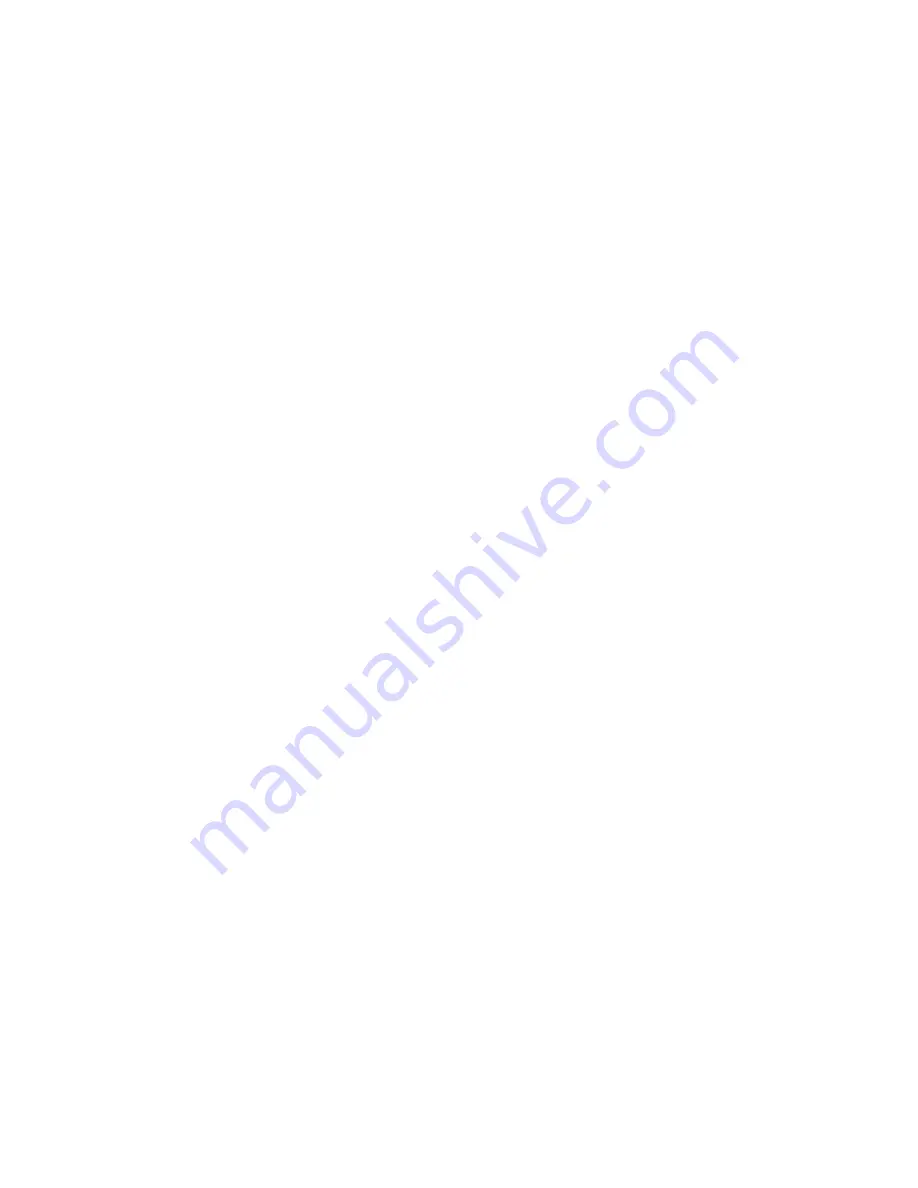
Model OE-10
Installation, Operation and Maintenance
Page
11
Rev. 4/20/07
L
IFTING A
V
EHICLE
1) Insure that the lifting arms are parked, out to
full drive thru position.
2) Position the vehicle in the service bay so that
the vehicle’s center of gravity is on a line
between the two columns, and so the vehicle
is centered between the two columns.
