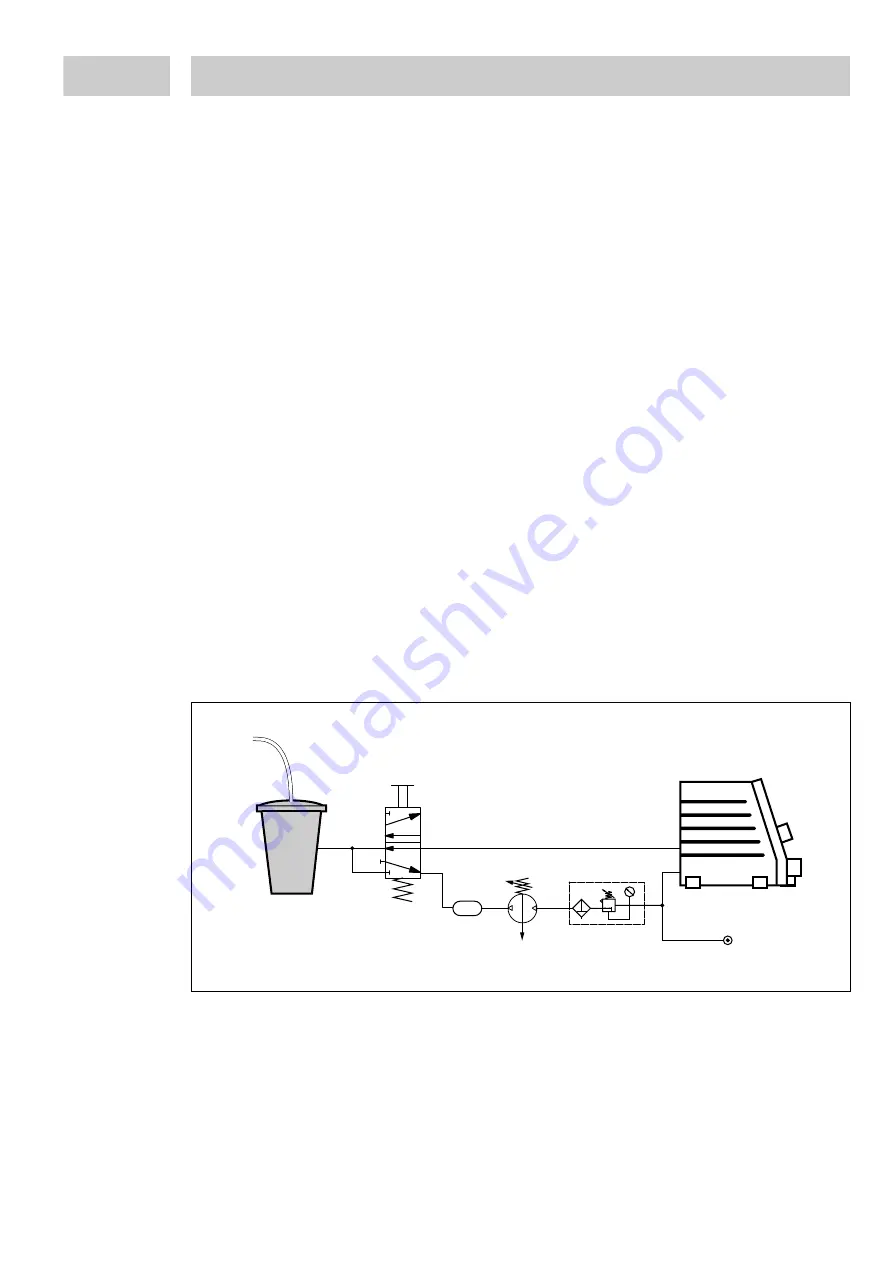
11
5 Dispensing
5.1 Flushing
To avoid troubles caused by air bubble the product feedline and the VoluDrop Dispenser
must be filled and then purged of air.
Generally, flushing has to be done for the initial startup and also, depending on the
adhesive, in regularly time lags.
Air bubbles can result in the following troubles:
– no or too little product or
– dispenser does not spit.
For easier handling an external possibility of switching between the reservoir pressure
and the necessary flushing pressure should be implemented. It consists of 1 manual
actuated switch-over valves (5/2-way valves, button actuated, fumbling, not resting) and
a connection to the pressure supply of more than 7 bar (100 psi).
See also pneumatic diagram section 8.
The 5/2-way valve is used as a switch-over valve for switching between the
product pressure (reservoir pressure 0.6 - 0.8 bar / 8.7 - 11.6 psi) and the
flushing pressure min. 7 bar (100 psi), max. 8 bar (116 psi).
Basic position of the switch-over valve is in position
reservoir pressure from the controller 0.6 - 0.8 bar.
A compressed air pressure of 7 - 8 bar (100 - 116 psi) is necessary to override the
integrated non-return valve 2. If it is not available an additionally pressure multiplicator
has to be used. To limit the pressure at 8 bar a LOCTITE filter regulator order no. 97120
or a comparable one is necessary. Otherwise the integrated burst plate of the reservoir
can burst (lower burst limit 8.8 bar / 125 psi).
Flushing Procedure
•
Mount the components according to the graphic below.
Place a container under the dispenser. Product will flow out!
•
Press switch-over valve and keep it pressed. The reservoir will be pressurized
with min. 7 bar.
•
Start dispensing for several times.
•
Switch over to 0.6 – 0.8 bar by releasing the valve.
•
The reservoir will be vented due to the pressure regulator of the controller.
•
Wait a short time till the correct pressure 0.6 – 0.8 bar is present.
Dispensing can be continued.
Switch-over
Valve
min. 7 bar (100 psi)
max. 8 bar (116 psi)
0.6 - 0.8 bar
(8.7 - 11.6 psi)
Feedline
Reservoir
Controller
97120
I
0
5
1
2
3
4
Summary of Contents for VoluDrop UV 97650
Page 1: ...Operating Manual VoluDrop Dispenser UV 97650 ...
Page 2: ...2 Contents English 3 16 ...
Page 17: ...17 8964739 03 2003 ...