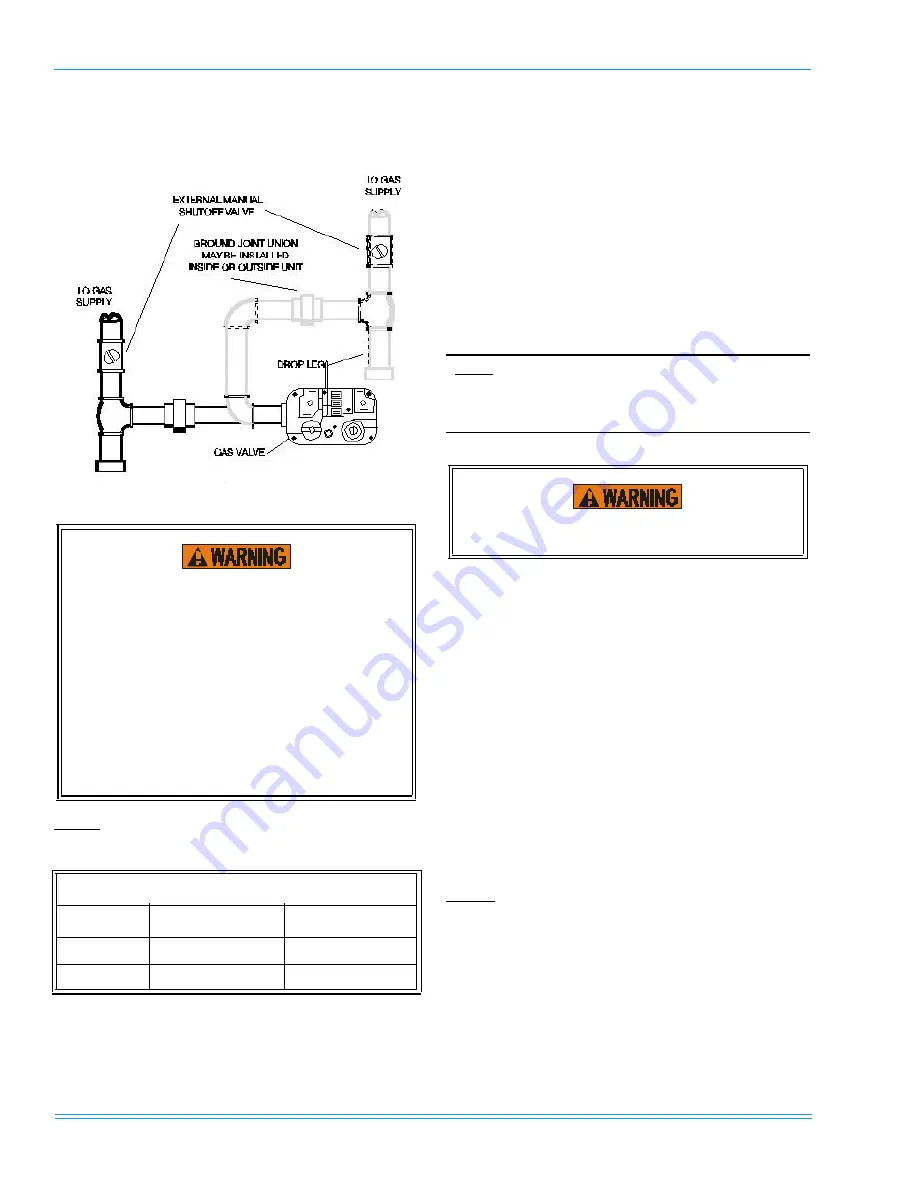
035-14527-000 REV A (599)
Form 650.77-N3U
14
Unitary Products Group
nections to the unit. Installation of a drop leg and ground
union is required. (Refer to Figure 10 on page14)
NOTE:
a 1/8” NPT plug is included in the inlet side of the gas
valve for measuring incoming gas pressure.
ELECTRICAL POWER CONNECTION
Field wiring to the unit must conform to and be grounded in
accordance with the provisions of the National Electrical
Code ANSI/NFPA No. 70 - latest edition, Canadian Electric
Code C22.1 Part 1 - (latest edition) and/or local codes. Elec-
trical wires which are field installed shall conform with the
temperature limitation for 63°F/35°C rise wire when installed
in accordance with instructions. Specific electrical data is
given on the furnace rating plate.
Provide a power supply separate from all other circuits. Install
overcurrent protection and disconnect switch per local/
national electrical codes. The switch should be reasonably
close to the unit for convenience in servicing. With the dis-
connect switch in the OFF position, check all wiring against
the unit wiring label. Also, see the wiring diagram in this
instruction.
.
Connect the power supply as shown on the unit wiring label
on the inside of the blower compartment door and Figures 11
& 12. The black furnace lead must be connected to the L1
(hot) wire from the power supply.
The white furnace lead must be connected to neutral. Also,
the green equipment ground wire must be connected to the
power supply ground.
Remove the screw retaining the wiring box. Route the power
wiring through the unit side panel with a conduit connector or
other proper connection. Make wiring connections as shown
in Figure 11 or 12. Replace the wiring box and screw.
An alternate wiring method is to use a field provided 2 x 4 box
and cover on the outside of the furnace. Route the furnace
leads into the box using a protective bushing where the wires
pass through the furnace panel.
NOTE :
The power connection leads and wiring box on
upflow units may be relocated to the left side of the furnace.
Remove the screws and cut wire tie holding excess wiring.
Reposition on the left side of the furnace and fasten using
holes provided.
ELECTRICAL CONTROL CONNECTIONS
Install the field-supplied thermostat. The thermostat instruc-
tions for wiring are packed with the thermostat. With the ther-
mostat set in the OFF position and the main electrical source
FIGURE 10 : GAS PIPING
Compounds used on threaded joints of gas piping
must be resistant to the action of liquefied petro-
leum gases.
After all gas piping connections are completed,
leak test all joints, fittings and furnace connections
with rich soap and water solution, commercial
available bubble type leak detection fluid, or other
approved means.
Do not use an open flame or other source of igni-
tion for leak testing.
INLET GAS PRESSURE RANGE
NATURAL GAS
PROPANE (LP)
Minimum
4.5 In. W.C.
11 In. W.C.
Maximum
13.8 In. W.C.
13.8 In. W.C.
Note:
The furnace’s control system depends on correct
polarity of the power supply and a proper ground connec-
tion. Refer to the furnace control diagnostics section for
symptoms of reversed power supply polarity
Use copper conductors only.