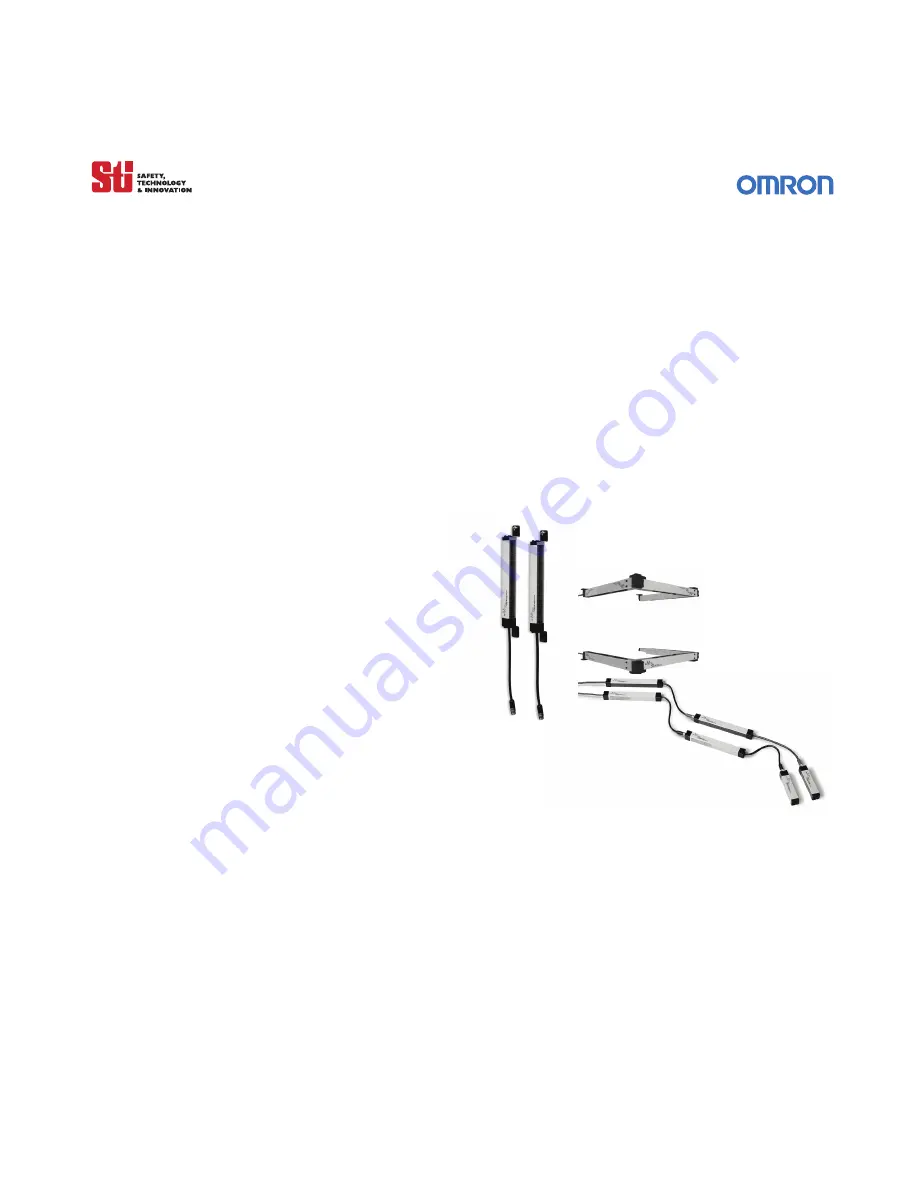
. . . . .
4700 Series
Installation and Operating Manual
for MC4700, MCF4700, MCJ4700, MS4700 & MSF4700 Series
Original Instructions
O M RO N ScientificTechnologiesInc.
Manufacturing and Sales Office
6550 Dumbarton Circle
Fremont CA 94555 USA
1 / 888 / 510-4357
Tel: 510/608-3400
Fax: 510/744-1442
www.sti.com
© OSTI 1209 PN99584-0050 Rev.E