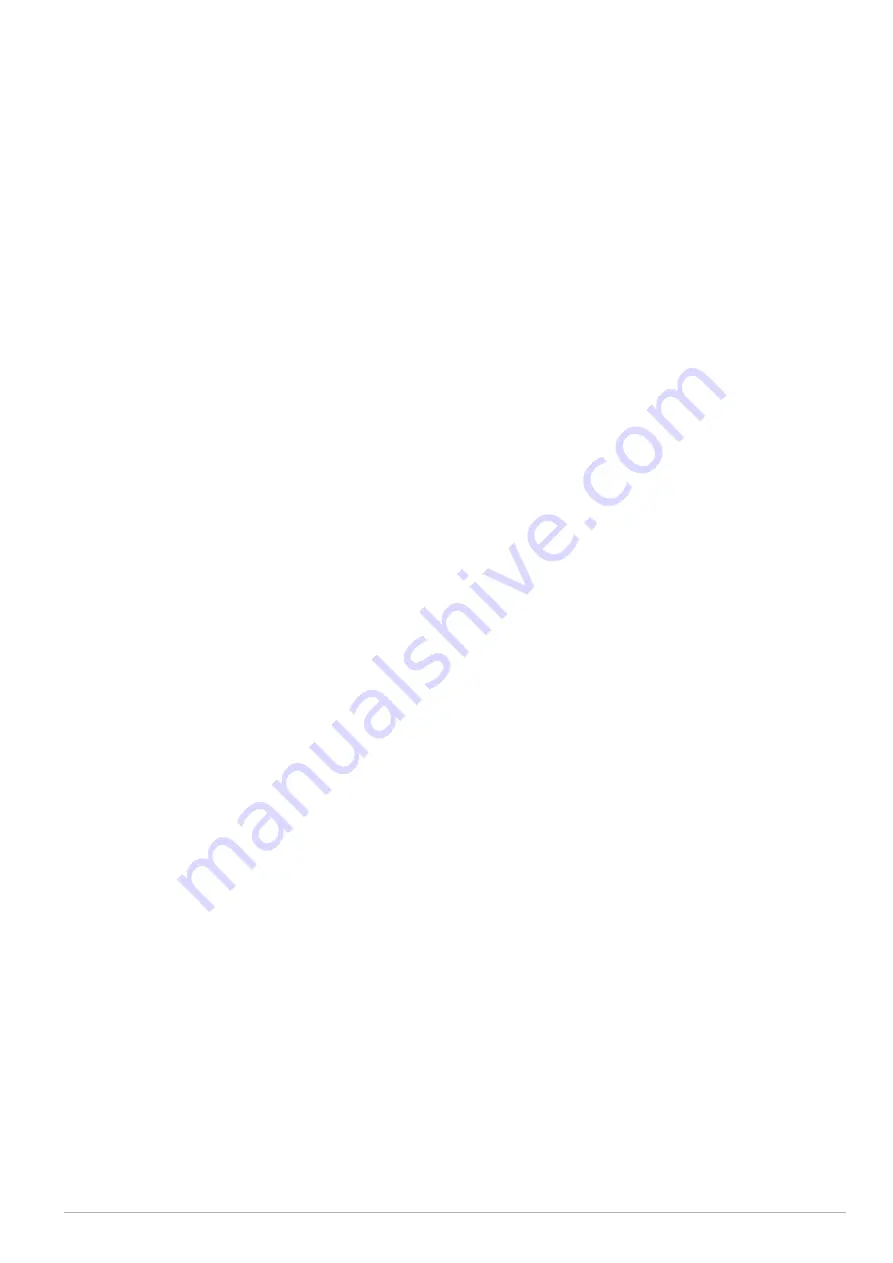
27
www.major-equipment.com
E. Vacuum Pump Maintenance
How to uninstall the from the tanker:
PTO:
1. Stop the power take-off of the tractor;
2. Remove the cardan shaft from the power take-off of the rotary blades vacuum pump
3. Remove the connecting pipe that joins the rotary blades vacuum pump to the tank car, by loosening the metal
band and sliding the pipe from the adjustable elbow
4. Remove any hydraulic connections
5. Remove the clamping screws and disinstall the rotary blades vacuum pump
Pulley
1. top the power take-off of the tractor
2. Remove the driving belts.
3. Remove the pipe that connects the rotary blades vacuum pump to the tank car. To accomplish this, loosen the
metal clamp and pull the pipe out of the elbow
4. Remove any plumbing connections
5. Remove the mounting screws and remove the rotary blades vacuum pump
Hydraulic
1. S top the hydraulic system
2. Remove the hydraulic connections to the motor
3. Remove the pipe that connects the rotary blades vacuum pump to the tank car. To accomplish this, loosen the
metal clamp and pull the pipe out of the elbow
4. Remove any plumbing connections;
5. Remove the mounting screws and remove the rotary blades vacuum pump.
How to disassemble the pump - Back Assembly
MEC 1000-1600-2000-3000-4000-5000-6500-8000
1.
Remove the back cover or the lubrication pump (together with the connector joint) from the flange;
2.
Remove the screws from the back flange;
3.
U se two screws for screwing into the threaded extraction holes until the flange is removed;
MEC 9000-11000-13500
1.
Remove the rear cover or oil pump (together with the connecting joint) from the flange;
2. Remove the seeger ring from the rear pin;
3.
Remove the screws from the rear flange.
4.
Screw two screws into the threaded extraction holes just until the flange can be removed;
STAR - AGRI /V (with rear cast iron oil tank)
1. Remove the tank cover and the lubrication pump (together with the connector joint) from the back tank;
2. Remove the screws from the back tank;
3. U se two screws for screwing into the threaded extraction holes until the tank is removed;
STAR - AGRI /F (with rear flange and extractable side sheet oil tank)
1. Close the oil cock placet on the tank
2.
Remove the back cover with the lubrication pump (together with the connector joint) from the flange;
3.
Remove the screws from the back flange;
4.
U se two screws for screwing into the threaded extraction holes until the flange is removed;
How to disassemble the pump - Front Assembly
PTO:
1. Unscrew the screws of the gearbox cover;
2. Use two screws for screwing into the threaded extraction holes until the cover is removed;
3. Remove the gear with splined shaft using an extractor if necessary;
Summary of Contents for 1150 Slurry Vac
Page 1: ...MAJOR Standard LGP Alpine Challenger and Tandem Tankers Operator s Manual Parts List ...
Page 54: ...50 www major equipment com 3500 Challenger Assembly ...
Page 62: ...58 www major equipment com MEC 9000 11000 13500 M P ...
Page 68: ...64 www major equipment com Wired Controls ...
Page 69: ...65 www major equipment com ...
Page 70: ...66 www major equipment com ...
Page 73: ...69 www major equipment com TANDEM AXLES STANDARD DUTY ...
Page 74: ...70 www major equipment com TANDEM steered BNR2RW1XC001 GF TANDEM steered BNR2RW1XC001 P ...
Page 77: ...73 www major equipment com TANDEM steered GEK2250 TANDEM fixed GEK2560 ...
Page 80: ...76 www major equipment com STEERED TANDEM AXLE HEAVY DUTY AFTER HR16634 BNRAXL1XCN001_E A ...
Page 84: ...80 www major equipment com STEERED TANDEM AXLE HEAVY DUTY AFTER HR16634 BNRAXL1XCN001_E C ...
Page 88: ......