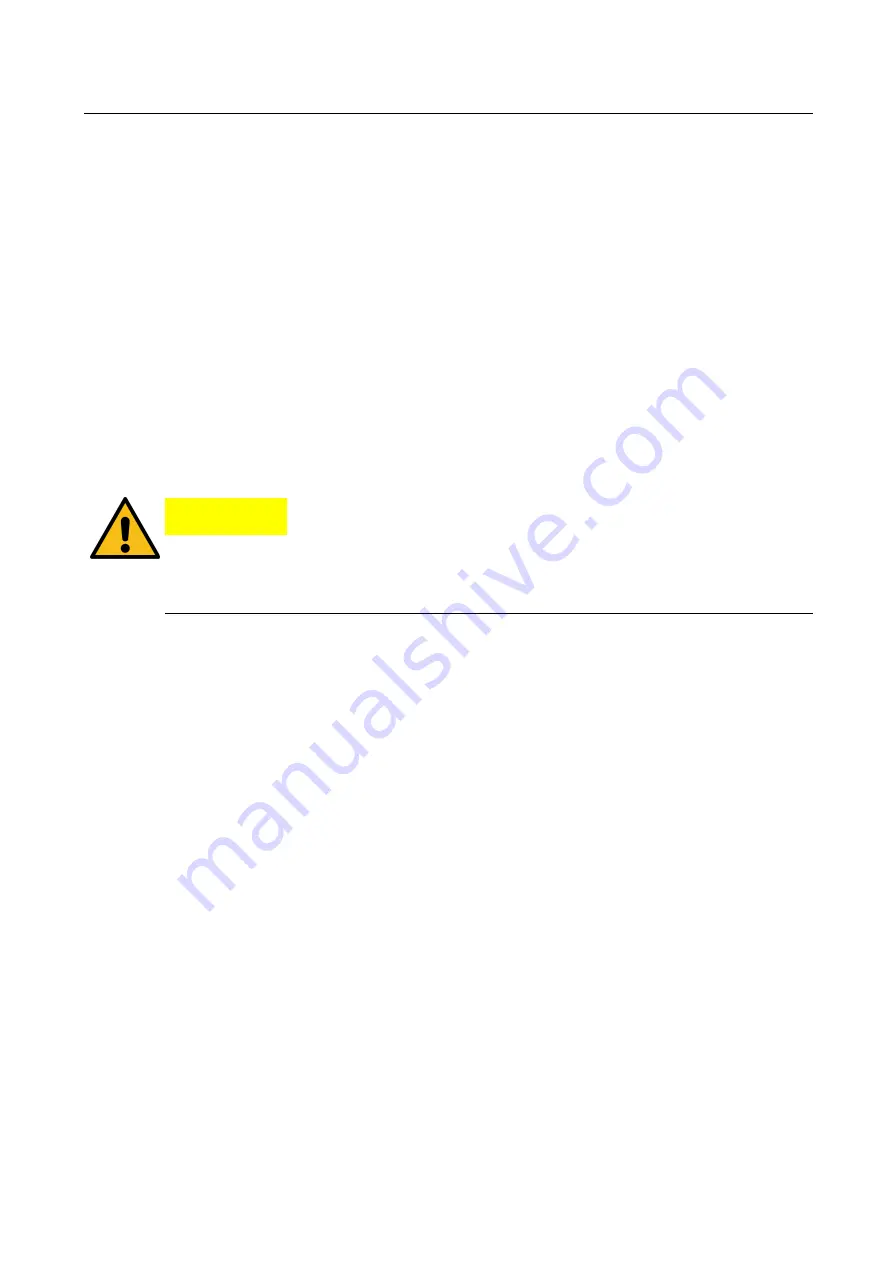
26
BA082901-en
5.10.4
Manual Lowering with 2.5 kW or 5.5 kW Power Unit in the Control Desk
1 Open the cap of seat valve
+A-M1
(by turning it anticlockwise), making sure not to
lose the sealing ring.
2 Remove the coil with plug-in connector from the valve and tighten the cap (without
coil) finger-tight. The seat valve is now disabled.
3 Place the sliding shoe underneath the latch on side
+A
. You may need to use the
hand pump to do this. After several pumping movements, the latch can be raised by
hand.
If you use the hand pump, be aware of offset! Raise the sides one after the other –
the valve on the other side must be closed in each case.
4 Repeat steps 1 to 4 for side
+B
.
5 Use the key ring to pull up lowering valve
+C-M2
slowly
. The lift is lowered. Be
aware of offset and hazard zone! To stop the lowering movement, release the valve.
CAUTION
The height offset should remain < 50 mm – adjust the height of the runways as neces-
sary. Either use the hand pump to raise the lower side or use bypass valve
+C-M4.A
or
+C-M4.B
to lower the higher side.
6 Lower the lift to the home position, remove the vehicle, rectify errors.
7 Raise the lift without any load.
8 Remove the sliding shoes.
9 Attach the coils with plug-in connectors to both seat valves and tighten the caps
finger-tight (by turning them clockwise). The valves have now been returned to a
functioning state.
Summary of Contents for DUO CM Series
Page 27: ...27 BA082901 en A M1 B M1 C M4 A C M4 B C M2...
Page 29: ...29 BA082901 en C M5 A C M4 B C M4 A C M5 B Hand pump...
Page 31: ...31 BA082901 en A M1 B M1 C M2 C M4 A C M4 B...
Page 33: ...33 BA082901 en C M5 A Hand pump C M4 B C M4 A C M5 B Stopcock Buttons...
Page 35: ...35 BA082901 en A M50 A B M50 B C M54 A C M54 B...
Page 37: ...37 BA082901 en A M50 A B M50 B Stopcock Buttons...