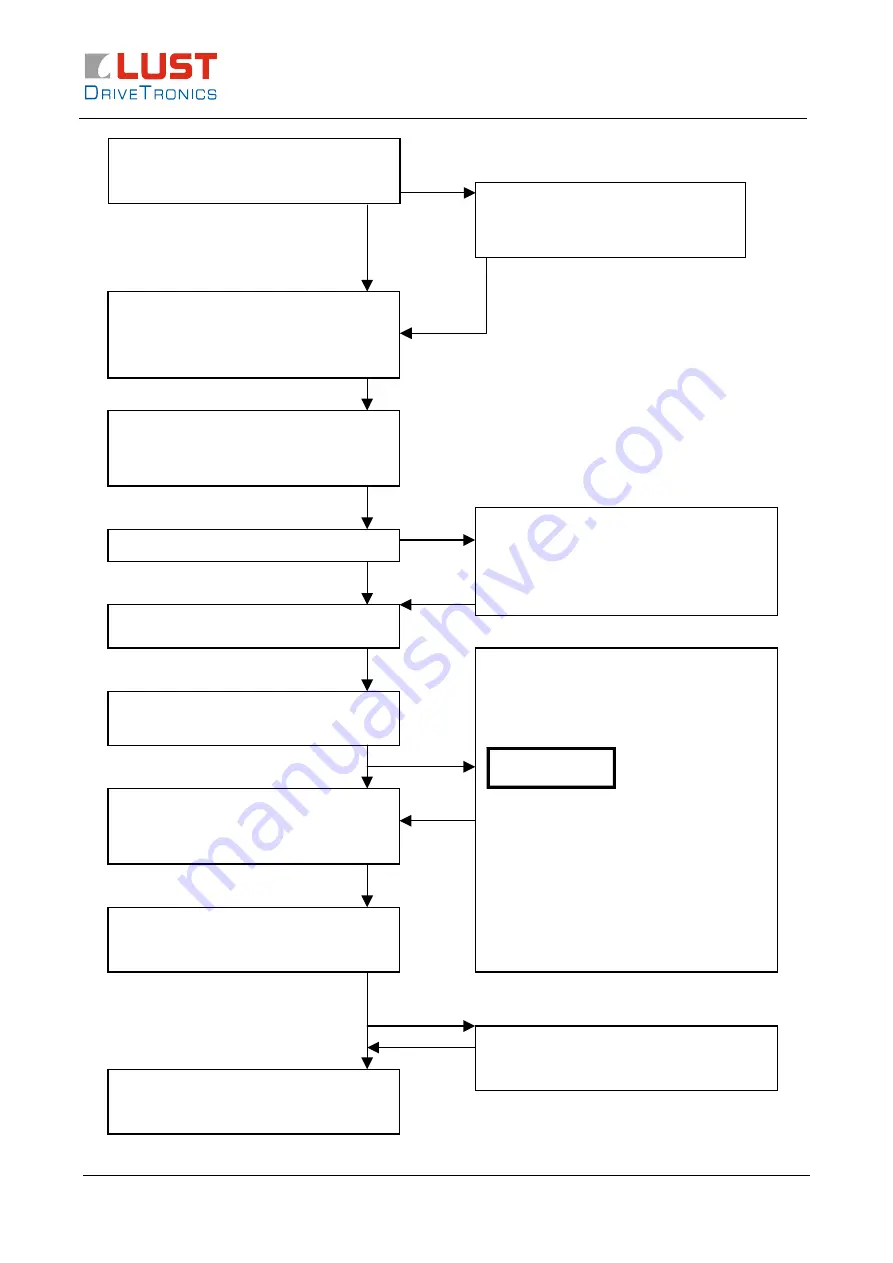
Servomotoren / Servomotors
Baugröße/Size 2 (
□
145 ) F.P 12 – 32L
Baugröße/Size 3 (
□
190 ) F.P 13 – 43L
Nr./No. 680-01975
27
5.1.4.5
Carefully remove drive end shield (A; 10)
with rotor (2) from stator (1).
5.1.5.1
Push disassembly tool into the terminal box
(43) and detach the insulator with turn and
light pressure. Pull the insulator apart and
remove the contact pins.
5.1.5.2
Mark resolver (4) to non-drive end bearing
shield (B; 11), loosen screws (7,22) and
remove resolver stator (4).
5.1.6
Remove fitting key (41).
5.1.7
Remove outer circlip (46).
5.1.8
Loosen screw (21).
5.1.10
Remove drive end shield (A; 10) with drive
end bearing (A; 52) from armature (2) with
an extraction tool.
5.1.11
Remove drive end bearing (A; 52) from drive
end shield (A; 10).
Type with brake
5.1.9
Separate brake coil carrier (60a) and brake
armature (60b) by applying 24V d.c.
Caution!
When the brake winding is disconnected,
the brake armature (60b) immediately
moves against the brake coil carrier (60a).
If the armature (2) is to be turned or the
brake armature (60b) removed, 24V d.c.
must be applied to the brake winding.
Separation of the brake armature (60b)
and brake coil carrier (60a) by force will
result in deformation of the diaphragm at
the brake armature (60b).
5.1.13
Remove non-drive end bearing (B; 53) from
armature (2) with an extraction tool.
Type with brake
5.1.12
Remove brake coil carrier (60a).
Type with brake
5.1.4.5
Carefully remove brake connecting cable
from stator (1).
Type with oil-tight drive end shield
(A)
5.1.7
Before removing the outer circlips (46) and
(47), sealing ring (80) must be removed by
destruction.
Only refers to a faulty brake coil carrier
Disassembly steps 5.1.5.1 to
5.1.5.2 only refer to a faulty
resolver stator (4); otherwise
continue with 5.1.6.