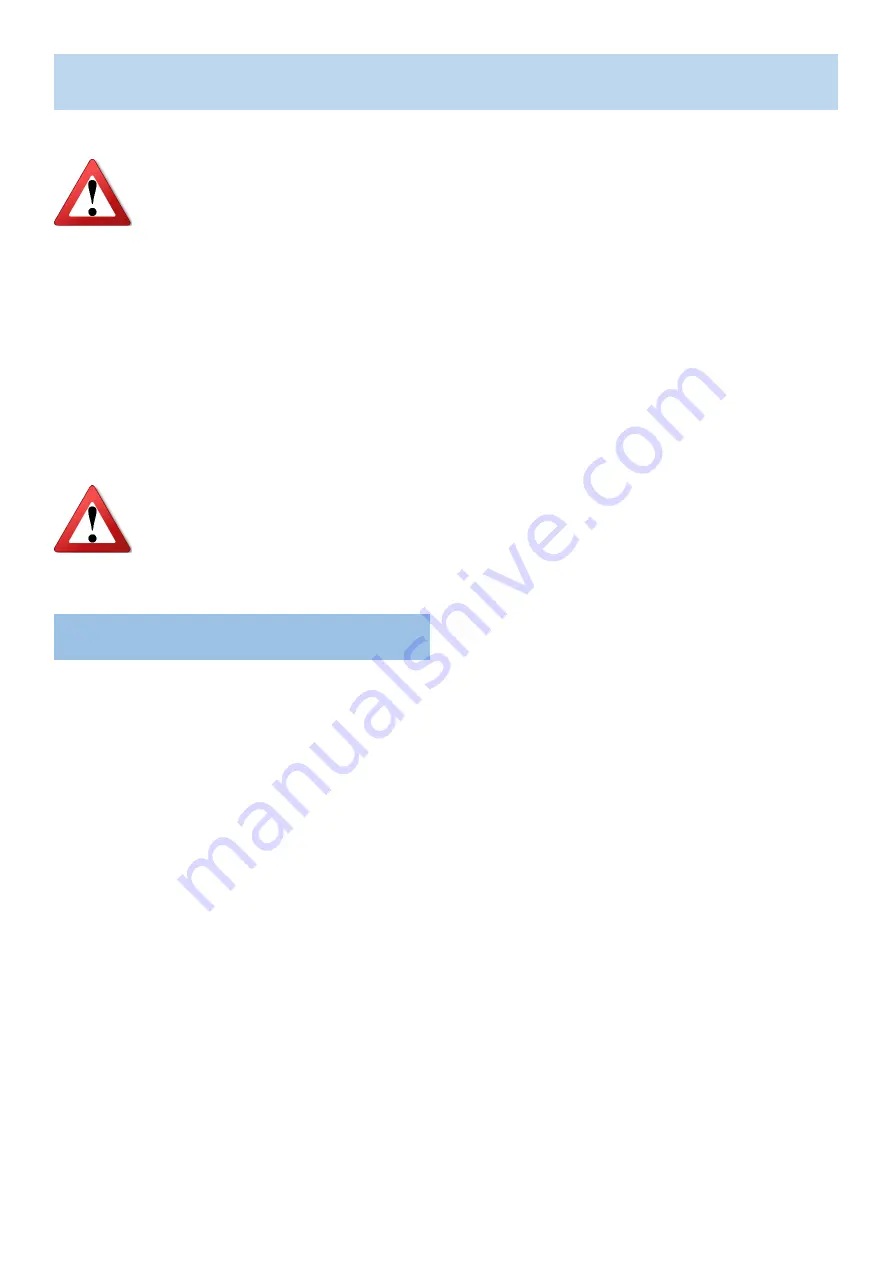
SAFETY WARNINGS AND PRECAUTIONS
PLEASE
READ
AND
UNDERSTAND THE FOLLOWING
SAFETY
HIGHLIGHTS.
BE
SURE THAT ALL INSTALLATION,
OPERATION, MAINTENANCE AND REPAIR
PROCEDURES ARE PERFORMED ONLY BY
QUALIFIED INDIVIDUALS. ARC AND TIG
WELDING CAN BE HAZARDOUS. PROTECT
YOURSELF AND OTHERS FROM POSSIBLE
SERIOUS INJURY OR DEATH. KEEP
CHILDREN AWAY. PACEMAKER WEARERS
SHOULD CONSULT WITH THEIR DOCTOR
BEFORE OPERATING
WHEN USING THE WELDER, ALL
BASIC SAFETY PRECAUTIONS
SHOULD ALWAYS BE FOLLOWED
TO REDUCE THE RISK OF PERSONAL
INJURY AND DAMAGE TO EQUIPMENT.
READ ALL INSTRUCTIONS BEFORE
USING THIS WELDER.
Keep work area clean.
Cluttered areas
invite injuries.
Observe work area conditions.
Do not
use machines or power tools in damp or wet
locations. Do not expose to rain. Keep work
area well-lighted. Do not use electrically
powered tools in the presence of flammable
gases or liquids.
Keep children away.
Children must be
never allowed in the work area. Do not let
them handle machines, tools or extension
cords.
Store idle equipment.
When not in use,
tools must be stored in a dry location to
inhibit rust.
Always lock up
tools and keep them out of
the reach of children.
Do not force tool.
It will do the job better
and safer at the rate for which it was
intended. Do not use inappropriate
attachments in an attempt to exceed the
tool capacity.
Use the right tool for the job.
Do not
attempt to force a small tool or attachment
to do the work of a larger industrial tool.
There are certain applications for which this
welder was designed. Do not modify this
welder and do not use this welder for any
other purposes for which it was not intended.
Dress properly.
Do not wear loose clothing
or jewelry as they can be caught in moving
parts.
Protective,
flame
retardant,
electrically non-conductive clothing and
non-skid footwear are recommended when
working. Wear restrictive hair covering to
contain long hair.
Use eye and ear protection.
Always wear
ANSI approved, arc shaded, impact safety
face shield (welding helmet). Always use a
full-face shield when welding. Always wear
ANSI approved eyewear under face shield
and while in the workplace. Wear a NIOSH
approved dust mask or respirator when
working around metal, chemical dusts,
fumes and mists.
Do not over reach.
Keep proper footing
and balance at all times. Do not reach over
or across running machines.
Maintain tools with care.
Keep tools sharp
and clean for better and safer performance.
Follow instructions for lubricating and
changing accessories. Inspect tool cords
periodically and, if damaged, have them
repaired by an authorized technician. The
handles must be kept clean, dry, and free
from oil and grease at all times.
Disconnect power.
Unplug tool when not
in use.
Remove adjusting keys and wrenches.
Check that keys and adjustment wrenches
are removed from the welder and work area
before plugging in.