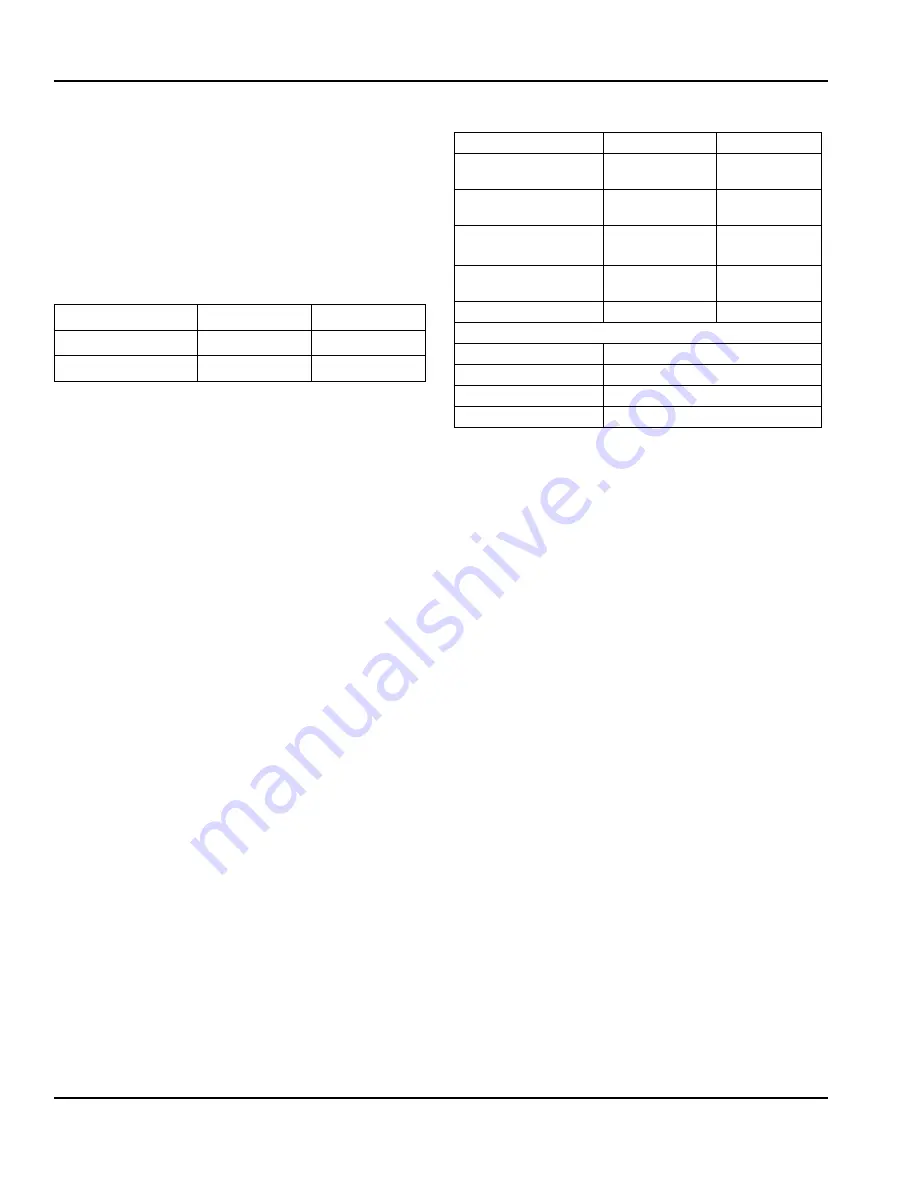
Installation Instructions
Section 2
2-10
Part Number 5031216
01/09
STEP BY STEP INSTALLATION
GENERAL
MII series dispensers have a stainless steel cabinet and
lighted merchandiser standard.
Beverage valves, coldplate connections, drain
connections and electrical components are front
serviceable.
CAPACITIES
SPECIFICATIONS CHART
* This is the optimal pressure. For high foam, decrease the pressure,
for spitting/popping, increase the pressure.
Dispenser
Valves
Ice Storage
MII-302
10 or 12
300 lbs
MDH-302 w/EM
10 or 12
300 lbs
MIN.
MAX
Incoming Plain
Water Pressure
40 psi dynamic
70 psi static
Plain Water Pressure
to Carb Tank
55 psi
65 psi
Ambient
Temperature
40°F
(4°C)
105°F
(41°C)
Co
2
Pressure
(Primary)
90 psi
100 psi
Electrical
115V/60 Hz/1
230V/50-60 Hz/1
Pre-mix Pressure
Normal
60 psi*
Diet
40 psi*
B-I-B (Secondary)
75 psi or according to line run
Flavor Shots
30 psi or according to line run