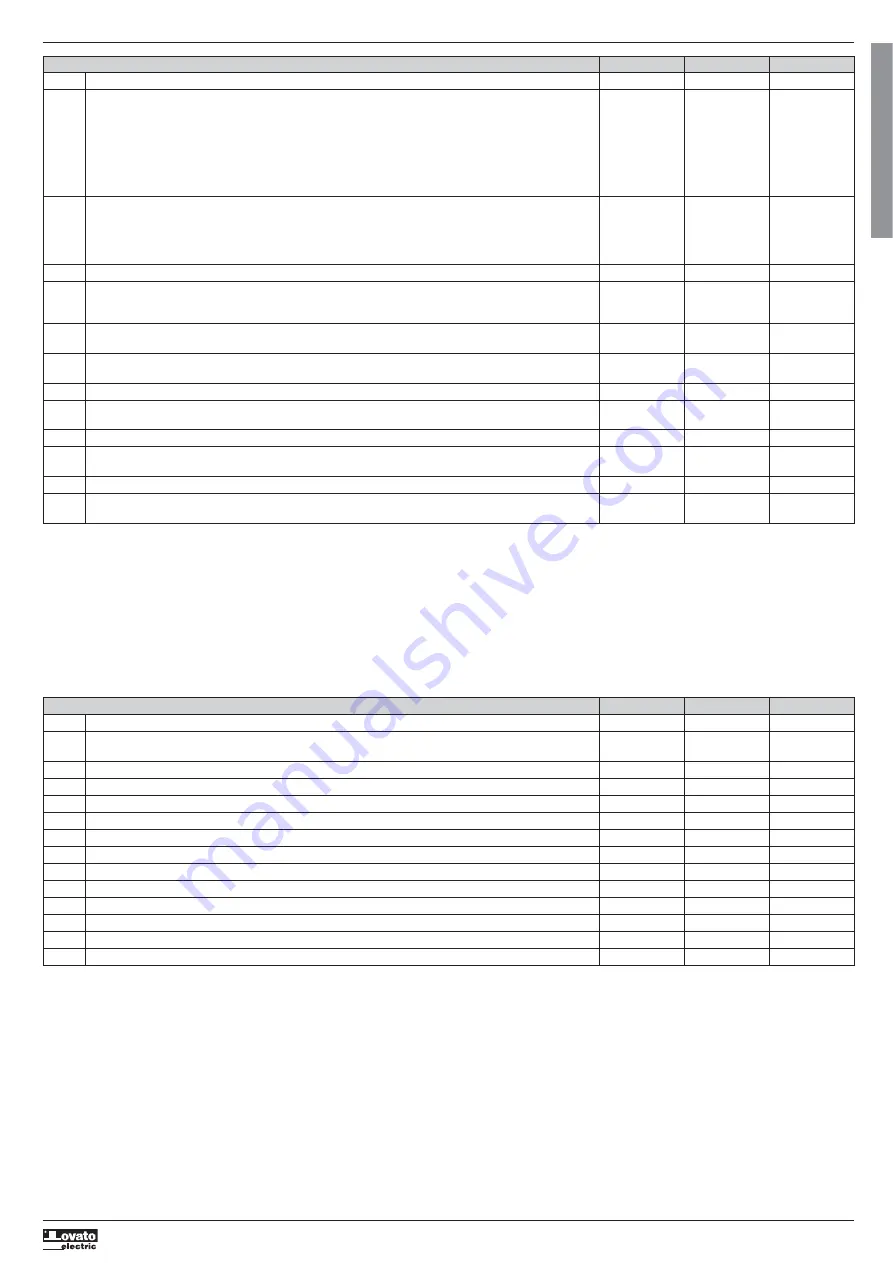
I564 GB I 02 19
15
M16 – COMMUNICATION (COMn, n=1…2) UoM Default Range
P16.n.01 Node serial address 01 01-255
P16.n.02 Serial port speed bps 9600 1200
2400
4800
9600
19200
38400
57600
115200
P16.n.03 Data format 8 bit – n 8 bit - no parity (n)
8 bit, odd
8 bit, even
7 bit, odd
7 bit, even
P16.n.04 Stop bits 1 1-2
P16.n.05 Protocol Modbus RTU Modbus RTU
Modbus ASCII
Modbus TCP
P16.n.06 IP address 192.168.1.1 000.000.000.000 –
255.255.255.255
P16.n.07 Subnet mask 255.255.255.0 000.000.000.000 –
255.255.255.255
P16.n.08 IP port 1001 0-9999
P16.n.09 Channel function Slave Slave / Gateway
Mirror / Master
P16.n.10 Client / server Server Client / Server
P16.n.11 Remote IP address 000.000.000.000 000.000.000.000 –
255.255.255.255
P16.n.12 Remote IP port 1001 0-9999
P16.n.13 IP gateway address 000.000.000.000 000.000.000.000 –
255.255.255.255
Note: This menu is divided into 2 sections for communication channels COM1...2.
