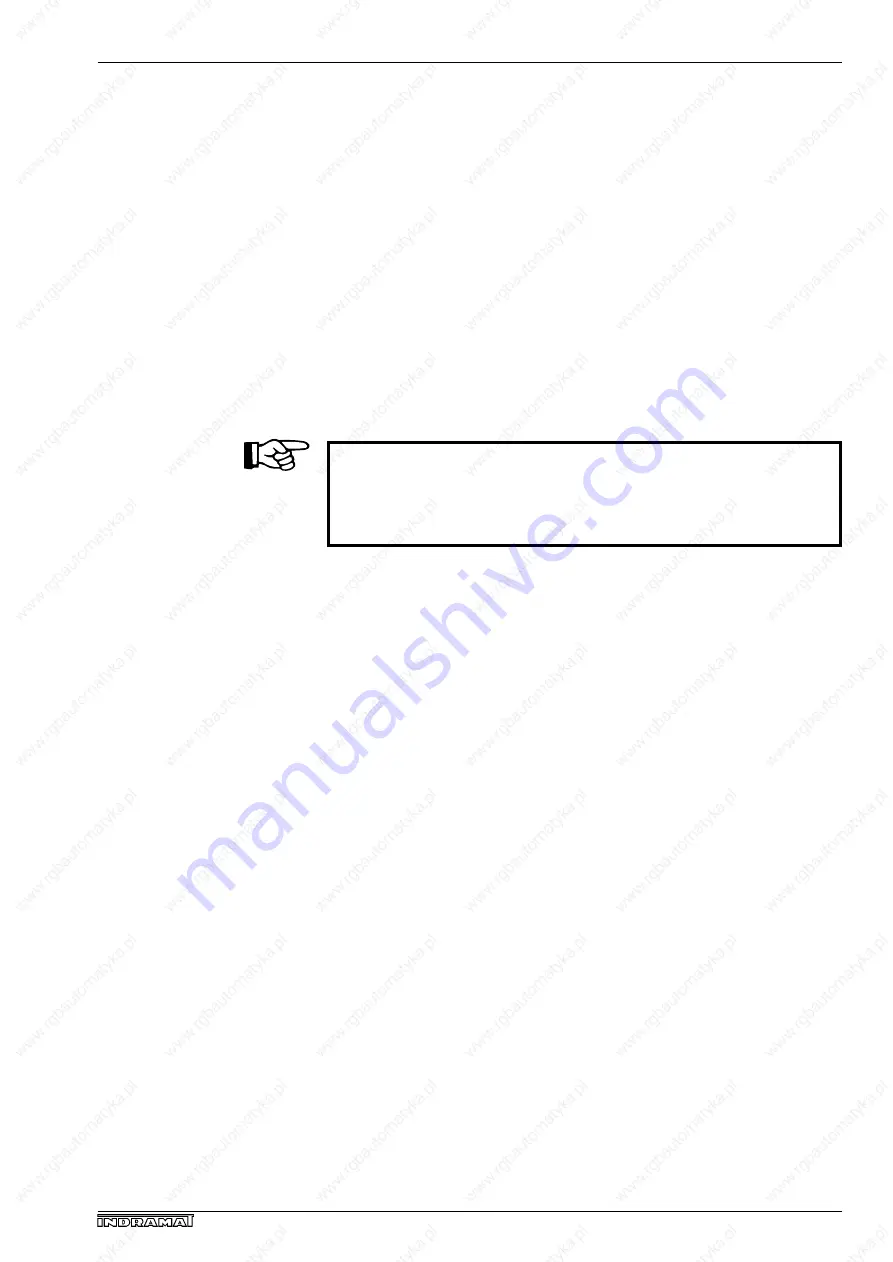
• DOK-DIAX02-DDS02.1*ANA-ANW1-EN-E1,44 • 12.96
72
7. Commissioning the functions of the digital AC servo drive
7.7. Command value
smoothing
When the servo drive is controlled in closed loop by the NC control,
stepped command value signals - due to the control’s cycle time - will
result in torque fluctuations.
The effects of such a stepped command signal are:
– noise generation during acceleration and braking.
– vibration of the machine during interpolation.
This causes:
– increased mechanical stress in the machine.
– increased motor power dissipation.
The command signal emitted by the NC control can be smoothed using
the parameter "Command value smoothing filter time constant". The
recommended smoothing filter time constant is 1/3 the control cycle time.
• If the smoothing filter time constant is too high, this will cause signal
delays in the control loop and result in contouring errors.
• If the step response is desired, cancel the smoothing filter
time constant function by entering 0.25 msec.
An NC control requires position measuring systems to sense the position
of machine axes. These position measuring systems can either be
mounted directly on the machine’s mechanical construction (direct
position measuring system) or on the motor (indirect position measuring
system).
For indirect sensing of the axis position INDRAMAT supplies an interface
as standard on digital drives with ANALOG interface. This interface
comes in two versions:
– indirect relative position sensing with incremental encoder compatible
signals
– indirect absolute position sensing. Refer to Section 7.9 for more details.
The motor feedback senses the position of the rotor in the servo motor,
the process being cyclically absolute. The signal thus obtained under-
goes high resolution conditioning in the drive controller.
The output connector of the ANALOG interface with incremental encoder
emulator (DAE1.1) provides incremental encoder compatible square-
wave signals for evaluation through an external control system.
7.8. Actual-position
sensing by indirect rela-
tive position measuring
system
Indirect relative
position sensing