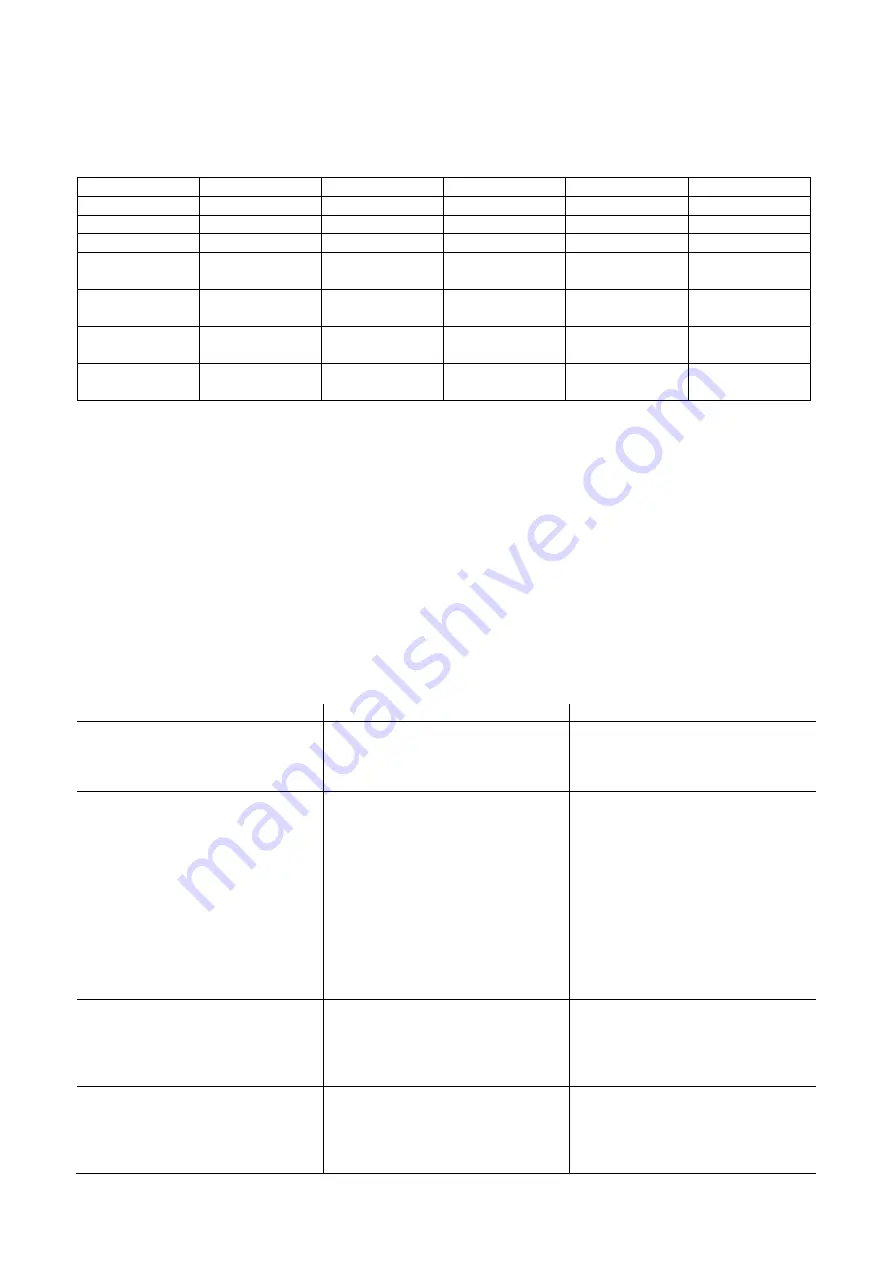
PUMP MAINTENANCE TABLE
INSPECTION
DAILY
WEEKLY
50Hrs
EVERY 500Hrs
EVERY 800Hrs
FILTERS
X
OIL
X
OIL/WATER LEAK
X
HYDRAULIC
SYSTEM
X
FIRST OIL
SUBSTITUTION
X
OIL
SUBSTITUTION
X
SEAL
SUBSTITUTION
X
14. Demolition
14.1. To allow the recycling of the raw materials, it is to separate well: pack (if supplied), the exhausted oils
and the lubricants, the electric motors, metallic pieces, parts and components in plastics.
14.2. It is compulsory to respect the norms in force related to the production, detention, harvest and disposal
of the refusals, according to what established by the legislative decree 22/97. The exhausted oils must be
delivered to the National Consortium Obligatory, while possible packing must be digested according to what
established by the title II of the legislative decree 22/97.
14.3. ATTENTION: MAER IDROPULITRICI society does not assume any responsibility for damages to
things, personal or animals, consequential and consequent to the re-use of the single parts or the single
components of the machine for function or situation of the assemblage different from the original for which
the high pressure cleaner has been conceived. Finally, when demolished, it is to destroy well the nameplate
of identification together to every other document related to the same machine.
15. Problems during the operation
Problem
Cause
Solution
The inlet hoses vibrate
Foreign piece in a valve
Air suction.
Disassemble the valve and
remove the foreign piece
Identify the source of the air
suction and eliminate it
The water does not reach the
lance although the pump is
working.
Missing water in the net.
Air inside the water circuit.
The lance nozzle is blocked.
The pump intake valve is
blocked.
The detergent intake tap is
open with empty detergent
tank.
The detergent feeder hose is
faulty.
Verify the connection with the
water supply and let the water
come in.
Bleed the circuit.
Remove and clean the nozzle.
Unscrew
the
valve
and
unblock it.
Close the tap and fill the
detergent tank.
Replace the detergent feeder
hose.
The pressure at the lance is weak
although the pump is under high
pressure.
The lance nozzle is blocked.
The pressure valve is dirty.
There is lime scale encrusted
inside
the
pressure
adjustment valve.
Remove and clean the nozzle.
Remove and clean the valve.
Remove the valve, clean it
and scale it carefully.
The motor does not switch on.
The fuses have burnt
The switch is disconnected.
The by-pass valve does not
gives electric signal to the
electronic board.
Change the fuses.
Rearm the switch.
Check the microswitch on the
valve.