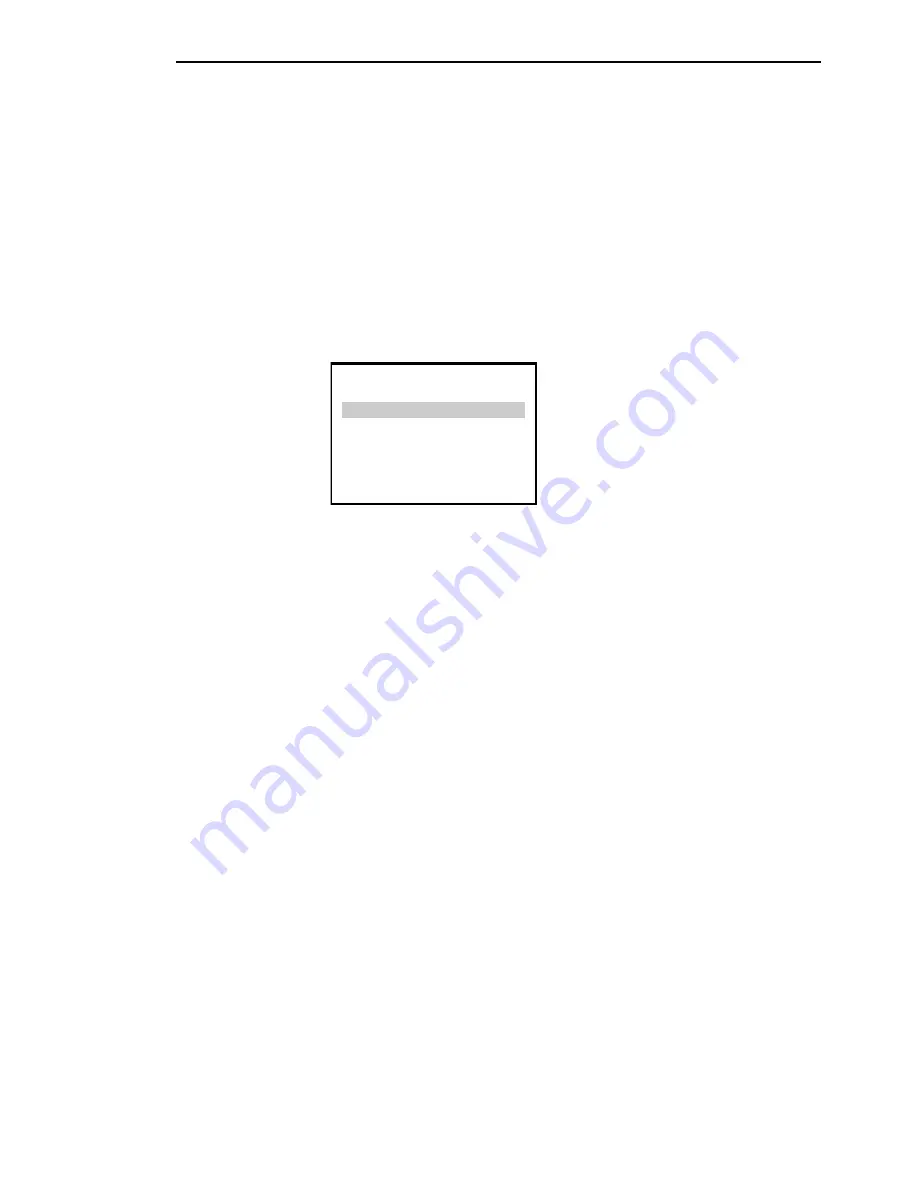
Page 42 of 72
If view mode is requested the message “View access granted” will be displayed.
If calibration mode is required the operator must enter a PIN and then press the OK button. If
the PIN is correct and the controller enters calibration mode then the message “Cal access
granted” will be displayed. An incorrect PIN will result in the message “Incorrect Password
View access granted” being displayed.
When in calibration or view mode, the function code screen (Diagram 8) is used to select the
desired function. The Up/Down data entry buttons or the numeric buttons can be used to scroll
through the function codes. Pressing the Cancel button returns the operator to the main menu.
By pressing the OK button the display enters the selected function.
Function code
00 Exit Calibration
01 View Active Winch
02 Cal. Active Winch
03 Not Used
04 Not Used
05 Not Used
Diagram 8: Function code screen
7.1.3
General information regarding text editing
Function codes that require editing will have a blinking cursor indicating where the edit will
take place. The numeric buttons are used to enter the new value (unless stated otherwise). The
OK button should be pressed when the edit is complete to accept the new value. Pressing the
cancel button aborts the edit and any changes made are discarded.
The “. / -“ button can be used to enter a decimal point or a negative value. If a negative
number needs to be entered the “. / -“ button should be pressed before any numeric buttons.
Pressing the “. / -“ button again before any other numeric button are pressed, results in the “ -
“ being removed. If a number contains only a fractional part (ie. 0.123 ) the operator needs to
press the button “0” before the “. / -“ button otherwise a “-“ will be displayed.
7.2
Calibration Functions Breakdown
7.2.1
EXIT CALIBRATION item
Returns the operator to the main menu.
File : 1550-Telescopic-HRT.DOC
Issue Date: - 01/08/05
Summary of Contents for RCI-1550 HRT
Page 2: ......
Page 6: ......
Page 16: ...Page 13 of 72 File 1550 Telescopic HRT DOC Issue Date 01 08 05 ...
Page 76: ......
Page 78: ......
Page 79: ......
Page 80: ......
Page 81: ......
Page 82: ......
Page 83: ...APPROVED BY TOL 0 0 0 1 2 3 4 55 26 2 0 7 2 8 9 1 1 1 1 0 7 5 6 2 ...
Page 84: ... APPROVED BY 0 1 2 22 3 3 3 TOL 4 4 23 4 232 22 3 242 4 2 32 2 3516 7 8 7 7 9 2 3 42 4 2 ...
Page 85: ... APPROVED BY 0 1 2 22 3 3 3 TOL 4 4 23 4 232 22 5 0 42 4 2 3617 8 9 8 8 2 ...
Page 87: ...APPROVED BY TOL 0 0 0 1 22 3 4 5 6 0 22 2 1 7 8 98 1 7 8 98 7 8 98 7 8 98 1 0 9 8 3 6 8 3 ...
Page 88: ......
Page 89: ......
Page 90: ......
Page 91: ......
Page 92: ......
Page 93: ......
Page 94: ......
Page 95: ......
Page 96: ......
Page 97: ......
Page 98: ......
Page 99: ......
Page 100: ......
Page 101: ......
Page 102: ......
Page 103: ......
Page 104: ......
Page 106: ......
Page 107: ......
Page 108: ......
Page 109: ......
Page 110: ......
Page 111: ......
Page 112: ......
Page 113: ......
Page 114: ......
Page 115: ......
Page 116: ......
Page 118: ......
Page 119: ......
Page 120: ......
Page 121: ......
Page 122: ......
Page 123: ......
Page 124: ......
Page 125: ......
Page 126: ......