
the flue pipe and the flue cap by attaching
the two sheet metal strips extending from
the flue cap assembly into the outer wall of
the flue pipe. Use the two sheet metal
screws provided to connect the strips to
the pipe section. See Diagram 4.
9) Install wall thimble in the center of the 10"
square and attach with wood screws (Di-
agram 5).
HORIZONTAL
INSTALLATIONS
Install the flue system according to the
manufacturer's instructions included
with the components.
1) Set the unit in its desired location. Check to
determine if wall studs or roof rafters are in
the way when the flueing system is at-
tached. If this is the case, you may want to
adjust the location of the unit. Rough in the
gas preferably on the right side of the unit
and the electrical (junction block is on the left
side) on the left.
2) Co Axial Flue pipe and fittings are designed
with special twist-lock connections to con-
nect the flueing system to the appliance flue
outlet. A twist-lock appliance adaptor is an
available option that must be used in con-
junction with the Simpson Dura-Vent Co
Axial Flue GS system.
3) Put a bead of silicone inside the outer section
of the adapter and a bead of Stove Mate on
the inner collar. Slip the adapter over the
existing inner and outer flue collar and
fasten to the outer collar only with the 3
supplied screws (drilling pilot holes will
make this easier). Level the fireplace and
fasten it to the framing using nails or screws
through the nailing strips.
4) Assemble the desired combination of pipe
and elbows to the appliance adaptor and
twist-lock for a solid connection.
Note:
a) Twist-lock procedure: Four indentations,
located on the female ends of pipes and
fittings, are designed to slide straight
onto the male ends of adjacent pipes and
fittings, by orienting the four pipe inden-
tations so they match and slide in to the
four entry slots on the male ends, Dia-
gram 1. Push the pipe sections com-
pletely together, then twist-lock one
section clockwise approximately one-
quarter turn, until the two sections are
fully locked. The female locking lugs will
not be visible from the outside, on the
Black Pipe or fittings. They may be locat-
ed by examining the inside of the female
ends.
Diagram 1
b) Horizontal runs of flue must be sup-
ported every three feet. Wall straps are
available for this purpose.
5) Mark the wall for a 10" x 10" (254mm x
254mm) square hole. The center of the
square hole should line up with the center-
line of the horizontal pipe. Cut and frame the
10 inch (254mm) square hole in the exterior
wall where the flue will be terminated. If the
wall being penetrated is constructed of non-
combustible material, i.e. masonry block or
concrete, a 7"(178mm) dia. (7-1/2"(191mm)
dia. for flex) hole is
acceptable.
Diagram 2
Note:
a) The horizontal run of flue must be level,
or have a 1/4 inch (6mm) rise for every
1 foot (.3m) of run towards the termina-
tion. Never allow the flue to run down-
ward. This could cause high tempera-
tures and may present the possibility of
a fire.
b) The location of the horizontal flue termi-
nation on an exterior wall must meet all
local and national building codes, and
must not be blocked or obstructed. For
External Flue Terminal Locations, see
diagram on page 10.
6) The arrow on the flue cap should be
pointing up. Insure that the 1-1/2" clear-
ances to combustible materials are main-
tained. Install the termination cap, diagram 5.
The four wood screws provided should be
replaced with appropriate fasteners for
stucco, brick, concrete, or other types of
sidings.
Note: If installing termination on a siding
covered wall, a vinyl siding stand-
off or furring strips must be used
to ensure that the termination is
not recessed into the siding.
7) Before connecting the horizontal run of flue
pipe to the flue termination, slide the Wall
Thimble (Part # 620-926) over the flue pipe.
Note: Apply sealant "Mill-Pac" to inner
pipe and high temperature sili-
cone sealant to outer pipe on eve-
ry twist-lock joint.
Note: With
D u r a - V e n t ,
the mini-
mum height
is achieved
by installing a
90
o
elbow di-
rectly to the
flue adaptor.
Diagram 4
Diagram 3