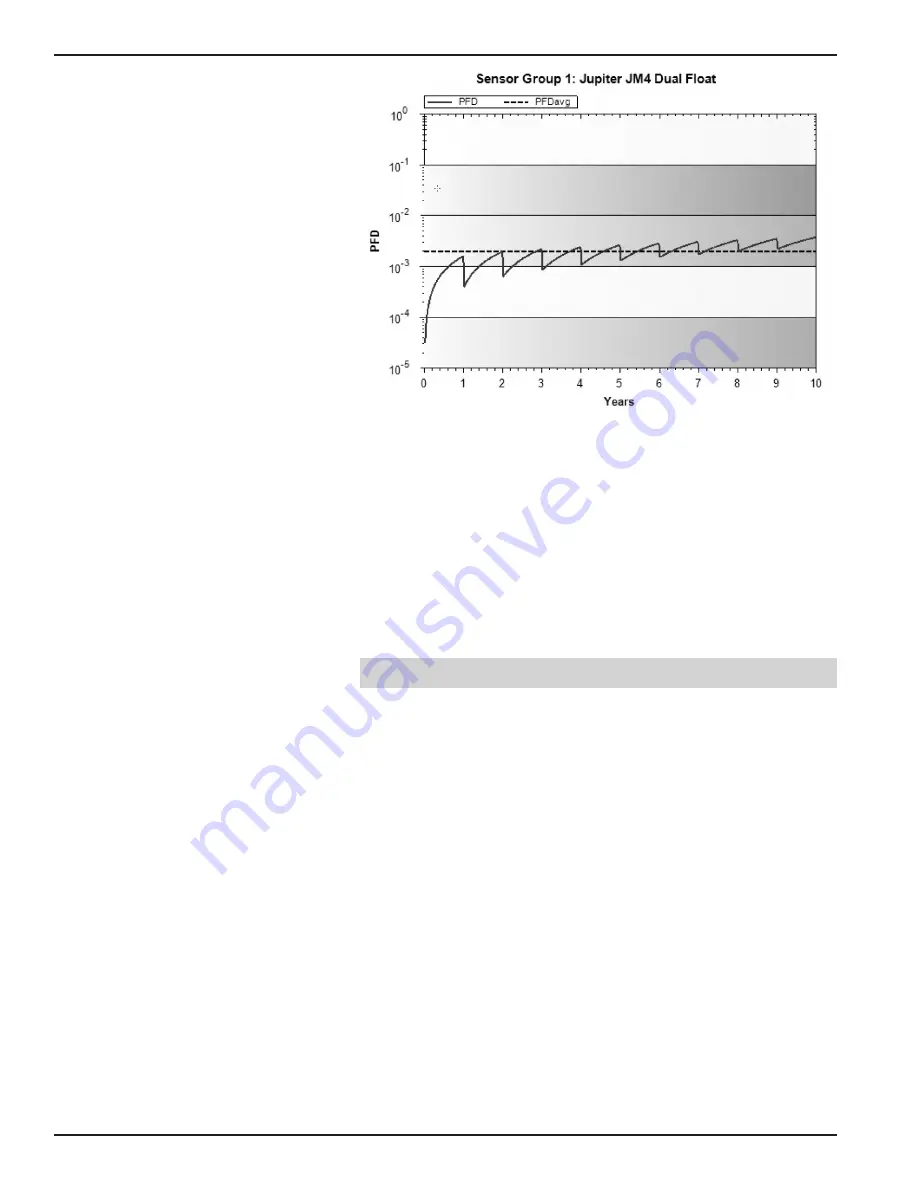
14
ORI-652 Jupiter
®
Model JM4 Magnetostrictive Transmitter – SIL Safety Manual
PFD
AVG
value for a single Model JM4-511x-xxx (two floats)
with proof test intervals of one year.
It is the responsibility of the Safety Instrumented Function designer to
perform calculations for the entire SIF.
For SIL 2 applications, the PFD
AVG
value needs to be
≥
10
-3
and
<
10
-2
.
This means that for a SIL 2 application, the PFD
AVG
for a 1-year Proof
Test Interval of the Model JM4-511x-xxx is approximately equal to
20% of the range.
These results must be considered in combination with PFD
AVG
values
of other devices of a Safety Instrumented Function (SIF) in order to
determine suitability for a specific Safety Integrity Level (SIL).
7.5
Report: Lifetime of Critical Components
According to section 7.4.9.5 of IEC 61508-2, a useful lifetime,
based on experience, should be assumed.
Although a constant failure rate is assumed by probabilistic
estimation method, this only applies provided that the useful
lifetime of components is not exceeded. Beyond their useful
lifetime the result of the probabilistic calculation method is
therefore meaningless, as the probability of failure significantly
increases with time. The useful lifetime is highly dependent on
the subsystem itself and its operating conditions.
The assumption of a constant failure rate is based on the bathtub
curve. Therefore it is obvious that the PFD
AVG
calculation is only
valid for components that have this constant domain and that
the validity of the calculation is limited to the useful lifetime of
each component.
The expected useful life of JUPITER Model JM4-511x-xxx is at
least 50 years.