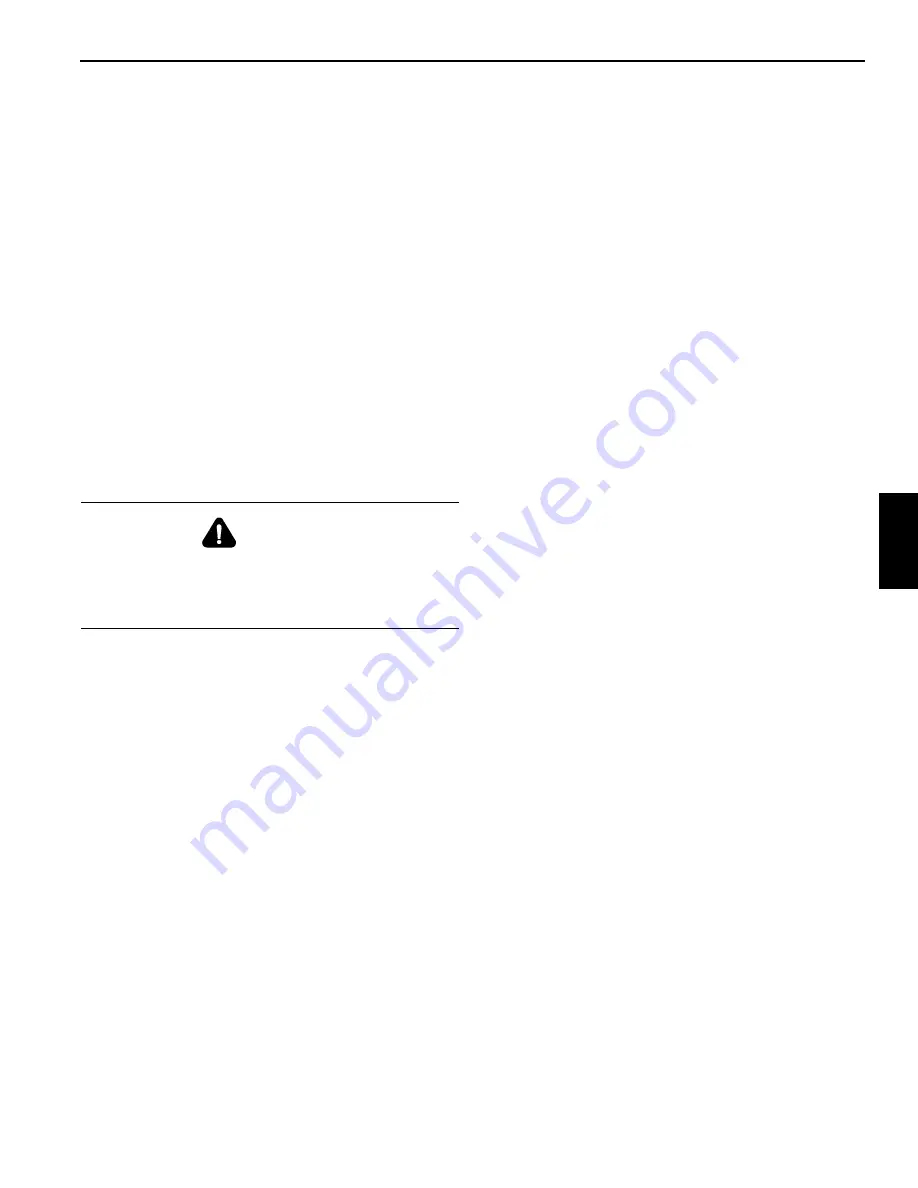
5-7
RT765E-2 SERVICE MANUAL
HOIST AND COUNTERWEIGHT
5
Published 9-04-2014, Control # 422-08
GROVE
hoist line pull and load holding test must be conducted
following the repair work.
Oil Sampling
Oil Change
The hoist gear oil must be changed after the first 100
operating hours then on an annual basis, at a minimum
thereafter. In severe duty applications, the gear oil should be
c h a n g e d e v e r y s i x m o n t h s . U s e t h e r e c o m m e n d e d
lubricants. Refer to
Gear Oil Sampling and Analysis
Proper gear oil sampling and analysis is a vital part of a
c o m p r e h e n s i v e p r e v e n t i v e m a i n t e n a n c e p r o g r a m .
Information obtained from the oil analysis allows the
m a i n t e n a n c e t e c h n i c i a n t o s u b s t i t u t e p r e v e n t i v e
maintenance for more costly unscheduled down time or a far
more dangerous failure. Early detection of accelerated
component wear allows the scheduling of corrective
maintenance.
Prepare the hoist by cleaning the drain plug area and drain
extension tube in order to obtain an uncontaminated sample.
Operate the hoist in both directions for one or two minutes to
thoroughly mix the gear oil then take the sample from the
midstream flow of the oil to obtain an accurate representation
of the oil condition. After taking the oil sample continue with
the oil change or refill the hoist gear cavity to the proper level
with recommended lubricant.
General Guidelines for Iron Contaminant
Level
100-500 ppm
Normal
500-800 ppm
Caution - Abnormal Sample. Change oil and retake sample
after 50 hours of operation. If second sample is above 500
ppm, remove hoist from service and perform tear-down
inspection to determine source of contamination.
800+ ppm
Unacceptable. Remove hoist from service and perform tear-
down inspection to determine source of contamination.
Iron contaminant levels will be on the high side of “Normal'
during initial break-in.
Equally important as the level of contamination is the change
in level of contamination. An effective oil analysis program
should provide the technician with a view of the progression
of wear or a trend. If a sample shows a sudden rise in
contaminant level action should be taken to determine what
has changed.
NOTE:
Oil analysis alone cannot detect nor warn against a
fatigue failure.
Brake Test Procedure
These planetary hoists have a spring applied, hydraulically
released, multiple disc brake inside the hoist housing. This
brake holds a suspended load when the directional control
valve is in neutral, or when hydraulic power is lost. An over-
running brake clutch assembly permits the power train and
drum to rotate in the direction to lift a load, while the brake
remains fully applied. A load cannot be lowered, however,
without applying hydraulic pressure to the release port and
releasing the brake.
(Test to be performed with no load on the hoist)
Remove and cap or plug the brake release line from fitting in
the hoist brake release port.
With the hydraulic power unit running, move the directional
control valve handle slowly to the full open, lowering position.
Increase the engine speed, if necessary, to bring system
pressure up to the relief valve setting. The hoist drum should
remain stationary.
If the hoist drum rotates, the hoist should be disassembled
and the brake components should be examined for wear. In
addition, the brake springs should be measured for the
correct free length in those hoist using helical compression
springs.
CAUTION
Hot oil may cause personal injury and/or burns to
unprotected skin. Make certain the oil has cooled to a safe
temperature (typically less than 110°F or 43°C) before
taking an oil sample, changing oil or servicing the hoist.
Reference Only