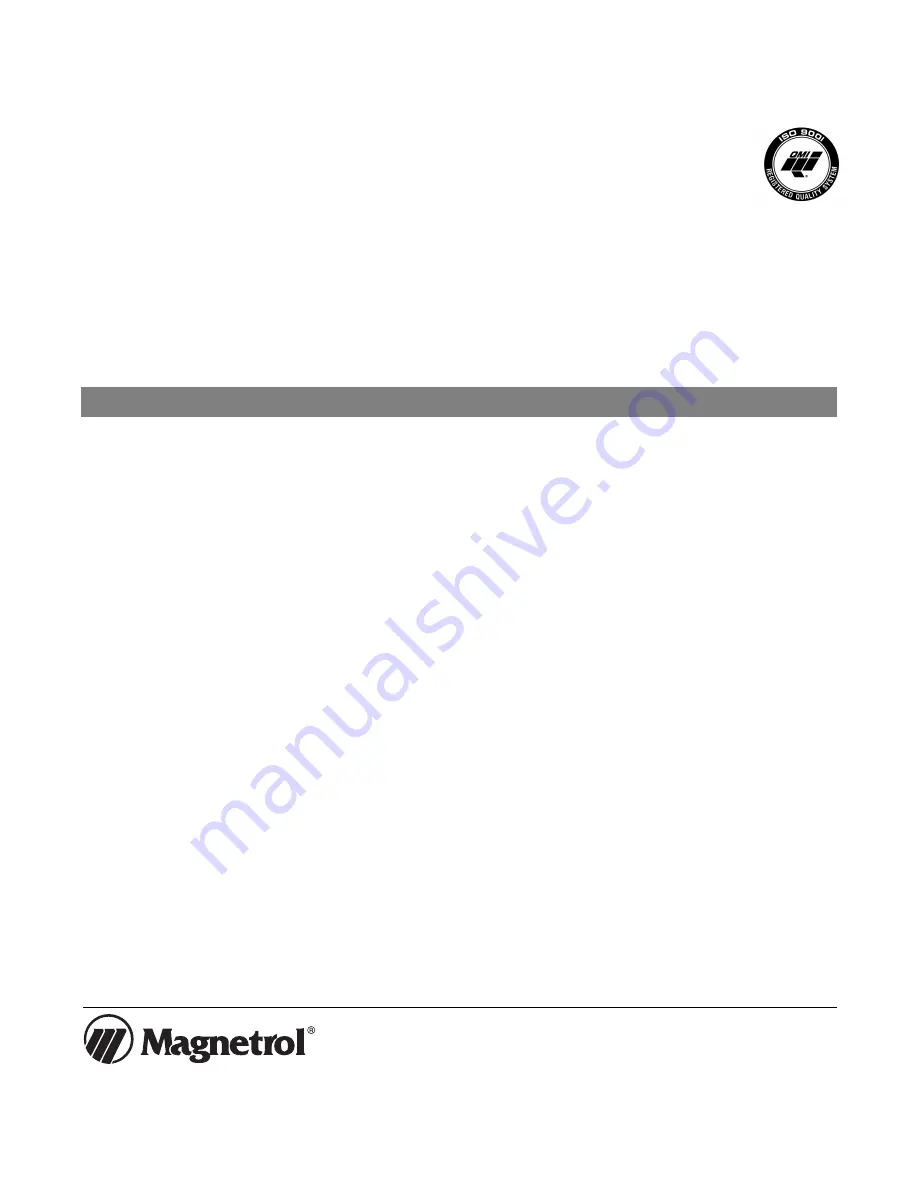
BULLETIN: 50-624.3
EFFECTIVE: November 2003
SUPERSEDES: April 1996
5300 Belmont Road • Downers Grove, Illinois 60515-4499 • 630-969-4000 • Fax 630-969-9489 • www.magnetrol.com
145 Jardin Drive, Units 1 & 2 • Concord, Ontario Canada L4K 1X7 • 905-738-9600 • Fax 905-738-1306
Heikensstraat 6 • B 9240 Zele, Belgium • 052 45.11.11 • Fax 052 45.09.93
Regent Business Ctr., Jubilee Rd. • Burgess Hill, Sussex RH15 9TL U.K. • 01444-871313 • Fax 01444-871317
Copyright © 2013 Magnetrol International, Incorporated. All rights reserved. Printed in the USA.
SERVICE POLICY
Owners of Magnetrol may request the return of a control or
any part of a control for complete rebuilding or replacement.
They will be rebuilt or replaced promptly. Controls returned
under our service policy must be returned by Prepaid trans-
portation. Magnetrol will repair or replace the control at no
cost to the purchaser (or owner) other than transportation if:
a. Returned within the warranty period; and
b. The factory inspection finds the cause of the claim to be
covered under the warranty.
If the trouble is the result of conditions beyond our control;
or, is NOT covered by the warranty, there will be charges for
labor and the parts required to rebuild or replace the equip-
ment.
In some cases it may be expedient to ship replacement
parts; or, in extreme cases a complete new control, to
replace the original equipment before it is returned. If this is
desired, notify the factory of both the model and serial num-
bers of the control to be replaced. In such cases, credit for
the materials returned will be determined on the basis of the
applicability of our warranty.
No claims for misapplication, labor, direct or consequential
damage will be allowed.
RETURN MATERIAL PROCEDURE
So that we may efficiently process any materials that are
returned, it is essential that a “Return Material Authorization”
(RMA) number be obtained from the factory, prior to the
material’s return. This is available through Magnetrol local
representative or by contacting the factory. Please supply
the following information:
1. Company Name
2. Description of Material
3. Serial Number
4. Reason for Return
5. Application
Any unit that was used in a process must be properly
cleaned in accordance with OSHA standards, before it is
returned to the factory.
A Material Safety Data Sheet (MSDS) must accompany
material that was used in any media.
All shipments returned to the factory must be by prepaid
transportation.
All replacements will be shipped F.O.B. factory.
Note:
See ESD Handling Procedure on page 5.
IMPORTANT
ASSURED QUALITY & SERVICE COST LESS
PRODUCT WARRANTY
All Magnetrol electronic and ultrasonic level and flow con-
trols are warranted free of defects in materials or workman-
ship for one full year from the date of original factory ship-
ment.
If returned within the warranty period; and, upon factory
inspection of the control, the cause of the claim is
determined to be covered under the warranty; then,
Magnetrol will repair or replace the control at no cost to the
purchaser (or owner) other than transportation.
Magnetrol shall not be liable for misapplication, labor
claims, direct or consequential damage or expense arising
from the installation or use of equipment. There are no
other warranties expressed or implied, except special
written warranties covering some Magnetrol products.
QUALITY ASSURANCE
The quality assurance system in place at
Magnetrol guarantees the highest level of
quality throughout the company. Magnetrol
is committed to providing full customer
satisfaction both in quality products and
quality service.
Magnetrol’s quality assurance system is registered to ISO
9001 and Z299.1 affirming its commitment to known
international quality standards providing the strongest
assurance of product/service quality available.