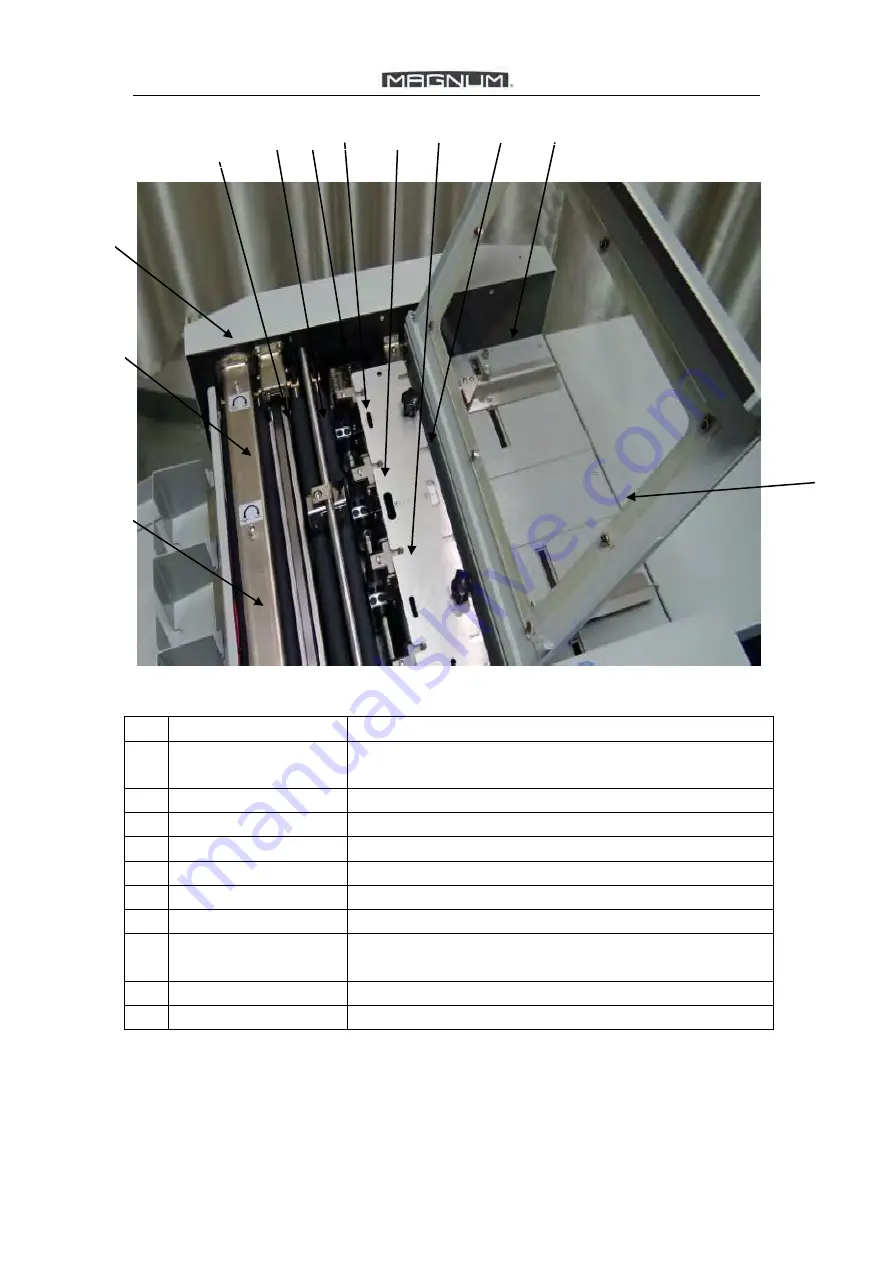
MCC-35
7
No. Description
Remark
1
Crease Depth
Adjust Screw
Clockwise adjust to shallow; anticlockwise adjust to
deep
2
Cross Cutter
Cut paper in cross direction
3
Lag wheel Set
Adjust the roller pressure
4
Slitter #1
Slit the side edge of paper
5
Slitter #2
Slit with fixed gutter, gutter is 8 mm or 3/8 inch
6
Slitter #3
lit with fixed gutter, gutter is 8 mm or 3/8 inch
7
Slitter #4
Slit the other side edge of paper
8
Gauge Plate
Fixing all the slitters distance. (Standard is 85mm
and 90mm or 3.5inch and 5.5 inch )
9
Right Side Guide
Deflect paper feeding
10 Left Side Guide
Deflect paper feeding
1
1
1
2
3 4 5
6
7
8
10
9
Summary of Contents for MCC-35
Page 36: ...MCC 35 32 Chapter 6 CUTTING FORMAT 6 1 Metric Version 6 1 1 A3 90 48...
Page 37: ...MCC 35 33 6 1 2 A3 90 50...
Page 38: ...MCC 35 34 6 1 3 A3 90 54...
Page 39: ...MCC 35 35 6 1 4 SRA3 90 48...
Page 40: ...MCC 35 36 6 1 5 SRA3 90 50...
Page 41: ...MCC 35 37 6 1 6 SRA3 90 54...
Page 42: ...MCC 35 38 6 1 7 SRA3 85 210...
Page 43: ...MCC 35 39 6 1 8 SRA3 85 210 C1...
Page 44: ...MCC 35 40 6 1 9 SRA3 90 210...
Page 45: ...MCC 35 41 6 1 10 SRA3 90 210 C1...
Page 46: ...MCC 35 42 6 1 11 SRA3 A3 C1...
Page 47: ...MCC 35 43 6 1 12 SRA3 A3 C2...
Page 48: ...MCC 35 44 6 2 Imperial Version 6 2 1 DIG 3 5 2...
Page 49: ...MCC 35 45 6 2 2 DIG 3 5 5...
Page 50: ...MCC 35 46 6 2 3 DIG 3 5 8...
Page 51: ...MCC 35 47 6 2 4 DIG 5 8...