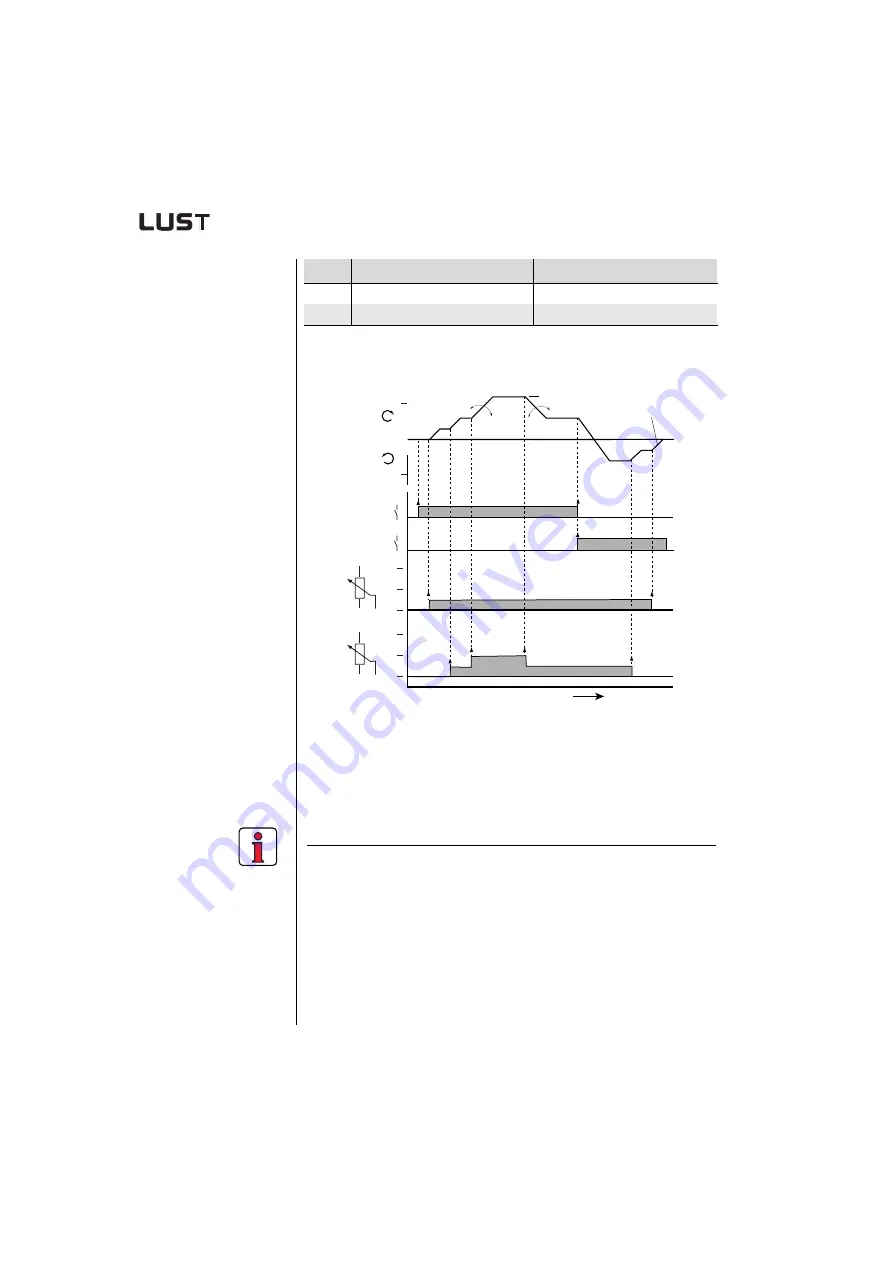
4-10
CDA3000 Operation Manual
4 Commissioning
Input signals
Figure 4.4 Example of a driving profile for two directions with correction
reference (R2), 152-ASTER = ROT_2
FOR setting
FOR is preset, and requires no further optimization for standard
applications.
Note:
For more detailed information on optimizing
•
the speed control loop
refer to the CDA3000 Application Manual.
6
Brake drive by opening start contact. Drive brakes down to standstill.
7
Open ENPO contact.
Safely disables power stage.
Commissioning is completed.
Step
Action
Note
t [ms]
0
0
1
10 V
FMAX
5 V
R1
0 V
f [Hz]
STL
0
1
STR
10 V
5 V
R2
0 V
FMAX
303-FMAX1
592-DECR1
590-ACCR1
594-STPR1