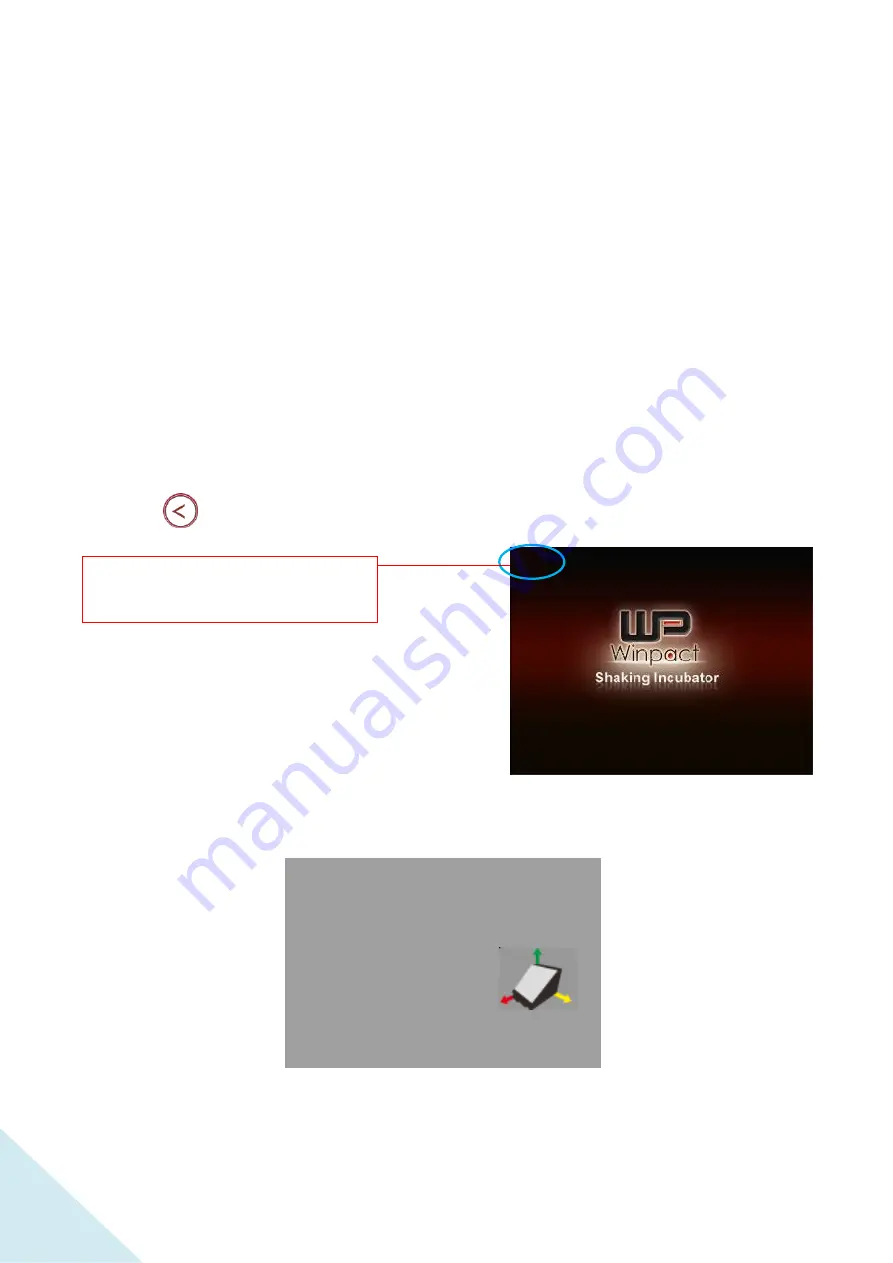
93
Allowance of Shaking/ Vibrating Settings
To prevent system over-shaking due to unexpected hardware malfunction, the manufacturer has
implemented a preventive mechanism defined in the six parameters to detect the abnormality
and respond immediately by shutting down the system. For example, if the device is working on
an uneven surface, the warning of over shaking can remind users and encourage users to arrange
a proper working environment for the device.
It is highly recommended that user conduct step 1 before step 2 for balance calibration after the
first-installation of device.
Step1
Hold the enter key until the number counts to the range of
1000 to 1500
.
(Pressing
and hold at the same time to fast forward to the favorable number)
Move device meanwhile checking the PV value to be as close as BASIC value. After the adjustment,
user can proceed to step 2 “Allowance of Shaking/ Vibrating Settings”.
Release the button when the number
goes between 1000 and 1500
1150
Mount Adjust Mode
PV Basic
X
30 27
Y
-15 -13
Z
270 270
Adjust mount, let PV equal to Basic.
Summary of Contents for Winpact SI-200
Page 2: ...2...
Page 14: ...14 PT 100 Sensor Port External Temp Port Spare Installation Hole Fan...
Page 27: ...27 A maximum of 9 microplate holders can be installed if the same type of holders is used...
Page 37: ...37 Features of Control Panel LCD Screen Key Pad 1 2 3 5 4 6 7 8...
Page 61: ...61 Step8 When the installation complete press Close to exit the installation dialogue...