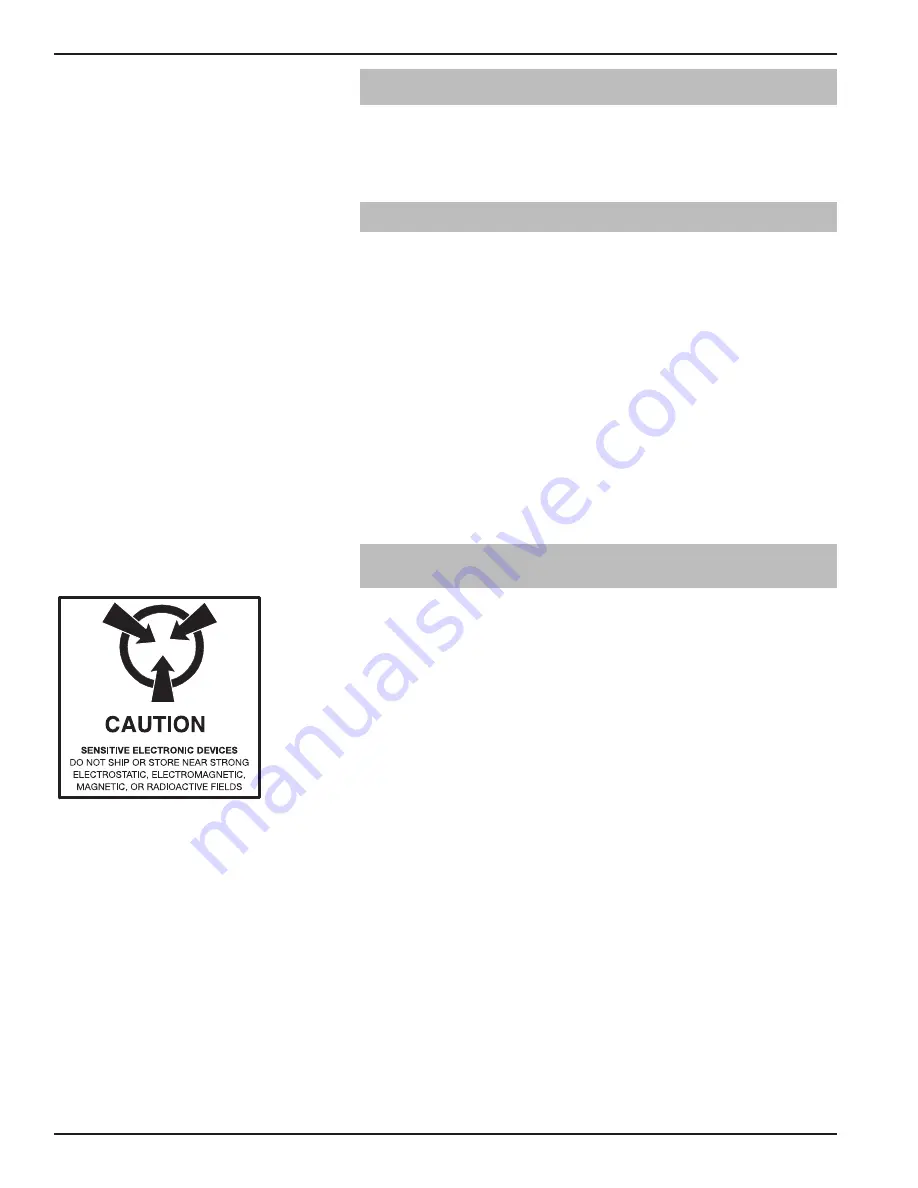
50-613 Kotron
®
Series 82 CE RF Level Transmitter
4
1.0
Complete Installation
This section provides detailed procedures for properly
installing, configuring, and, as needed, troubleshooting the
Kotron
®
Series 82 CE RF Level Transmitter.
1.1
Unpacking
Unpack the instrument carefully. Make sure all components
have been removed from the packing material. Check
all the contents against the packing slip and report any
discrepancies to the factory.
Before proceeding with the installation, do the following:
• Inspect all components for damage. Report any damage
to the carrier within 24 hours.
• Make sure the nameplate model number agrees with the
packing slip and purchase order.
• Record the model and serial numbers for future reference
when ordering parts.
1.2
Electrostatic Discharge (ESD)
Handling Procedure
Magnetrol
®
electronic instruments are manufactured to the
highest quality standards. These instruments use electronic
components that may be damaged by static electricity pre-
sent in most work environments.
The following steps are recommended to reduce the risk of
component failure due to electrostatic discharge.
• Ship and store circuit boards in anti-static bags. If an anti-
static bag is not available, wrap the board in aluminum
foil. Do not place boards on foam packing materials.
• Use a grounding wrist strap when installing and removing
circuit boards. A grounded workstation is recommended.
• Handle circuit boards only by the edges. Do not touch
components or connector pins.
• Make sure that all electrical connections are completely
made and none are partial or floating. Ground all
equipment to a good, earth ground.