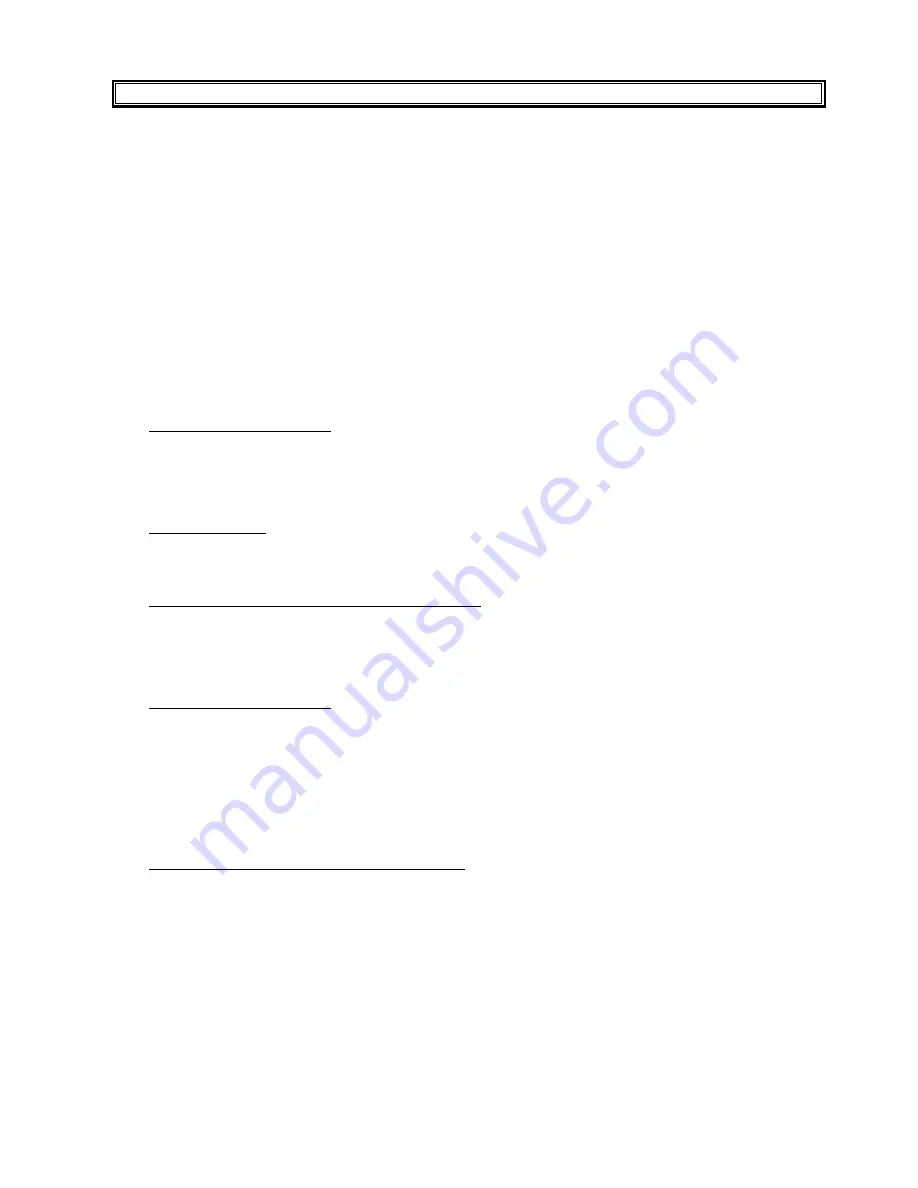
Pag.70
27/03/2014
RECOMMENDATIONS FOR A CORRECT PREVENTIVE MAINTENANCE
The aim of this schedule is to prevent as far as possible equipment from breaking down, through the periodical check-up
and replacement of components subject to fair wear and tear, thus reducing service calls and relevant cost in working hours.
This schedule is based on the suppliers recommendations along with previous service history on equipment currently out in
the field.
It is designed to assist in extending the operational life of the equipment.
A. Pre delivery inspection:
We suggest to carry out a Pre Delivery Inspection on all machines before deliver them to final customer. PDI can detect
inconveniences which may occur during transportation or a long storage. For instance:
-
screws and nuts which fit the body-work may become loose;
-
flowmeter may be block by dust especially after long storage;
-
screws which fit the power supply wires may become loose.
B. 2 or 3 weeks after installation:
Parts to be checked or adjusted:
1.
the grinder/s settings
2.
the dose settings
3.
if daily cleaning of group and milk frother is carried out by the operator.
C. At 4 months’ intervals:
Parts to be changed:
1.
o-rings for milk frother
2.
milk silicone tube for milk frother
3.
o-rings for group pistons.
4.
Internal Mixer gasket
Parts to be cleaned or replaced (check and decide on site):
5.
o-rings for the drip tray
6.
group upper piston micro screen
7.
group lower piston screen
8.
milk frother
9.
clean the hopper by the oil of the coffee
10. clean the coffee chute by means of a dry brush
Parts to be checked or adjusted:
11. grinder/s setting (coarseness of the coffee powder)
12. air adjustment for milk frother
13. coffee silicone tube
14. pump pressure should be 8-9 bars for rotation pump and 11 bars for vibration pump, check after had closed the
coffee flow valve on upper piston or use the dedicated tool, code no. A 0128
15. coffee boiler expansion valve should leak at 13 bars after a few coffee deliveries
16. front door switch
17. grounds beans tray induction switch
18. check the gasket underneath the sweeper (it is glued to the sweeper)
Check the functioning of the machine with the customer:
19. dose settings (setting of milk frother, steam boiler pressure…)
20. that the double coffee spout delivers consistent quantity of coffee in the cup, if not replace it
21. check how many times the group cleaning procedure has been carried out
22. check how many times the milk frother cleaning procedure has been carried out.
Summary of Contents for ILC-200
Page 18: ...Pag 18 27 03 2014 INFO RESET A1 READ DOSES DATA Doses counter A B esc...
Page 19: ...Pag 19 27 03 2014 A2 READ DOSES DATA Reset doses counter A B...
Page 20: ...Pag 20 27 03 2014 B INFO RESET SYSTEM DATA...
Page 29: ...Pag 29 27 03 2014...
Page 33: ...Pag 33 27 03 2014...
Page 36: ...lb 05061 02 EN Pag 36 27 03 2014...
Page 39: ...Pag 39 27 03 2014 DISPLAY REGULATION...
Page 42: ...Pag 42 27 03 2014...
Page 43: ...Pag 43 27 03 2014...
Page 44: ...Pag 44 27 03 2014...
Page 46: ...Pag 46 27 03 2014...
Page 50: ...lb 05061 02 EN Pag 50 27 03 2014 1 1 3 3 5 5 7 7 2 2 4 6 4 6 esc esc V esc...
Page 59: ...Pag 59 27 03 2014...