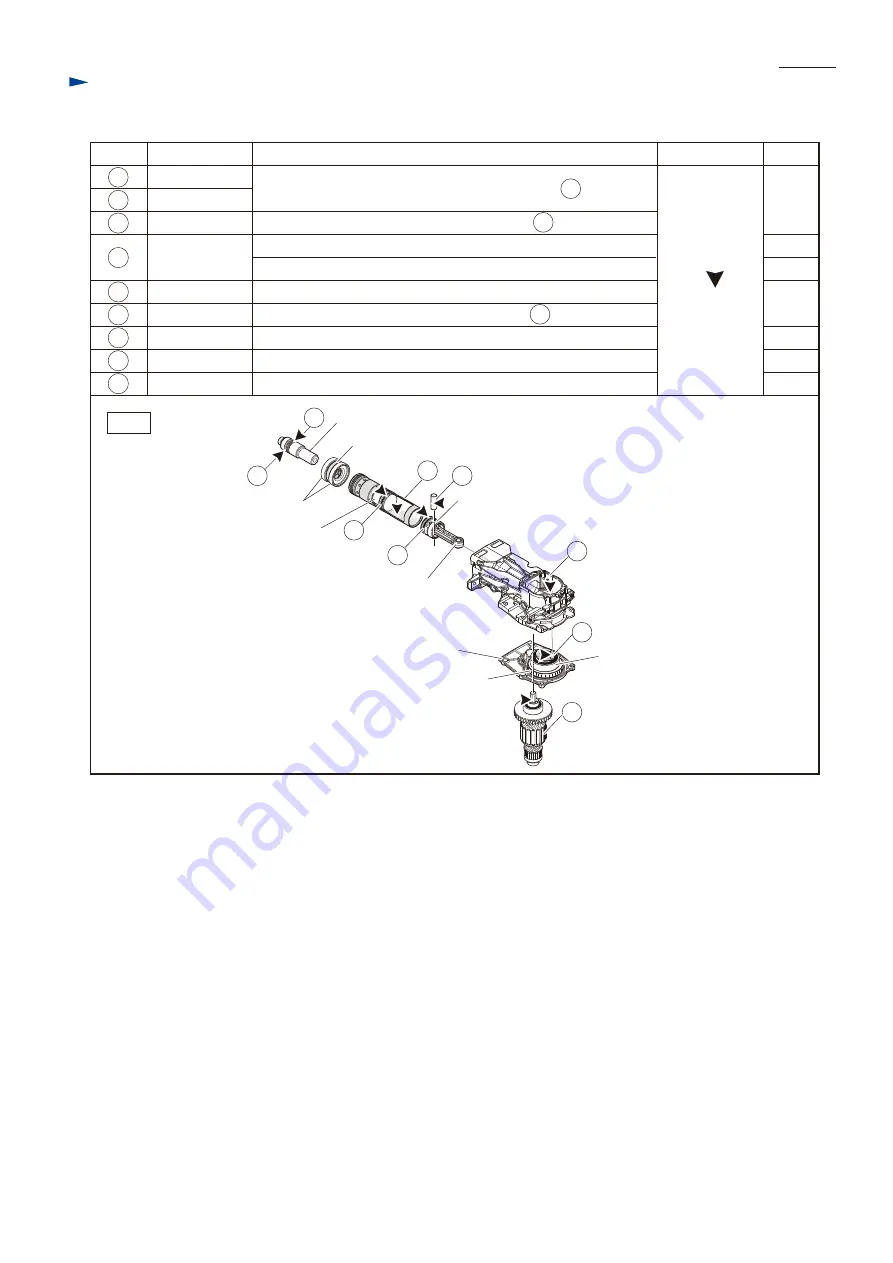
P 3/ 17
R
epair
[2] LUBRICATIONS (cont.)
Makita grease R
No. 00
Item No.
Description
Portion to lubricate for Impact bolt section and Crank section
Amount
Lubricant
36 37
38
34
62
66
77
37
36
34
38
Pin 12
Cylinder 40
O ring 44
O ring 31.5
Crank housing
Crank shaft
Armature
Whole portion
Space between Piston and Striker
Space between Impact bolt and Striker
Whole portion for smooth action of Striker in 36 Cylinder 40
Whole portion for smooth action of Impact bolt in 24 Tool holder
Whole portion for smooth action of Piston in 36 Cylinder 40
Space where Helical gear 57 and Crank shaft rotate
Pin portion where Connecting rod accepts
Drive end (Gear portion)
62
66
77
25
26 Impact bolt
Helical gear 57
Gear housing
Rubber ring 24
Ball bearing 6206LLU
Shoulder sleeve
Piston
Striker
25
26
X ring 21
Fluoride ring 28
40g
10g
a little
a little
a little
10g
10g
Connecting rod
Fig. 2