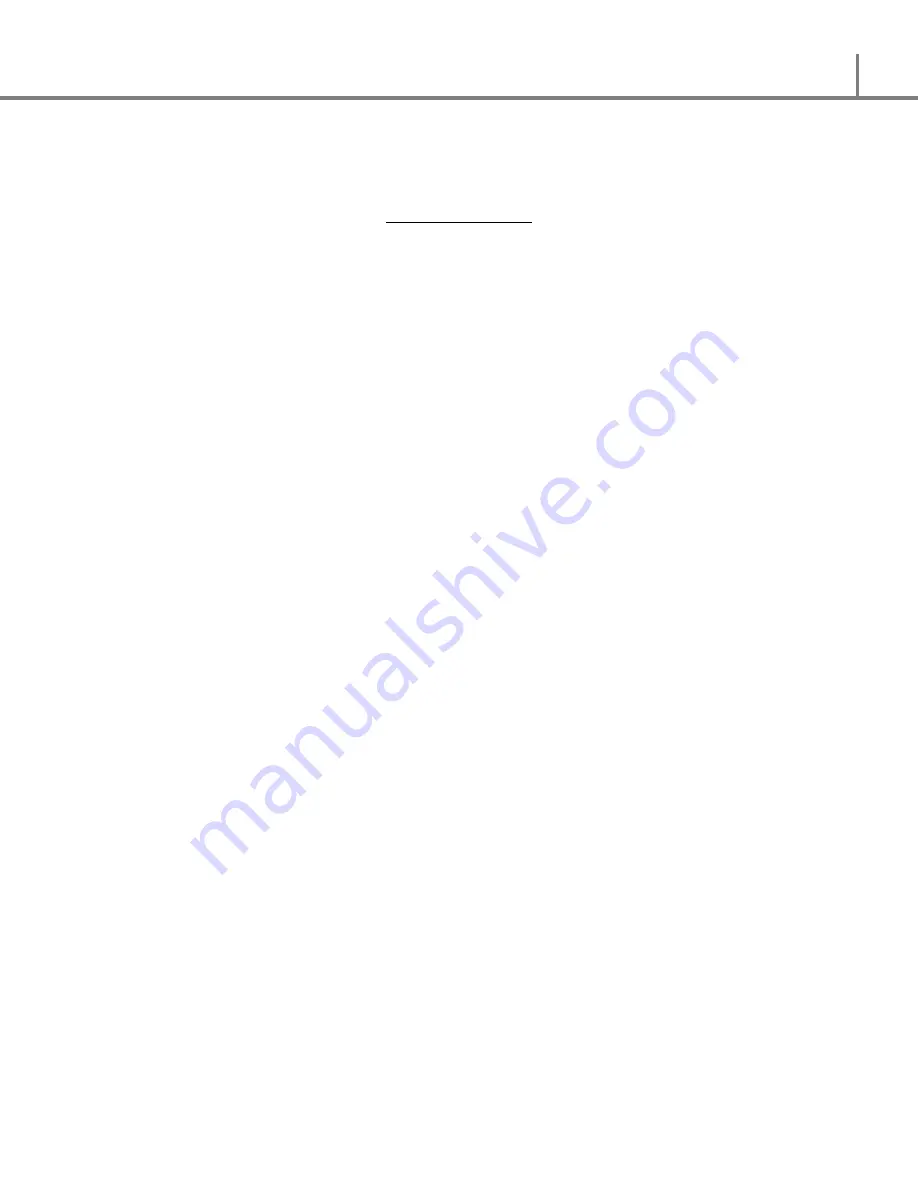
StarLam 1600R User Manual
36
Appendix A4
Tips and Tricks for the StarLam 1600R G3
Start -up Check List
1. Make sure machine power is on.
2. Make sure substrate is properly tensioned to take up core. Pull tension and tape in the center first then
pull tension on each side and tape. Substrate should be tight and not loose and sagging. Use the Que
(green) button to pull tension on the substrate and hold it after taping.
3. Make sure heater is in the raised position. Turn heater on and let it preheat to at least 100 Deg.
Celsius.
4. Open fluid flow valve so that liquid laminate is dispensed onto substrate. Wait until the laminate is
flowing off the sides of the substrate.
5. Start motor at the #2 speed.
6. Lower Heater.
7. Switch cooling fans on.
Let machine run until job is coated.
Clean-Up and Shut Down Check List
1. Shut off the fluid feed valve.
2. Stop the machine before the vinyl spools off of the feed roll. There should be approximately 2 to 3
wraps still on the core (1.5 meters total from the metering rod to the end of the substrate).
3. Using a foam brush push all the remaining laminate off the substrate and into the reclaiming trough.
4. Loosen the fastening screws that hold the metering rod in place and remove the metering rod.
5. Place the metering rod into the cleaning trough and rotate it a few times to wet the rod.
6.