D
O NOT EXCEED
2250
POUNDS PER ARM
.
D
O NOT ATTEMPT TO LIFT THE VEHICLE WITH
ONLY TWO ARMS
,
AS THIS WILL VOID THE
WARRANTY
I
NSURE THAT THE HIGHEST POINT ON THE
VEHICLE WILL CONTACT THE
O
VERHEAD
L
IMIT
S
WITCH
B
AR
.
D
O NOT PLACE THE VEHICLE IN THE SERVICE BAY
BACKWARDS
.
R
EFER TO THE VEHICLE MANUFACTURERS SERVICE
MANUAL
,
TECHNICAL BULLETINS
, “V
EHICLE
L
IFTING
P
OINTS
G
UIDE
” (ALI/LP-G
UIDE
)
OR OTHER
PUBLICATIONS TO LOCATE THE RECOMMENDED
LIFTING POINTS
.
3) Position the arms and adapters so all four
pads contact the vehicle simultaneously.
The vehicle should remain level during lifting
.
4) Raise the lift until all four wheels are off the
ground. Test the stability of the vehicle by
attempting to rock the vehicle. Check adapters
for secure contact with vehicle lift points. If the
vehicle seems unstable, lower the lift and
readjust the arms. If the vehicle is stable,
raise the vehicle to a height a few inches
above the desired working height.
5) Lower the vehicle until the safety latches on
both columns engage. The vehicle should
remain level when both latches are engaged.
If one side engages and the other continues to
descend, stop lowering the vehicle, raise it
several inches, and try again to engage both
latches.
Always lower lift into locks before entering
the area beneath the vehicle.
A
lways use safety stands when removing or
installing heavy components.
L
OWERING
A V
EHICLE
1) Insure that the area under the vehicle is clear
of personnel and tools.
2) Raise the vehicle until both latches are free.
3) Disengage the latches by pulling down and
holding the lock release lever.
4) Lower the vehicle by depressing the lowering
valve handle.
5)
Continue to lower the vehicle until the
carriages stop against the base plate. Retract
the extension arms, and park them.
M
AINTENANCE
To avoid personal injury, permit only qualified
personnel to perform maintenance on this
equipment.
The following maintenance points are suggested
as the basis of a preventive maintenance
program. The actual maintenance program
should be tailored to the installation. See
ANSI/ALI ALOIM booklet for periodic inspection
checklist and maintenance log sheet.
•
If lift stops short of full rise or chatters, check
fluid level and bleed both cylinders per
Installation Instructions.
•
Replace all Safety, Warning or Caution Labels
if missing or damaged (
See Installation
instructions page 3.
)
Daily
•
Keep lift components clean.
•
Check for loose or broken parts.
•
Check hydraulic system for fluid leaks.
•
Check adapters for damage or excessive wear.
Replace as required with genuine Challenger
Lifts parts.
•
Check lock release activation. When properly
adjusted, the idler column lock should rest
firmly against the back of the column when
engaged and against the spring mount tab
when disengaged.
Weekly
•
Check synchronizer cables and sheaves for
wear. Replace as required with genuine
Challenger Lifts parts.
•
Check lock release cable adjustment per
Installation Instructions step 42.
IMPORTANT: I
F IDLER SIDE LOCK PAWL DOES
NOT FULLY DISENGAGE
,
DAMAGE MAY RESULT
TO IDLER SIDE CARRIAGE AND OR CABLE
SYNCHRONIZING SYSTEM
.
•
Check synchronizer cable tension per
Installation Instructions. Adjust if necessary.
Monthly
•
Torque concrete anchor bolts to 80 ft-lbs.
•
Check overhead shutoff switch. While raising
lift, operate overhead shutoff bar. Power Unit
motor should stop when bar is raised.
•
Lubricate carriage slide tracks with heavy
viscous grease. (Grease all (4) corners of both
columns.)
If any problems are encountered, contact
your local service representative
.
A2151_MAGNUM.doc