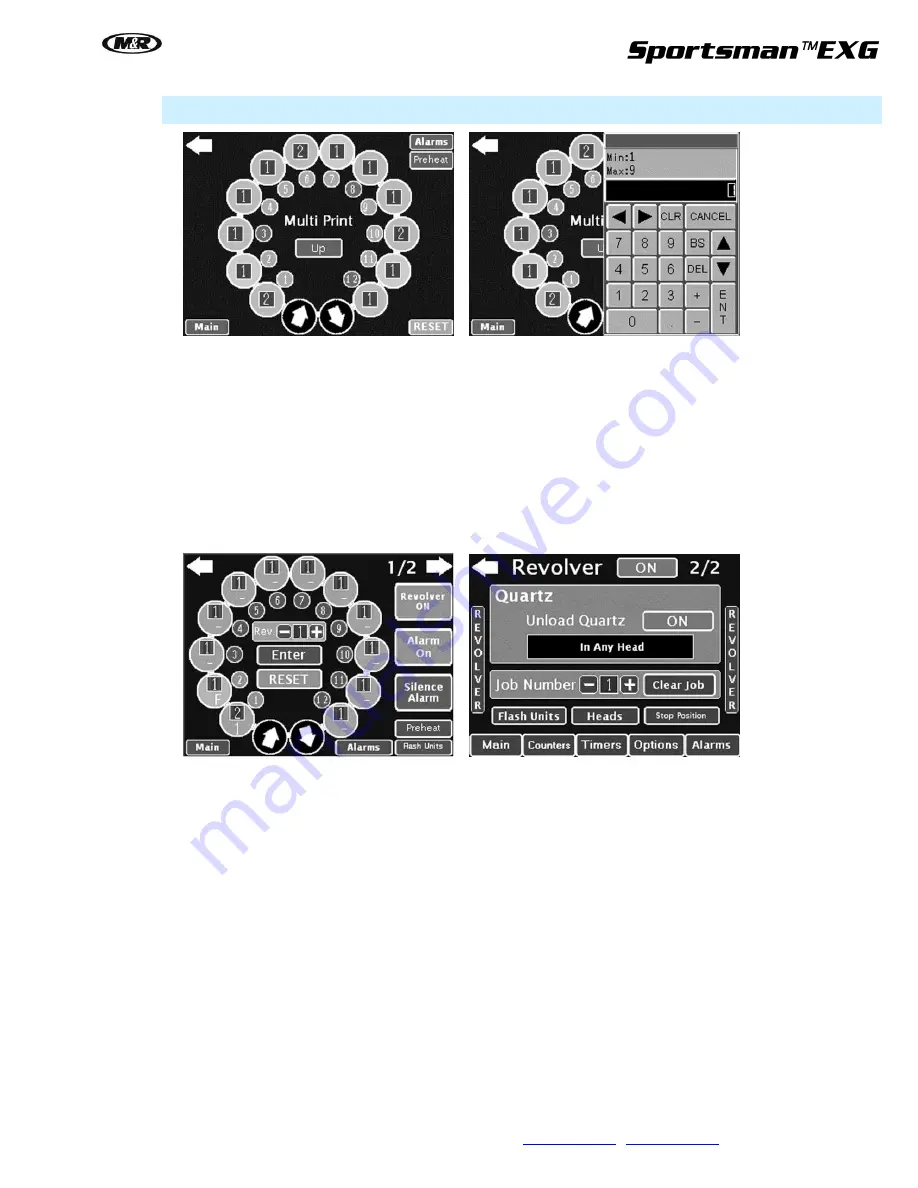
M&R Companies 440 Medinah Road Roselle, IL 60172 USA
27
Tel: +630-858-6101 Fax: +630-858-6134
V.050316
Note
: Set the
Up/Down
position in the
Options/Multi Print
menu.
Alarm On/Disabled
The
Alarm On/Disabled
button is used to activate the audible alarm signal that sounds just before the completion
of a programmed Revolver print sequence. Press the
Alarm On/Disabled
button once again to turn off the
audible signal.
Silence Alarm
The
Silence Alarm
button is used to silence the audible alarm signal that sounds just before the completion of a
programmed Revolver print sequence. Press the
Silence Alarm
button to turn off the audible signal.
Preheat
and
Flash Units
can also be accessed from the first Revolver screen.
Press the
Forward Arrow
to access the second Revolver screen.
Quartz
Unload Quartz
Press the Unload Quartz
Off/On
button. The indication changes to
On
and a Q is shown in the unload station.
Select the print stations to operate as Quartz Flash stations by pressing the indication
In Any Head
to view the list
of possible selections. Possible selections include
In Any Head
,
Head # 1
,
Head # 2
,
Head # 3
,
Head # 4
,
Head
# 5
,
Head # 6
,
Head # 7
,
Head # 8
,
Head # 9
,
Head # 10
,
Head # 11
,
Head # 12
and
Unload Station
.
Press on the Head number,
In Any Head
or
Unload Station
to make your selection. To use the unload station as
a
Quartz Flash
station, you must have the
Unload Quartz
indication at the top of the screen selected to
On
.
Job No.
The
Job No.
indicates the current job being programmed. Press the plus (+) to increase the Job No. Press the
minus (-) to decrease the Job No. Press
Clear Job
to clear a previous job.
Flash Units
,
Heads
and
Stop Position
can also be accessed from the second Revolver screen. Press the
Back
Arrow
to return to the first Revolver screen.