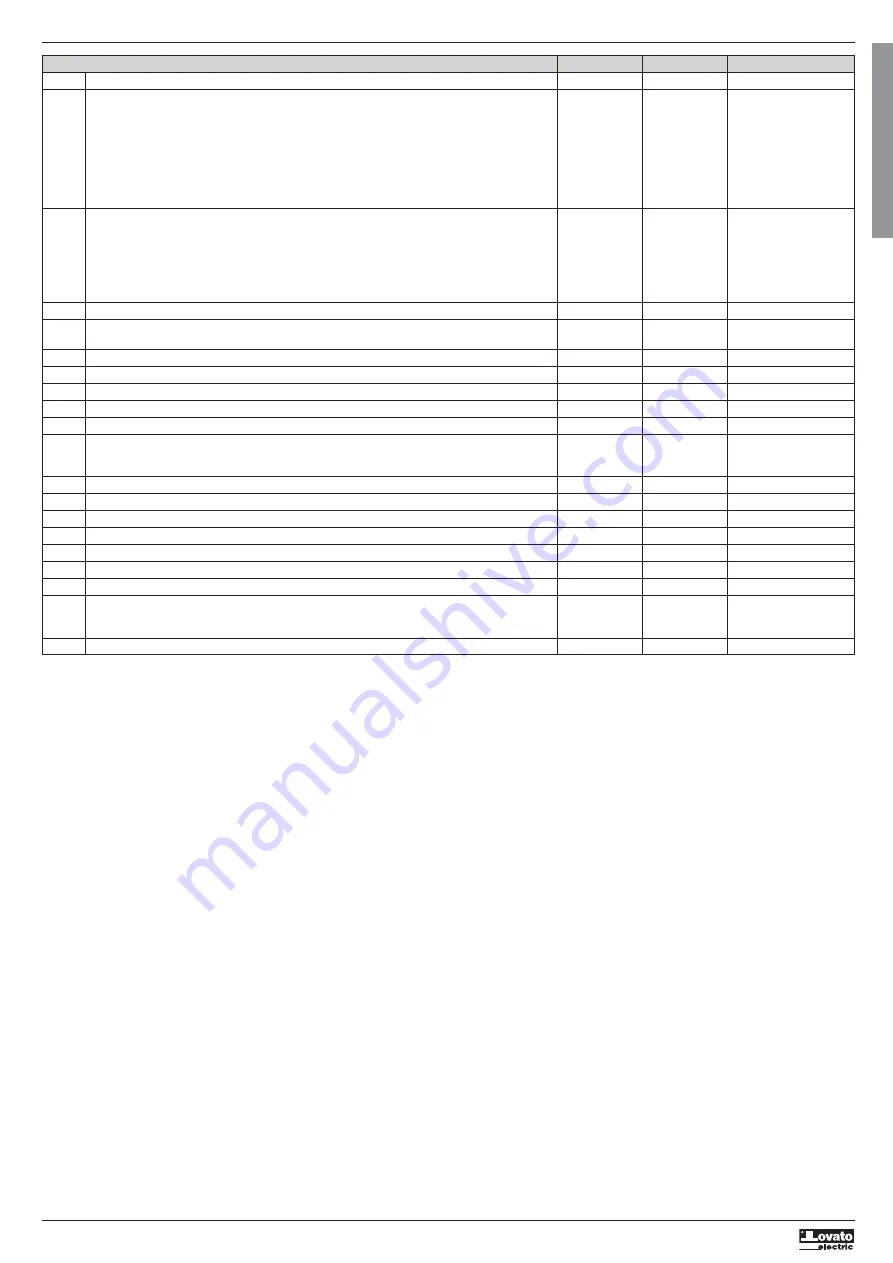
I456
GB
CS
01
18
12
G
B
P04 – PROTECTIONS UoM Default Range
P04.01
Thermal motor protections enable ON OFF / ON
P04.02
Starting thermal protection class 10 2
10A
10
15
20
25
30
35
40
P04.03
Run thermal protection class 10 2
10A
10
15
20
25
30
P04.04
Motor thermal protection reset % 120 0…140
P04.05
IN3 input type Digital DIGITAL
PTC
P04.06
Number of automatic alarm reset attempts OFF OFF / 1…6
P04.07
Automatic alarm reset interval min 1 1…30
P04.08
Minimum torque threshold (load too low) %Tn OFF OFF / 20…100
P04.09
Minimum torque trip delay sec 10 1…20
P04.10
Maximum starting time sec OFF OFF / 10…1000
P04.11
Phase sequence control OFF OFF
L1-L2-L3
L3-L2-L1
P04.12
Minimum voltage threshold V OFF OFF / 170…760
P04.13
Minimum voltage trip delay sec 5 0…600
P04.14
Maximum voltage threshold V OFF 170…760 / OFF
P04.15
Maximum voltage trip delay sec 5 0…600
P04.16
Current asymmetry % OFF OFF / 1…25
P04.17
Current asymmetry delay sec 5 0…600
P04.18
Maintenance interval h OFF OFF / 1…50000
P04.19
Alarm reset mode STOP STOP
START
STA-STO
P04.20
Start after power off sec 10 0...900
P04.01
– General enabling of thermal protections set with parameters P04.02 and P04.03. If this parameter is set to OFF (for example, for starting multiple motors with a single starter) both protections will be
disabled.
