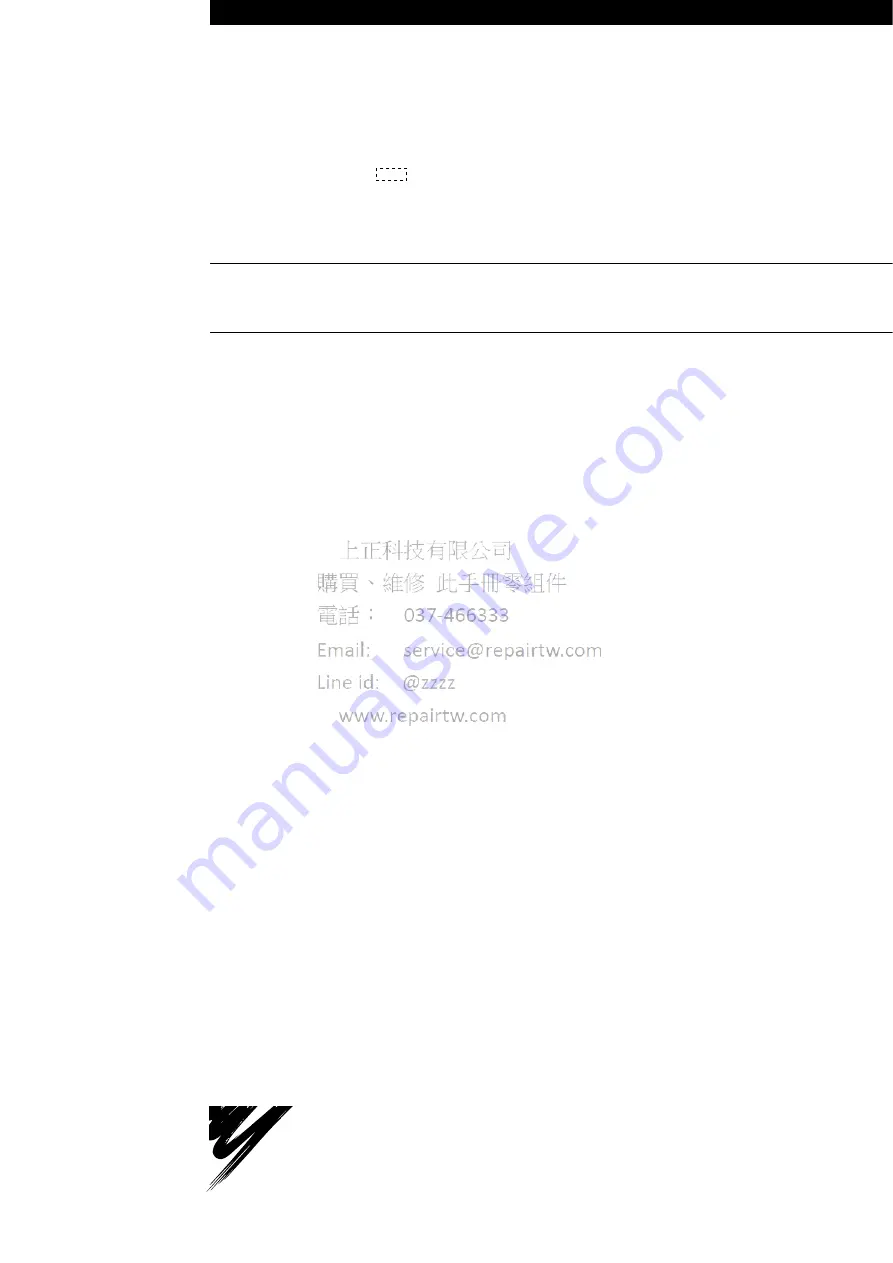
YASKAWA
VARISPEED-686SS5
INSTRUCTION MANUAL
YASKAWA
MANUAL NO. TOE-S686-15B
SUPER-ENERGY SAVING VARIABLE SPEED DRIVE (VS-686SS5)
MODEL: CIMR-SSA
Upon receipt of the product and prior to initial operation, read these instructions
thoroughly, and retain for future reference.
200V CLASS 0.4 to 75kW (1.2 to 110kVA)
400V CLASS 0.4 to 300kW (1.4 to 460kVA)
REFERENCE
VARISPEED-686SS5 DESCRIPTIVE MANUAL FOR CONSTANTS (TOE-S686-15.2)