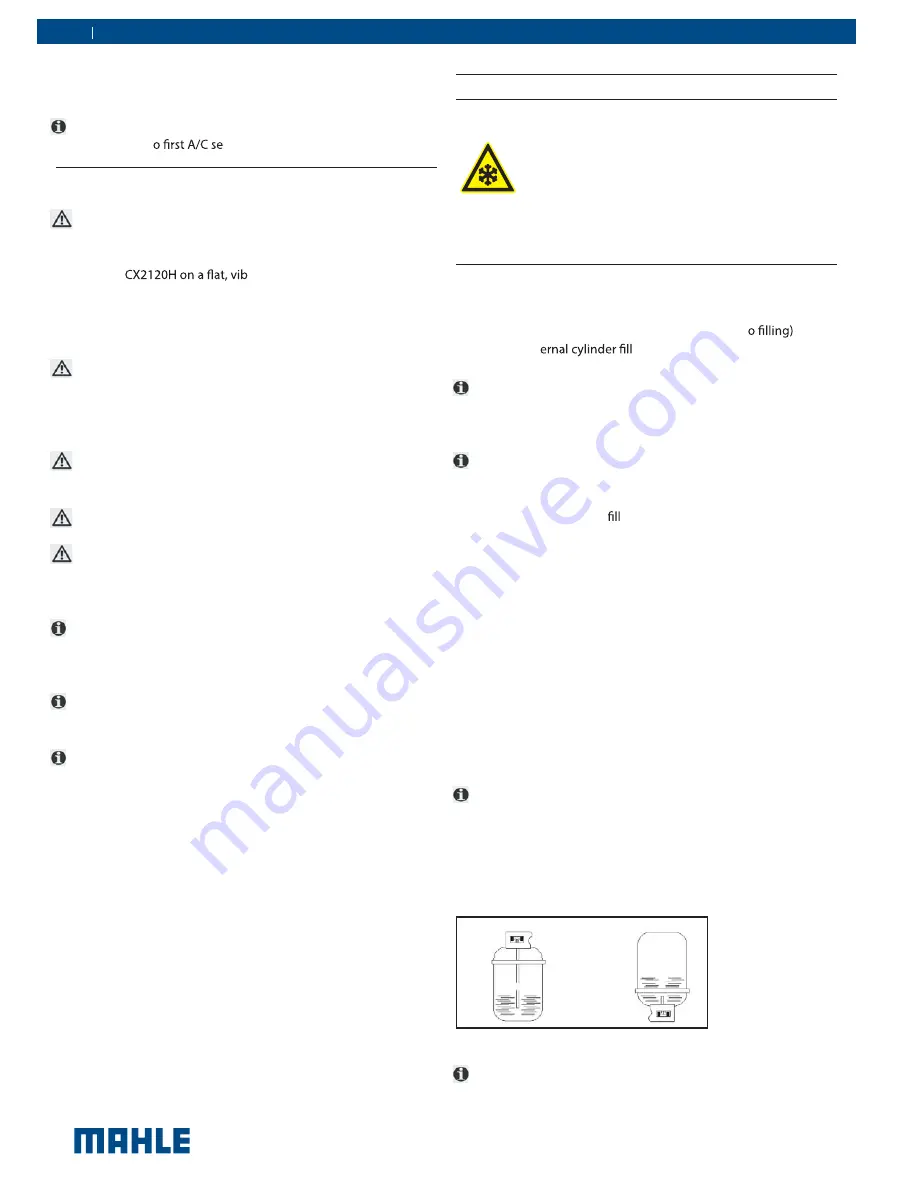
© MAHLE
14 | ACX2120H | Commissioning
en
6.
Commissioning
t
All the operations described in Section 5 and 6 must be per
-
formed prior t
rvice.
6.1
Connections and positioning
m
The ACX2120H is designed for 110V, 50/60Hz. Follow the
information on the ACX2120H rating plate.
1.
Set the A
ration-proof surface.
2.
Actuate the caster brake to stop the ACX2120H from rolling.
3.
Connect the power supply cable to the power supply.
4.
Switch on the main switch.
m
The unit must be positioned on a stable, horizontal surface to
ensure correct operation. Unit must be in an area with proper
ventilation and at least 10cm from any potential obstacle to
its internal ventilation.
m
Keep unit out of rain and excessive humidity as moisure could
cause irreparable damage.
m
Prevent exposure to direct sunlight and excessive dust.
m
Unit must be properly grounded with the power plug ground
pin. Failure to ground unit can cause damage and constitutes
a risk of fatal injury or shock to the operator.
t
Do not unplug any internal electrical connections and only
have internal components opened and repaired by trained
customer service personnel.
t
Contact customer service in the event of any transportation
damage (e.g. oil leakage).
t
Leave quick couplings closed when unit is not in use and at
end of vehicle service operations.
6.2
First start-up verification
X
Check the service hoses for damage.
X
Firmly connect the service quick-release cou -
plings to the service hoses.
X
Wear protective goggles.
X
Wear protective gloves.
Execute the following actions in sequential order by following the
procedure as shown on the display:
—
Gas weight check (vacuums entire refrigerant circuit to
ensure no contaminants are in system prior t
—
First int
o
It is possible to interrupt the initial check and print a report
in which the status of the check is reported (if printer option
was purchased).
t
Equipment cannot operate in automatic mode until all the
steps of initial check are completed.
1.
Set the internal cylinder
to desired quantity (min. 3kg).
2.
Follow on-screen instructions.
3.
Make sure hoses are disconnected from any external source
at this time.
4.
Start the procedure that initially creates vacuum in the internal
refrigerant circuit (approximately 15 minute process).
5.
Once message is displayed, the unit can be connected to the
external cylinder and the valves opened.
6.
Just before the targeted refrigerant amount is reached, unit
will pause and prompt user to close external refrigerant tank
connection.
7.
Once this is done, the unit will continue to recover the refriger -
ant from the hoses and end once this is completed. The total
amount recovered will then be displayed.
t
Check the type of source tank, two types are available:
—
Connect to the the liquid valve and keep tank in the upright
position to transfer refrigerant.
—
Refrigerant cylinder without plunger (single valve):
Refrigerant cylinder with plunger (typically 2 valves):
Connect to the available valve and invert tank to transfer
refrigerant.
Fig. 13: Virgin refrigerant cylinder tank types
t
The LP (blue) gauge indicates the pressure inside the external
cylinder.
Refrigerant causes frostbite on the skin
Warning - Risk of frostbite from escaping
refrigerant