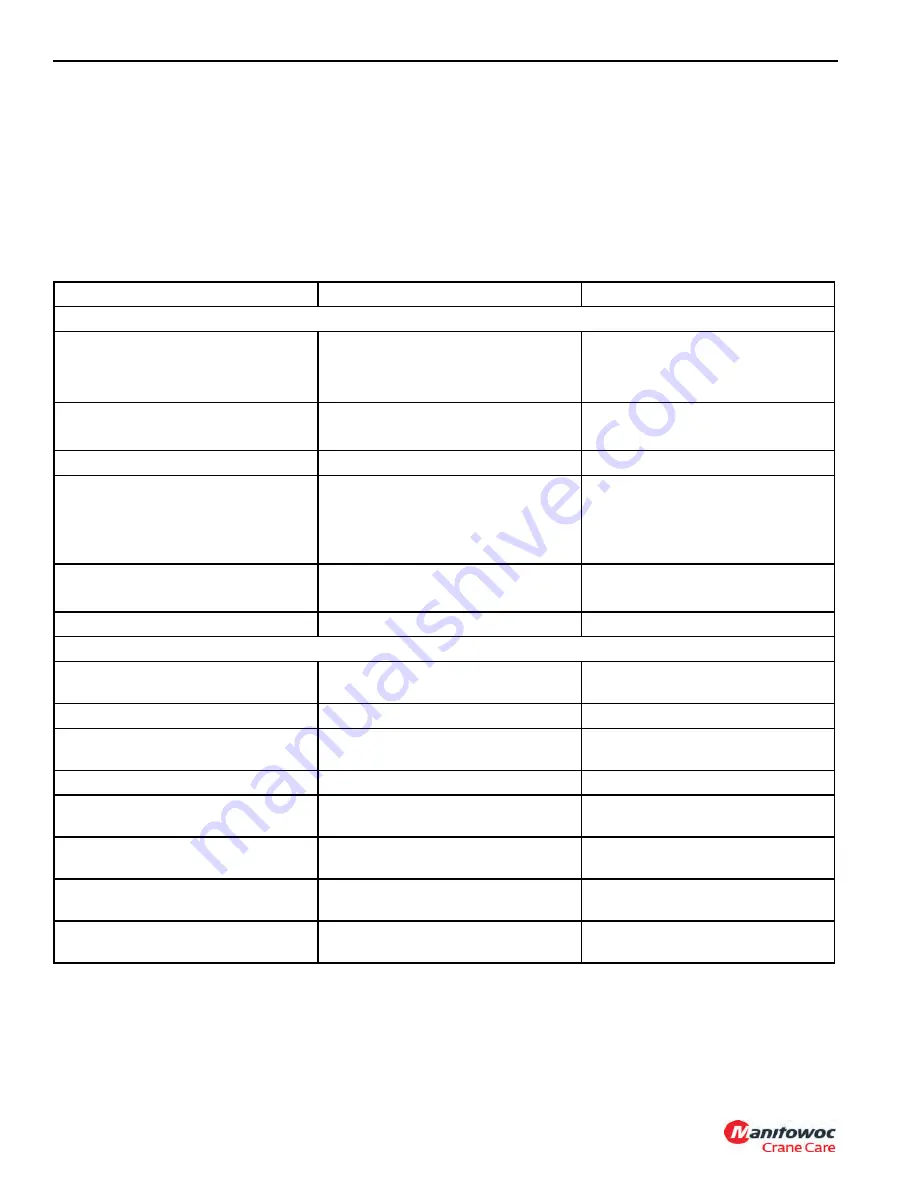
HYDRAULIC SYSTEM
RT765E-2 SERVICE MANUAL
2-30
Published 9-04-2014, Control # 422-08
VALVES
General
This subsection provides descriptive information for several
of the main hydraulic valves used on this crane. For a listing
of the valves, the circuit they are used in, and their physical
location, refer to Table 2-3. Refer to Figure 2-17 and
Figure 2-18 for valve locations.
The description of each valve given here is for the valve
itself. For information on how each valve functions in the
individual circuits, refer to the description and operation
procedures of that circuit.
Table 2-3
Valve Usage Table
Valve Name
Circuit Used In
Physical Location
Superstructure
Directional Control Valves
Hoist/Lift /Telescope
Swing/Steer
Counterweight Removal (Optional)
Superstructure (Right Side)
Superstructure (Right Side)
Rear Turntable
Hydraulic Remote Controllers
(Joysticks)
Hoist/Lift
Swing/Telescope
Right Armrest
Left Armrest
Dual Accumulator Charge Valve
Service Brakes
Superstructure (inside left side)
Swing Brake/Armrest Lockout Manifold
• Swing Brake Release
• Crane Function
Swing
Each hoist, swing, lift and telescope
controller circuit
Superstructure (right side)
Superstructure (right side)
Holding Valves
Lift
Telescope
Lift cylinder (bolt on)
Telescope cylinder port blocks
Boom Lock Valve
Telescope
Telescope Cylinder Retreat Circuit
Carrier
Integrated Outrigger/Rear Steer Valve
Outrigger and Rear Steer
On front face of carrier frame front
cross member
Outrigger Control Manifold
Outrigger
Front and Rear Outrigger Boxes
Axle Lockout Valve (Double Solenoid
Valve)
Rear Axle Lockout
On carrier left side rear center frame
cross member
High Speed Boost Selector Valve
Hoist and Telescope
On swivel port #6
Priority Flow Control Valves
Hydraulic Oil Cooler, Transmission Oil
Cooler, Fan Motor
On carrier, RH frame rail
Priority Flow Control Valves
Service Brake and Air Conditioner
Circuit
On carrier, LH frame rail
Cross Axle Differential Lock Solenoid
Valve
Optional axle differential lock
On carrier front side rear center frame
cross member
Axle Disconnect Solenoid Valve
Two/Four Wheel Drive
On carrier front side rear center frame
cross member
Reference Only