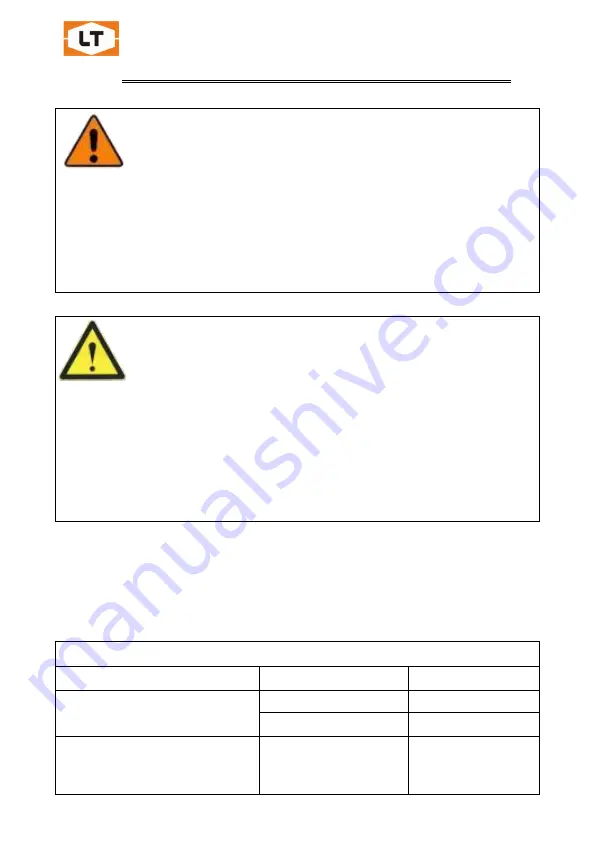
Zhengzhou Linghang Robot Co.,Ltd.
29 / 42
5.
Regular Maintenance
Warning: All energy connections (e.g. electrical, air, water, etc.) are
turned off unless the tool is supported or placed in the tool holder,
Otherwise maintain or repair the tool or module is not allowed.
Release pressure and turn off power according to customer specific
safety specifications and policies. If no tools are placed and the circuit is po'wered
on, personal injury or device damage may occur. Before performing maintenance
or repair on the tool quick-change unit or module, place the tool in the tool holder,
close and discharge all energized circuits, clear all pressurized connections, and
verify that all circuits are powered off.
Note: the cleanliness of the working environment seriously affects
the trouble-free operation of the tool quick-change device. The dirtier
the environment, the greater the need for debris protection. You may
need to protect the entire end gripper tool, master disk, tool disk, and
all modules.
Protective measures include:
•Tools should be placed awayfro~m the chip generator.
•Tool holder mounting cover.
•Shields, deflectors, air curtains and similar devices mounted on end gripper tools
and tool brackets.
5.1 Maintain the checklist regularly
The following table provides a visual inspection and regular maintenance
plan. For detailed periodic maintenance steps for all utility modules pls check the
modules section.
Maintain checklist
Application program
Tool change frequency
Survey schedule
Normal application
<1 min
per week
>1 min
per month
Welding/servo/deburring,casting
operation (dirty environment)
all
per week