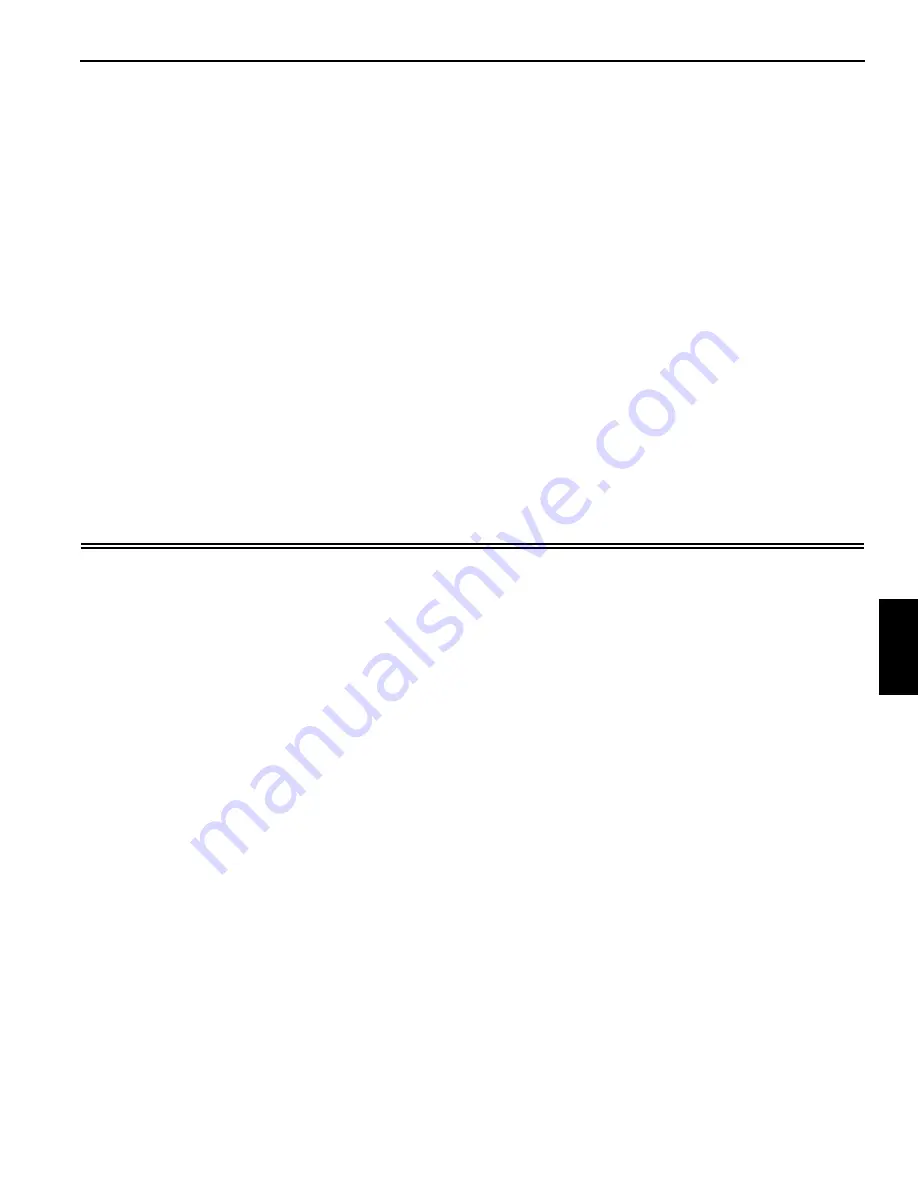
6-1
Published 9-04-2014, Control # 422-08
RT765E-2 SERVICE MANUAL
SWING SYSTEM
6
GROVE
SECTION 6
SWING SYSTEM
SECTION CONTENTS
Description . . . . . . . . . . . . . . . . . . . . . . . . . . . . . . . 6-1
Theory of Operation . . . . . . . . . . . . . . . . . . . . . . . . 6-1
Maintenance . . . . . . . . . . . . . . . . . . . . . . . . . . . . . . 6-3
Swing Motor . . . . . . . . . . . . . . . . . . . . . . . . . . . . . . 6-7
Swing Gearbox And Brake. . . . . . . . . . . . . . . . . . . 6-8
Swing Bearing. . . . . . . . . . . . . . . . . . . . . . . . . . . . 6-10
Swivels. . . . . . . . . . . . . . . . . . . . . . . . . . . . . . . . . . 6-15
Description . . . . . . . . . . . . . . . . . . . . . . . . . . . . . 6-15
Hydraulic Swivel . . . . . . . . . . . . . . . . . . . . . . . . . . 6-17
Two Port Water Swivel . . . . . . . . . . . . . . . . . . . . . 6-19
Electrical Swivel . . . . . . . . . . . . . . . . . . . . . . . . . . 6-20
Swing Lock Pin . . . . . . . . . . . . . . . . . . . . . . . . . . . 6-22
DESCRIPTION
The purpose of the swing system is to allow the crane
superstructure to rotate atop the carrier frame. The
superstructure swing system provides full 360 degree
rotation in both directions and is equipped with free swing
capabilities. The term free swing means that, with the Swing
Brake Switch in the OFF position, the superstructure will
swing freely after the Swing Control Lever is released until it
coasts to a stop or the Swing Brake Pedal is depressed.
Swing is activated using a control lever in the cab. When the
Swing Control Lever is actuated, hydraulic pressure is routed
to the Swing Motor to drive the gearbox in the appropriate
direction. As the gearbox rotates, the pinion gear meshes
with the teeth on the swing bearing and rotates the
superstructure. The maximum rotation is 2.5 rpm. Braking is
accomplished by depressing a Swing Brake Pedal which is a
proportionate control valve that provides a controlled braking
of the swing motion.
The swing system consists of a hydraulic remote controller, a
directional control valve, the swing drive, the swing brake
assembly, the brake pedal and power brake valve, and a
swing brake release solenoid valve.
The crane is equipped with a pin type swing lock as standard
and an optional 360 degree positive swing lock. The 360
degree positive swing lock meshes with the swing gear teeth
at any point of rotation. The pin type swing lock can only be
engaged when the boom is centered over the front or rear of
the carrier. Both swing locks are operated from the cab.
THEORY OF OPERATION
Swing Drive
The hydraulic power for the swing drive (Figure 6-1) is
supplied by the engine driven hydraulic pump. Oil flows from
the pump to the hydraulic swivel. Flow from the swivel is
routed to the service brake dual accumulator charge valve.
Bypass flow from the Dual Accumulator Charge Valve is
routed to the Front Steering Flow Divider Valve in the Swing
Directional Control Valve. Bypass flow from the flow divider
valve is used to supply the Swing Directional Control Valve.
When the hydraulic remote control is positioned to select
right or left swing, the flow through the control valve is
directed to the Swing Motor. If the Swing Brake Selector
Switch is in the OFF position, the superstructure will rotate in
the desired direction. Shifting the control to neutral and
depressing the brake pedal will stop the swing.
Swing Brake
The hydraulic power for the swing brake is supplied by the
pressure reducing/sequence valve in the swing brake and
armrest lockout manifold. With the Swing Brake Selector
Switch positioned to ON, the Swing Brake Release Valve
blocks the regulated flow to the brake release port and spring
Reference Only