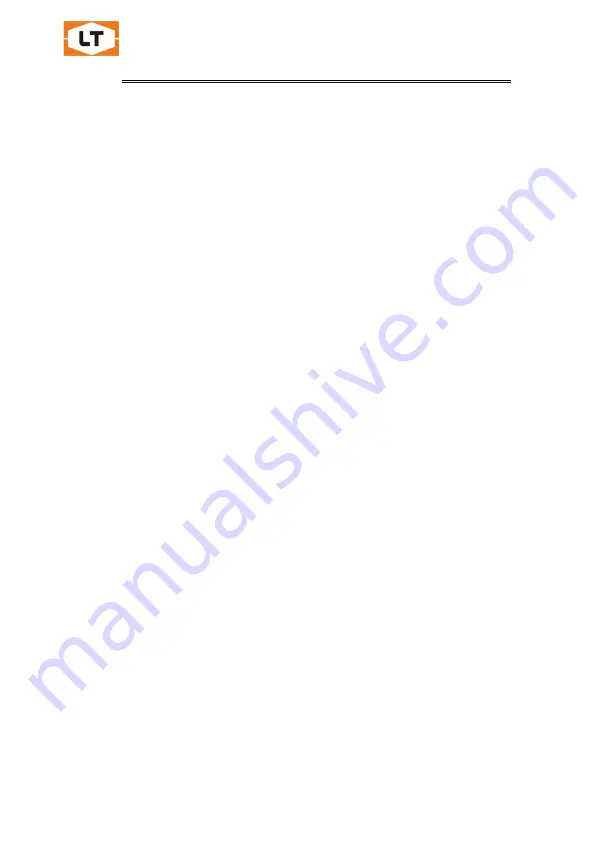
Zhengzhou Linghang Robot Co.,Ltd.
28 / 42
When the User provides the tool holder, a fixed, repeatable, horizontal, stable
place to facilitate the lifting of the tool is necessary. The tool holder must support
the weight of the tools, tool plates, tool transition flanges, optional modules, cables,
hoses, and other necessary components. The offset cannot exceed the specified
data.
Ideally, the tools should be suspended vertically from the tool holder so that
gravity can help separate the tool plate from the master plate during unlocking. A
tool holder also can be designed to hold the tool in a horizontal position, but the
necessary compliance must be provided during locking and unlocking. In general,
horizontal tool holder will cause more abrasion to the locking mechanism and
positioning characteristics of the tool holder.
The tool can be placed on the tool holder in a variety of ways. A common
method is to use tapered locator pins and bushings. Robot programming and
position repeatability are critical to tool picking and dropping.
It is recommended to use sensors to detect the presence of tools in the tool
holder. Sensors can be used priorto locking to ensure that tools are properly
placed in the bracket. Sensors can also be used when the robot disconnects and
starts to move away. If the tool gets stuck on a stand or cannot be released from
the robot, the sensor provides a safety measure.
The position close to the sensor should be as vertical as possible to prevent
metal shavings, weld splashes or other debris from landing on the sensor and
producing false readings.
A chip guard on the tool stand can cover tools and modules to protect them
from dirty conditions such as grinding or welding. Alternatively, position the tool
in an area free from weld splashes, liquids, adhesives, or other debris so that a
debris shield is not required anymore.