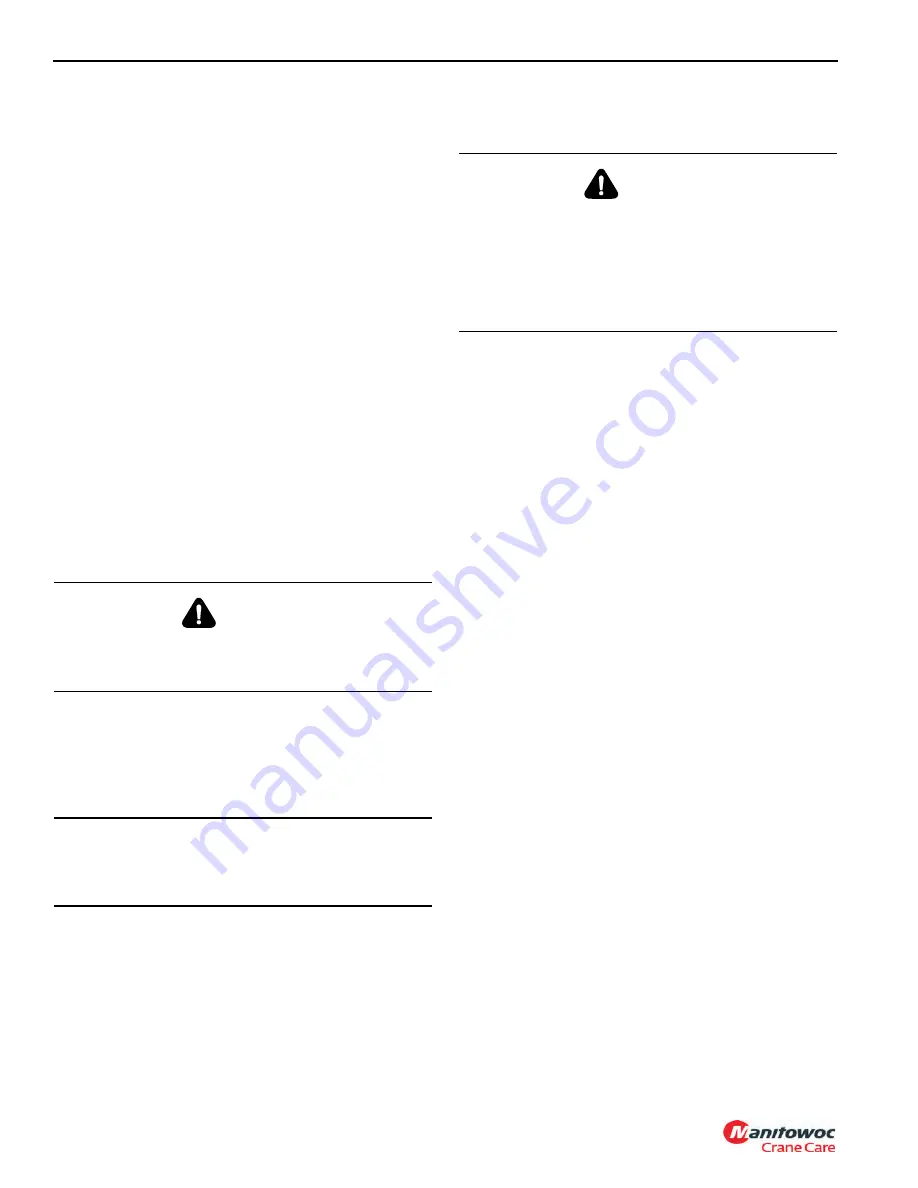
6-10
Published 9-04-2014, Control # 422-08
SWING SYSTEM
RT765E-2 SERVICE MANUAL
SWING BEARING
Description
The swing bearing is an anti-friction roller bearing that mates
the superstructure to the carrier. The bearing inner race is
bolted to the superstructure and the outer race is bolted to
the carrier. The inner race contains two grease fittings for
lubrication of the bearing which are hosed to two fittings at
the front of the turntable center section. The outer race also
contains two grease fittings and incorporates gear teeth that
mesh with the pinion gear of the swing gearbox to provide
rotation.
Maintenance
General
The swing bearing is the most critical maintenance point of
the crane. It is here, at the centerline of rotation, that
stresses of loads are concentrated. In addition, the bearing
provides the only attachment between the superstructure
and carrier. Therefore, proper care of the bearing and
periodic maintenance of the turntable-to-bearing attach bolts
-IS A MUST -to ensure safe and efficient operation.
Torquing Turntable Bolts
General
Maintaining proper torque value for bolts is extremely
important for structural strength, performance, and reliability
of the crane. Variations in torque can cause distortion,
binding, or complete separation of the superstructure from
the carrier.
Proper identification of bolt grade is important. When marked
as a high strength bolt (grade 8), the serviceman must be
aware of bolt classifications and that he is installing a high
strength heat-treated tempered component and the bolt
must be installed according to specifications. Special
attention should be given to the existence of lubricant and
plating that will cause variation from dry torque values. When
a high strength bolt is removed, or un-torqued, the bolt must
be replaced with a new bolt of the same classification.
KNOW YOUR TORQUE WRENCH! Flexible beam type
wrenches, even though they might have a pre-set feature,
must be pulled at right angle and the force must be applied at
the center of the handle. Force value readings must be made
while the tool is in motion. Rigid handle type, with torque
limiting devices that can be pre-set to required values,
eliminate dial readings and provide more reliable, less
variable readings.
NOTE:
If multipliers and/or special tools are used to reach
hard to get at areas, ensure torque readings are
accurate.
Torque wrenches are precision instruments and must be
handled with care. To ensure accuracy, calibrations must be
made on a scheduled basis. Whenever there is a possibility
that a torque wrench may have been either overstressed or
damaged, it should immediately be removed from service
until recalibrated. When using a torque wrench, any erratic or
jerking motion can result in the application of excessive or
improper torque. ALWAYS use a slow, even movement and
STOP when the predetermined value has been reached.
If it is reported by the crane operator or suspected that the
crane has been overloaded beyond the capacities specified
above the bold line on the crane’s capacity chart, then all
turntable bolts must be inspected for looseness and
retorqued to specifications.
Turntable bolts should be torqued according to the
procedures outlined in this section.
When using step wrenches, calculated wrench settings are
valid only when the following conditions are met.
1.
Torque wrenches must be those specified and forces
must be applied at the handle grip. The use of handle
extensions will change applied torque to the bolt.
2.
All handles must be parallel to the step wrench during
final tightening. Multiplier reaction bars may be
misaligned no more than 30 degrees without causing
serious error in torque.
CAUTION
Failure to maintain proper torque of the turntable bearing
attaching bolts will result in damage to the crane and
possible injury to personnel.
CAUTION
Repeated re-torquing may cause bolts to stretch. If bolts
keep working loose, they must be replaced with new bolts
of the proper grade and size.
WARNING
It is mandatory that bearing attaching bolts be inspected
for lack of torque and retorqued, as required, after the first
300 hours of crane operation. The bolts may loosen in
service due to vibration, shock-loads, and temperature
changes, therefore, periodic inspection should be
accomplished every 500 hours thereafter, ensuring the
bolts are properly torqued.
Reference Only