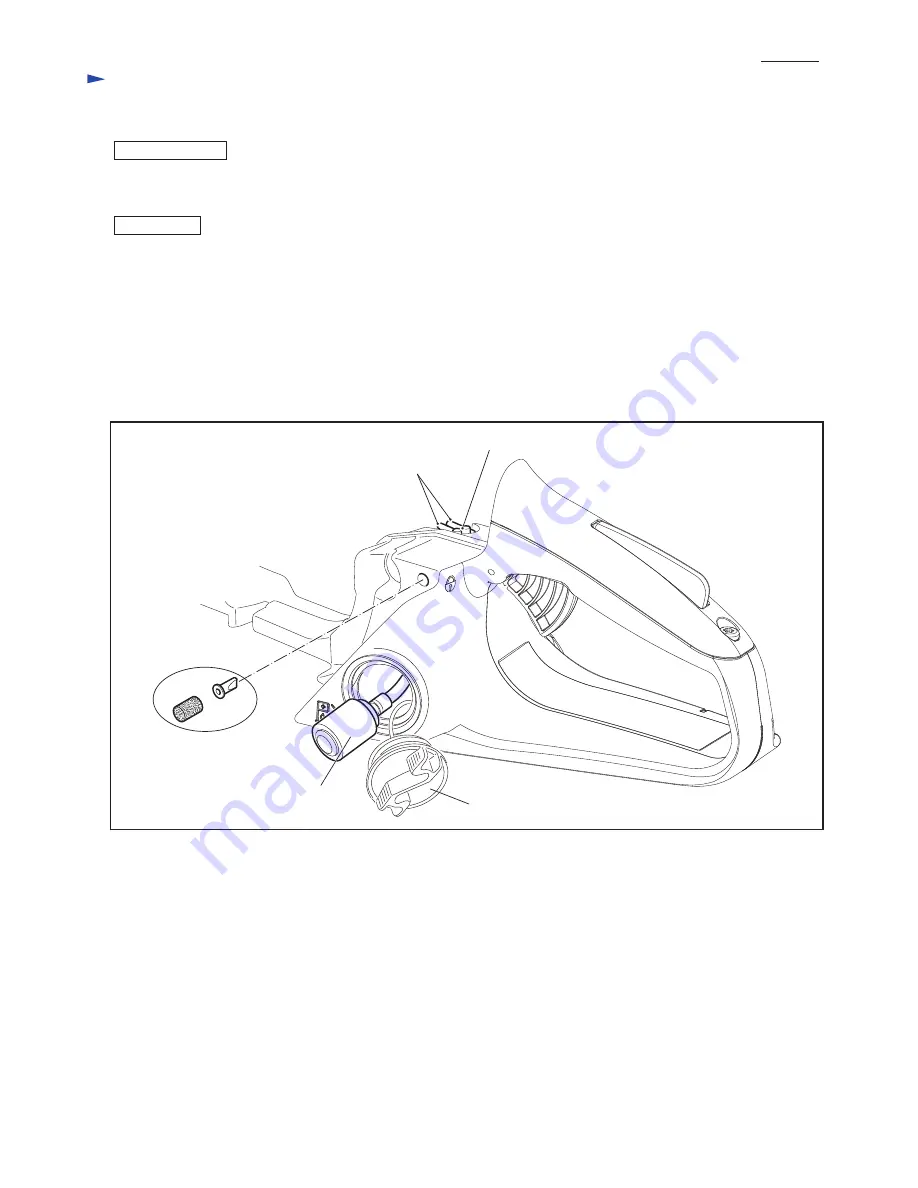
P 1
3
/ 1
6
(1) Referring to “DISASSEMBLY of
[2]-11. Tank assembly
”, disassemble the machine as drawn in
Figs. 35
and
34
.
(2) Using long-nose pliers, carefully pull out the one end of Fuel line from Fuel nipple. (Refer to
Figs 38 and 29.
)
Note
: Connect the one end of Fuel nipple to 1R127 (Re;
Fig. 30
), and fill the other of Fuel nipple.
Fasten Tank cap complete to Fuel Tank. Then, adjust the pressure value to 0.03MPa.
When the pressure value is descent, check the following parts:
•
Air valve set
• Ends of Fuel nipple
• Intake of Fuel nipple • Gasoline filter
• O ring 11.5 on Fuel nipple • O ring 29.5 of Tank cap complete
When the pressure is ascent, replace Air valve set with the new one.
Important
: Supply Soap liquid onto the suspicious surface of Fuel leakage during the pressure test.
After the above steps, reverse the disassembling procedure of “DISASSEMBLY of
[2]-11
Tank assembly”.
• Pick up Gasoline filter with a bent wire carefully out of Tank. (
Fig. 38
)
Do not use Pliers because the tips may scratch Fuel line.
Do not pull Gasoline filter/ Fuel line by force without care because Fuel line may be removed from the intake of Fuel nipple
inside Tank.
•
Turn Fuel nipple slightly counterclockwise and then remove it from Tank assembly with small-slotted screwdriver carefully.
Note
: Do not lever Nipple at the ends on the top. They may be broken off.
Ends of Fuel nipple
(Refer to
Fig. 26
)
Fuel nipple
Air valve set
Gasoline filter
Tank cap complete
R
epair
DISASSEMBLY
ASSEMBLY
[2] DISASSEMBLY/ ASSEMBLY
[2]-13. Fuel tank
Fig. 38
[2]-14. How to remove Gasoline filter/ Fuel line