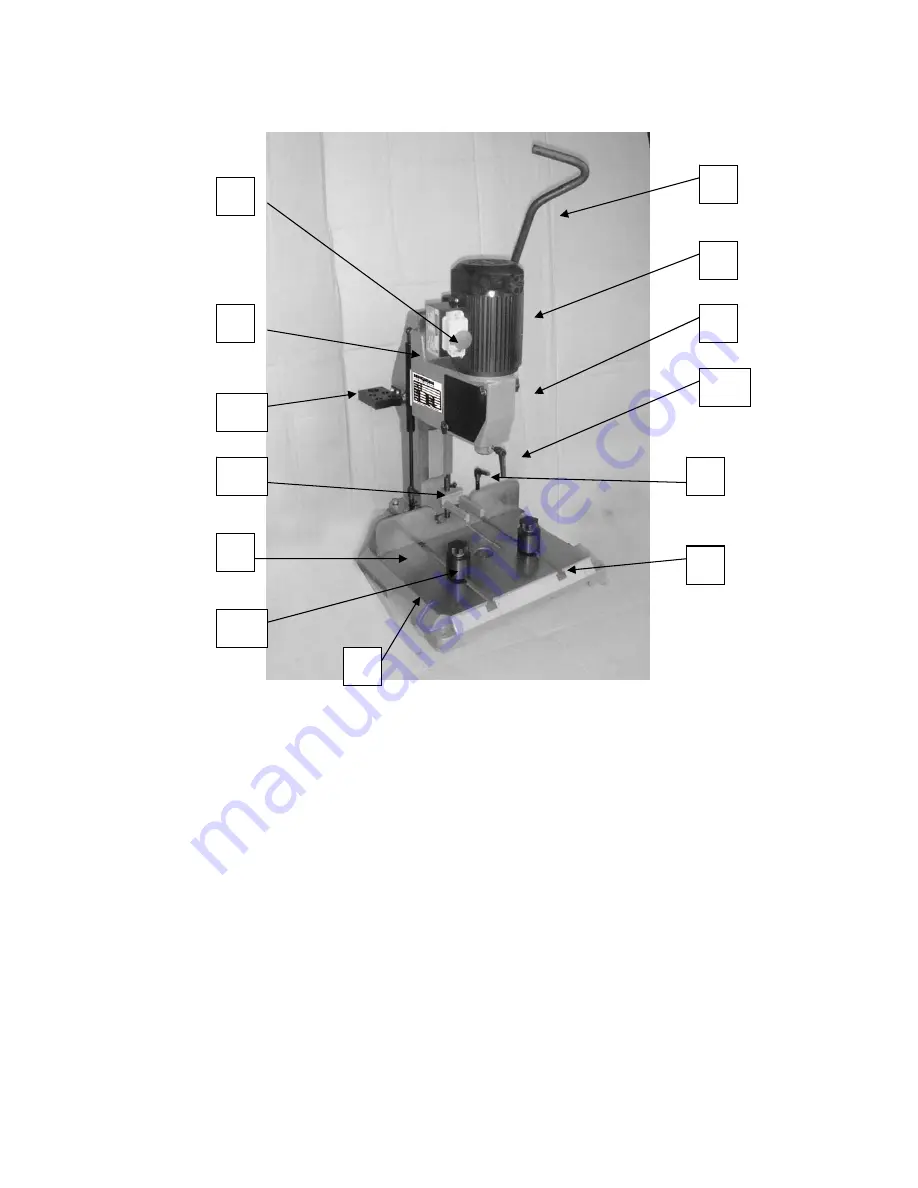
IDENTIFICATION OF MAIN PARTS AND COMPONENTS
1. DOWNFEED
HANDLE
2. MOTOR
3. ON/OFF
SWITCH
4. GAS
HEAD-CYLINDER
5. EXTENSION
WING
6. FENCE
7. BASE
8. FENCE LOCKING LEVERS
9. HEAD
10. WORKPIECE HOLD-DOWN
11. TABLE ROLLER
12. CHISEL LOCKING LEVER
13. CHUCK KEY AND CHISEL HOLDER
1
2
3
4
6
7
8
12
13
11
5
9
10