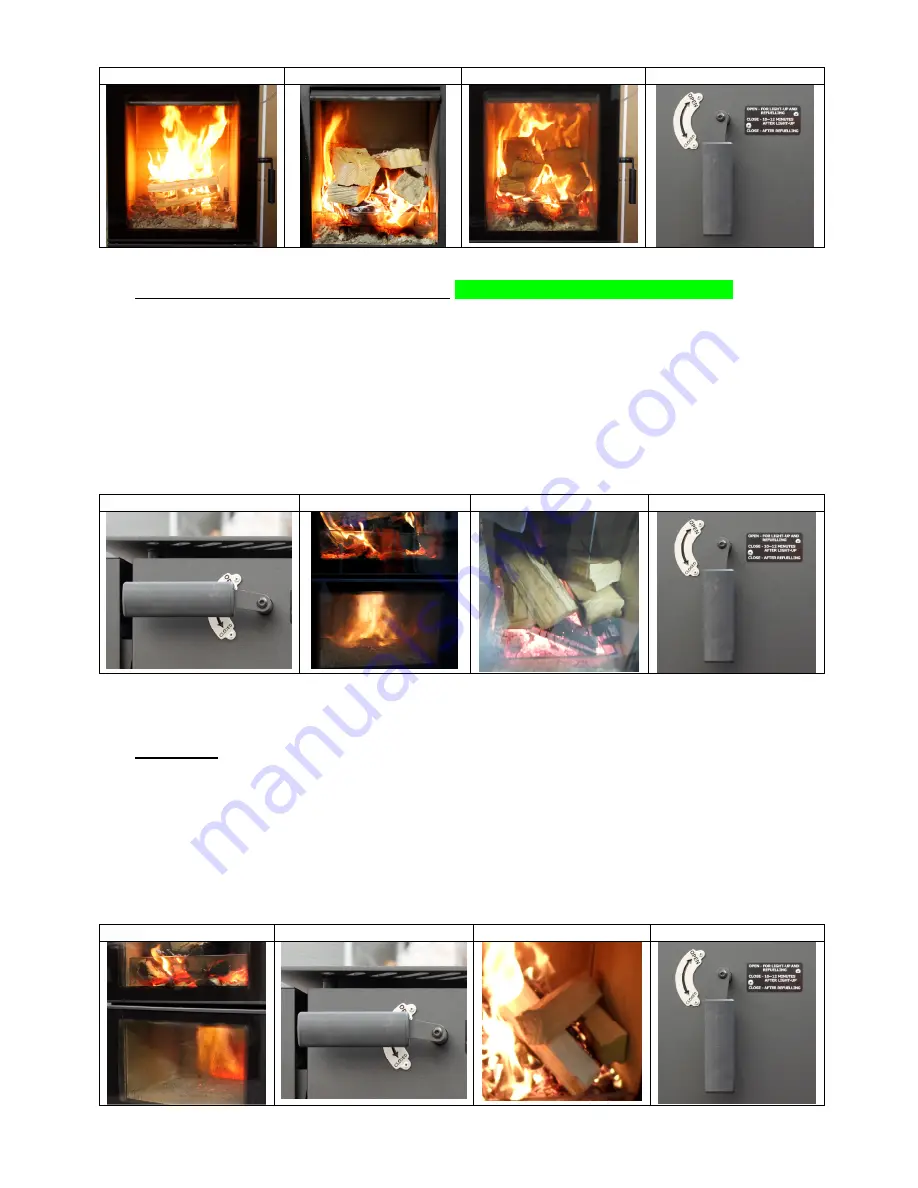
11
5.4A
5.4B
5.4C
5.4D
5.5 Intermediate Load 2 & Door Operations (after 10~12 mins after starting up)
-
(5.5A) Door will not open once damper handle is positioned on “
CLOSE
” because of safety interlock
mechanism.
-
(5.5B) The downdraft flame in the bottom combustion chamber should look like this.
-
When approx. 50% of the intermediated load 1 has burned down, Turn the damper handle to “
OPEN
” positions
-
(5.5C) Open the top combustion chamber slowly, load 4 pieces of intermediate load 2 – approx. 2.5 kg and
close the door
-
(5.5D) Turn the damper handle to “
CLOSE
” position to set the burner back into downdraft mode.
-
Do not ever force to open the top chamber door when damper is in “CLOSE” position
-
Please note if the bottom chamber flame is ‘pulsing’ or ‘puffing’ after closing the damper, open the damper for
another 1-2 mins and then close to return to downdraft mode.
5.5A
5.5B
5.5C
5.5D
Overall the above steps should take around 40-45 mins. This point on, the burner will be hot enough to run in the
downdraft mode for prolonged period.
5.6 Re-fueling
-
(Burner can be refueled with bigger logs once the down-draft is fully established.
-
(5.6A) As fuel burns away the down-draft flame will reduce. This is normal and flame will increase again when
more fuel is loaded.
-
(5.6B) Turn damper handle to “
OPEN
” position, open the top combustion chamber.
-
Use rake and level the ember bed. Particularly leaving good embers around the downdraft injector.
-
(5.6C) Place the 2-3 large size logs weighing approximately 1 kg each on embers in Front-to-Back direction
and close the door
-
(5.6D) Turn the damper handle to “
CLOSE
” position to set the burner back into downdraft mode.
5.6A
5.6B
5.6C
5.6D