The front IR communication port has fixed communication parameters, so no setup is required.
P16.n.01
– Serial (node) address of the communication protocol.
P16.n.02
– Communication port transmission speed.
P16.n.03
– Data format. 7 bit settings can be used for ASCII protocol only.
P16.n.04
– Stop bit number.
P16.n.05
– Select communication protocol.
P16.n.06...P16.n.08
– TCP-IP coordinates for Ethernet interface applications. Not used with other types of communication modules.
P16.n.09
– Role of the communication channel.
Slave
= Slave Modbus.
Gateway
= Bridge between the Ethernet and serial ports.
Mirror
= Remote panel mirror (reserved/function not operative yet).
Master
= RS485 port used for the command of the steps (available only for DCTL thyristor modules).
P16.n.10
– Enabling TCP-IP connection.
Server
= Awaits connection from a remote client.
Client
= Establishes a connection to the remote server.
P16.n.11...P16.n.13
– Coordinates for the connection to the remote server when P16.n.10 is set to Client.
M17 – BASIC PROTECTIONS UoM Default Range
P17.01 Temperature unit of measure °C °C / °F
P17.02 Internal panel temperature measurement source Internal sensor Internal sensor /
AINx
P17.03 Channel number x 1 1-99
P17.04 Fan start temperature ° 50 0-212
P17.05 Fan stop temperature ° 45 0-212
P17.06 Internal panel temperature alarm threshold ° 55 0-212
P17.07 Capacitor current overload ON OFF - ON
P17.08 Capacitor current overload threshold % 125 OFF / 100 – 150
P17.09 Immediate step disconnection threshold % 150 OFF / 100 – 200
P17.10 Current overload alarm reset time min 5 1 – 30
P17.11 Step trimming OFF OFF - ON
P17.12 Faulty step alarm threshold % OFF OFF / 25…100
P17.13 Maximum voltage threshold % 120 OFF / 90...150
P17.14 Minimum voltage threshold % OFF OFF / 60..110
P17.02
– Defines which sensor is providing the temperature measurement inside the panel:
Internal sensor
– Sensor built into the controller;
AINx
– Temperature by PT100 input on EXP1004 expansion module.
P17.03
– Channel number, relative to the previous parameter.
P17.04 – P17.05
- Start and stop temperature for the cooling fan of the panel, expressed in the unit set by P17.01. It is also possible to force the fan to start for a time of 30 seconds by going to the dedicated
temperature page and holding down the
◄
button for three seconds.
P17.06
– Threshold for alarm generation A07 Panel temperature too high.
P17.07
– Enables the measurement of the capacitor current overload, calculated from the waveform of the applied voltage.
Note:
This protection can only be used if the capacitors are not equipped with filtering devices such as inductors or similar.
P17.08
– Trip threshold of capacitor overload protection (alarm A08) triggered after a integral delay time that is inversely proportional to the overload value.
P17.09
– Threshold beyond which the overload tripping integral delay is zeroed, causing the immediate tripping of the protection and alarm.
P17.10
– Delay time for the overload alarm resetting.
P17.11
– Enables the measurement of the actual power of the steps, performed each time they are connected. The measurement is calculated, since the current drawn is referred to the whole load of the installation.
The measured power of the steps is adjusted (trimmed) after each switching and is displayed on the step life statistics page.
P17.12
– Percentage threshold of the residual power of the steps, compared with the original power programmed in main menu. Below this threshold, alarm A10 step failure is generated.
P17.13
– Maximum voltage alarm threshold, referred to the rated voltage set with P02.21, above which alarm A06 Voltage too high is generated.
P17.14
– Undervoltage alarm threshold, referred to the rated voltage set with P02.21, below which alarm A05 voltage too low is generated.
G
B