P04.02 – P04.03
– Define the motor electronic thermal protection class, for the starting and run phases respectively. The thermal protection class is set in relation to the type of use of the motor. Class 10 is adapted
to normal use, classes 15, 20 etc. for heavier duty use. If the motor has a heavy duty application, for more effective protection you can set the starting protection class higher than the run protection class.
P04.04
– Determines the value of the thermal status beneath which the motor thermal protection alarm is reset.
P04.05
– Defines whether terminal IN3 is used as a digital input or as PTC sensor input.
P04.06
– This function is used in unsupervised applications with 2-wire motor starting command. If the motor is stopped by an alarm with ‘Automatic reset’ enabled, after a time defined in P04.07 the alarm resets
and hence the motor starts again. If after the reset the motor does not restart, a number of motor reset and restarting attempts are made as set. During the alarm status, the display alternates the active
alarm and the time remaining to the automatic reset.
P04.07
– Delay between successive automatic reset attempts.
P04.08
– Normally used as protection against pumps dry running or to detect failure of transmission chains or belts. When the torque is lower than this setting, after the delay set in P04.09 the alarm A09 Load too
low is generated. The trip delay is reset if the torque returns to a value of 10% higher than the setting.
P04.09
– Load too low alarm trip delay.
P04.10
– Checks that the motor starting process does not exceed the set time, i.e. that the mechanical assemblies have not been modified (due to wear or failure) in such a way that prevents the machine from
starting properly. A starting time longer than this setting cause the alarm A10 Starting time too long.
P04.11
– Enables control of the power phase sequence, i.e. the direction of rotation of the motor. Setting L1-L2-L3 corresponds to forwards rotation, L3-L2-L1 to reverse. If the soft starter detects a phase sequence
different thant the set one, it generates the alarm A03 Incorrect phase sequence.
P04.12 – P04.13
– A voltage lower than P04.12 for a time longer than the time set on P04.13 generates the alarm A19 Line voltage too low.
P04.14 – P04.15
– A voltage higher than P04.14 for a time longer than the time set on P04.15 generates the alarm A20 Line voltage too high.
P04.16 – P04.17
– Controls the current asymmetry during full voltage running. Asymmetry greater than the setting P04.16 for a time longer than P04.17 generates the alarm A06 Current asymmetry.
P04.18
– Generates alarm A22 Maintenance request when the motor exceeds the set number of hours of operation. This can be reset with the command C01 Reset maintenance counter which simultaneously restores
the hour meter.
P04.19
– Defines the source of the alarms reset command.
STOP
= The alarms are reset when the STOP input opens.
START
= The alarms are reset when the START input closes.
STA-STO
= Both of the above.
P04.20
– It defines a delay of the start following a power down of the auxiliary voltage: when the auxiliary voltage comes back, if the START contact is already closed, the soft starter doesn’t restart the motor
immediately but only after the time specified in the parameter P04.20. During this time on the display appears the alarm A05 Auxiliary power failure. This parameter is available from firmware revision >=2.